высокотемпературный конденсаторный датчик приближения
- time:2025-07-06 02:12:40
- Нажмите:0
Surviving the Inferno: How High-Temperature Capacitive Proximity Sensors Revolutionize Industrial Sensing
Imagine a production line where molten metal flows, furnaces roar, or glass glows red-hot. Critical processes depend on precise object detection and positioning, but the searing heat fries standard sensors within minutes. This is the daily reality in industries pushing the boundaries of temperature, a reality where traditional sensing fails. Enter the unsung hero: the high-temperature capacitive proximity sensor. Engineered for resilience, this advanced technology is unlocking new levels of automation, safety, and efficiency in the hottest corners of manufacturing and beyond.
Unlike their optical or inductive counterparts, capacitive proximity sensors operate by detecting changes in an electrical field surrounding their active face. When an object enters this field, it alters the capacitance, triggering the sensor’s switching output. This non-contact, material-agnostic principle is inherently robust. However, standard capacitive sensors typically max out around 70-85°C – useless near a casting line or inside an engine test cell. High-temperature capacitive proximity sensors shatter this limit, reliably functioning in ambient environments often exceeding 150°C, 200°C, or even higher, depending on the specific design.
Why is this high-temperature capability so crucial? The answer lies deep within demanding industrial applications:
- Metal Processing & Foundries: Near molten metal handling, die casting machines, forging presses, and continuous casting lines, ambient temperatures soar. Sensors must detect molds, ladles, billets, or presence of materials without succumbing to the intense radiant heat.
- Automotive Manufacturing: Engine testing cells, exhaust system assembly, paint curing ovens, and brake disc production generate extreme heat. Reliable proximity detection is vital for robotic handling, part positioning, and process verification within these zones.
- Glass & Ceramics Manufacturing: Forming, annealing lehrs, and tempering furnaces operate at blistering temperatures. Sensors monitor glass sheets, molds, and conveyor positions critical to quality and throughput.
- Plastics & Rubber Processing: Extrusion lines, vulcanization presses (for tires), and injection molding machines involve high heat. Proximity sensors ensure material feed, mold closure verification, and ejection timing.
- Power Generation & Chemical Processing: Monitoring components inside turbines, boilers, or reactor vessels requires sensors unfazed by sustained high ambient temperatures.
- Аэрокосмическая деятельность: Engine component testing and manufacturing environments demand sensors capable of withstanding intense thermal conditions.
The Engineering Marvel: Surviving Extreme Heat
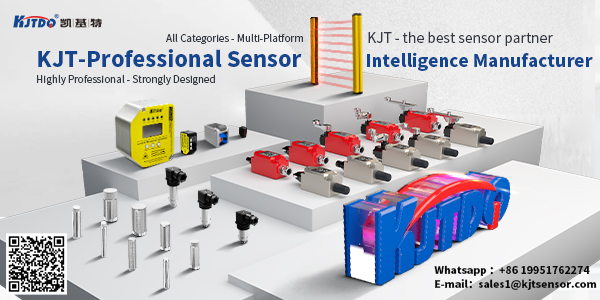
Creating a sensor that functions accurately at 200°C+ is no small feat. Standard electronic components and materials simply melt or degrade. High-temperature capacitive sensors incorporate several key innovations:
- Specialized Substrate Materials: Instead of standard FR4 PCB material, these sensors use ceramics (like Alumina - Al2O3) or high-temperature laminates that maintain structural integrity and electrical properties under thermal stress. Substrate selection is paramount for longevity.
- High-Temperature Solders & Components: Conventional solder melts at relatively low temperatures. Sensors rated for extreme heat use specialized high-temperature solders and carefully selected electronic components (capacitors, resistors, semiconductors) specifically graded for operation in continuous high ambient temperatures.
- Robust Hermetic Sealing: Preventing internal condensation during cool-down cycles and protecting delicate internals from harsh atmospheres (potentially corrosive) is critical. Ceramic hermetic sealing and specialized, heat-resistant potting compounds create a formidable barrier.
- Advanced Sensing Electrode Design: The electrode pattern generating the sensing field is optimized for performance in challenging thermal environments, often employing stable metallic alloys resistant to oxidation at high temperatures.
- Thermal Management: Strategic design considerations help dissipate internal heat buildup and minimize thermal gradients that could affect sensing accuracy or damage components. The sensor’s form factor often incorporates heat sinks or thermal barriers.
Why Choose Capacitive in the Heat?
While other sensing principles (like certain optical or inductive variants) can also be hardened for high temperatures, capacitive offers distinct advantages:
- Material Agnosticism: Detects metals, plastics, glass, wood, liquids, granules – whatever the hot process requires sensing. This flexibility is invaluable compared to inductive sensors, which only detect metals.
- Non-Contact Operation: Eliminates wear and tear, crucial in dusty or abrasive high-temperature environments.
- Sensitivity Adjustment: Many models allow tuning the sensing range or sensitivity to handle different target materials or counteract environmental effects, providing vital operational flexibility.
- Compact Form Factors: Available in cylindrical or block styles to fit into tight spaces within machinery, even near heat sources.
- Sealed Construction: Inherently suited to washdown or harsh environments often accompanying high heat, especially with high IP ratings (e.g., IP67, IP69K).
Selecting the Right High-Temperature Capacitive Sensor
When integrating these sensors into extreme environments, consider these critical factors:
- Maximum Ambient Temperature: This is the defining specification. Ensure the sensor’s rating comfortably exceeds your application’s actual peak ambient temperature, including any radiant heat load. Margin is safety.
- Sensing Range: Verify the required detection distance is achievable under the operating conditions. Heat can slightly influence range.
- Electrical Requirements: Voltage supply (DC or AC), output type (PNP/NPN, NO/NC), and current rating must match your control system.
- Connection & Cable: Ensure the cable jacket material (e.g., Teflon, Silicone) and connector are also rated for the high temperature. Integral cables or high-temp connectors are common.
- Environmental Sealing (IP Rating): Protection against dust, water, and potentially coolants or oils is often essential. IP67 or IP69K is typical for demanding settings.
- Housing Material: Stainless steel (e.g., 303, 304, 316) housings are standard for corrosion resistance and robustness in industrial settings. Consider chemical exposure compatibility.
- Compliance & Certifications: Look for relevant industry standards (CE, UL, ATEX/IECEx for hazardous areas if needed).
The Future is Hot (and Well-Sensed)
High-temperature capacitive proximity sensors are not just niche components; they are fundamental enablers for automating processes previously deemed too harsh for reliable sensing. By pushing the boundaries of material science and electronic design, these sensors bring precision, reliability, and safety to the most thermally demanding industrial frontiers. As technologies advance, we can expect even higher temperature ratings, greater miniaturization, enhanced diagnostic capabilities, and seamless integration with Industry 4.0 networks. For engineers battling the inferno, these sensors are the indispensable eyes and ears, thriving where others fear to tread. Their ability to deliver robust, non-contact detection across diverse materials in relentless heat is truly transforming manufacturing capabilities.