Линейный датчик движения
- time:2025-07-06 02:18:41
- Нажмите:0
Linear Motion Sensors: The Silent Backbone of Precision Automation
Imagine the conductor of a vast, intricate orchestra. Unseen yet essential, they ensure every instrument plays perfectly in time and place. In the realm of automation and machinery, linear motion sensors fulfill a remarkably similar role. These vital components are the eyes and ears of modern movement control systems, silently and precisely monitoring the straight-line position and velocity of objects with remarkable accuracy. From robotic arms assembling your smartphone to CNC machines carving complex components, linear motion measurement is fundamental to countless industrial and technological processes.
What Exactly is a Linear Motion Sensor?
At its core, a Линейный датчик движения (often referred to as a linear position sensor, linear encoder, or linear displacement transducer) is a device designed to detect and measure movement along a single, straight axis. Unlike rotary sensors that measure angular movement (like a spinning shaft), linear sensors track linear displacement – how far something has moved in a straight line, and sometimes how fast (linear velocity) or even how fast that speed is changing (linear acceleration).
These sensors convert the physical phenomenon of movement into an electrical signal – typically analog (voltage or current) or digital (serial communication like SSI or digital pulses) – that control systems can interpret. This real-time feedback is absolutely critical for:
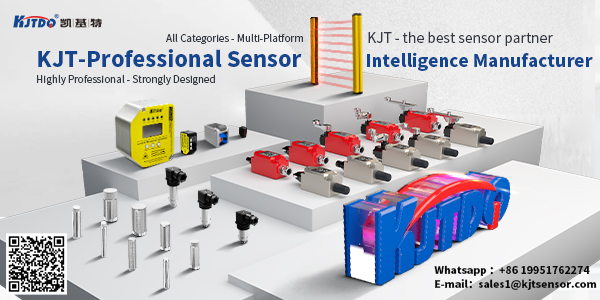
- Closed-Loop Control: Motion control systems rely on sensor feedback to compare the actual position of a machine element (like a tool head or carriage) to its commanded position. Any deviation triggers a correction, ensuring high-precision movement.
- Position Verification: Confirming that a component has reached its intended destination before proceeding to the next step in a process.
- Speed and Velocity Control: Monitoring and regulating the rate of linear movement.
- Safety Functions: Detecting limit positions to prevent over-travel and potential damage or accidents.
Key Technologies Powering Linear Sensing
The need for accuracy, reliability, and resilience across diverse environments has led to the development of several core linear position sensing technologies. Understanding their differences is crucial for selecting the right sensor:
- Magnetic Linear Position Sensors: Utilize the interaction between a magnetic field and Hall effect sensors or magnetoresistive elements. A magnet mounted on the moving target moves relative to a stationary sensor head. Advantages include excellent tolerance to dirt, dust, oil, and vibration, non-contact operation, and relatively low cost. Resolution can be very high with advanced configurations. They are widely used in hydraulic cylinders, factory automation, and material handling.
- Inductive Linear Position Sensors (LVDT - Linear Variable Differential Transformer & RVDT - Rotary Variant): These work on electromagnetic induction principles. An AC current energizes a primary coil, inducing voltages in secondary coils. The position of a movable ferromagnetic core alters the coupling, changing the output voltage proportionally. They offer exceptional accuracy, infinite resolution, true absolute position, and robust operation in harsh industrial environments. Common applications include high-precision machine tools, aerospace actuators, and critical industrial controls.
- Optical Linear Encoders: Employ a scale (glass or metal) with finely etched gratings and a read head containing a light source and photodetectors. As the read head moves relative to the scale, light patterns are interrupted, generating digital signals (quadrature pulses) that indicate position and direction. They provide the highest resolutions (sub-micron) and speeds but can be sensitive to contamination and require careful mounting. Dominant in semiconductor manufacturing, metrology, and high-end CNC equipment.
- Capacitive Linear Sensors: Measure changes in capacitance between fixed plates and a plate attached to the moving object. Distance changes alter the capacitance. They offer high resolution, low power consumption, and are non-contact, but performance can be affected by material properties and environmental factors like humidity. Often found in laboratory instruments and cleanroom applications.
- Potentiometric (Resistive) Linear Sensors: The simplest form, using a sliding contact (wiper) moving along a resistive element, changing resistance proportionally to position. Low cost and simple to use, but wear and limited lifespan due to physical contact can be drawbacks for demanding applications. Suitable for non-critical position feedback where cost is paramount and cycle life is low.
Selecting the Right Linear Motion Sensor: Key Considerations
Choosing the optimal linear position transducer isn’t a one-size-fits-all proposition. Several critical factors must be evaluated against the application’s needs:
- Required Accuracy and Resolution: How precise does the measurement need to be? Sub-micron, micron, or millimeter level?
- Measuring Range: What distance needs to be covered?
- Environmental Conditions: Will the sensor be exposed to extreme temperatures, shock, vibration, humidity, dirt, oil, or chemicals? (Magnetic sensors excel in dirty environments; optical encoders typically need protection.)
- Speed of Movement: Does the application involve high velocities or rapid acceleration/deceleration?
- Output Signal: What type of interface does the control system require (analog voltage/current, digital pulses, serial communication)?
- Mounting Requirements: How much space is available? What mounting configuration is feasible?
- Cost: What is the budget constraint?
- Absolute vs. Incremental: Does the system need to know its absolute position immediately upon power-up (absolute encoders/sensors), or can it reference a home position after startup (incremental encoders)?
Ubiquitous Applications: Where Linear Motion Sensing Drives Progress
Linear motion measurement is indispensable across a staggering array of industries:
- Промышленная автоматизация: Robotic arms positioning tools or parts, conveyor belt tracking, pick-and-place machine accuracy, automated guided vehicles (AGVs), printing presses, packaging machinery, and 3D printers all rely heavily on these sensors.
- Machine Tools (CNC): Ensuring the precise positioning of cutting tools relative to the workpiece in milling machines, lathes, grinders, and laser cutters is fundamental to manufacturing quality.
- Semiconductor Manufacturing: Building chips at the nanometer scale demands the extreme precision provided by high-end optical encoders.
- Medical & Laboratory Equipment: Medical imaging devices (MRI, CT scanners), robotic surgery systems, IV pumps, and analytical instruments utilize linear sensors for precise component movement.
- Automotive & Aerospace: Testing equipment, throttle and brake position sensing, actuation systems (landing gear, flaps), and manufacturing robots.
- Hydraulics & Pneumatics: Monitoring and controlling the position of cylinders in construction equipment, agricultural machinery, and industrial presses.
The Future: Smarter, More Integrated Sensing
The evolution of linear motion sensors continues apace. We see trends towards smart sensors with integrated processing capabilities, enabling onboard diagnostics and simplified wiring. Wireless communication options are emerging for challenging installations. Integration with Industrial Internet of Things (IIoT) platforms allows for predictive maintenance and deeper process optimization. Furthermore, miniaturization persists, opening doors for applications in ever-smaller devices, including sophisticated consumer electronics.
Their silent, unassuming nature belies their profound impact. Linear motion sensors remain an essential technology, providing the critical feedback loop that transforms potential movement into controlled, precise, and reliable automation – the very foundation of modern manufacturing and innovation.