efector proximity sensor
- time:2025-07-04 01:06:28
- Нажмите:0
Effector Proximity Sensors: The Silent Guardians of Robotic Precision and Safety
Imagine a high-speed robotic arm, deftly maneuvering within millimeters of delicate components, or an autonomous guided vehicle (AGV) smoothly navigating a crowded warehouse aisle. This ballet of metal and motion relies on an unseen sentinel: the effector proximity sensor. Far more than a simple switch, these sensors are the essential touchless guardians enabling efficiency, preventing costly collisions, and ensuring seamless automation.
Demystifying the Effector and Its Needs
Before diving deeper, let’s clarify “effector.” In robotics and automation, the effector is the end-of-arm tooling (EOAT) – the business end of the robot arm. This could be a gripper, a welding torch, a suction cup, a dispensing nozzle, or any tool performing a specific task. The effector interacts directly with the work environment, making it the most vulnerable point for unintended contact.
This is where effector proximity sensors come in. Mounted directly on or very near the effector itself, their primary function is non-contact object detection in the immediate vicinity. They provide critical real-time feedback about the environment before physical contact occurs.
How Effector Proximity Sensors Work: Seeing Without Touching
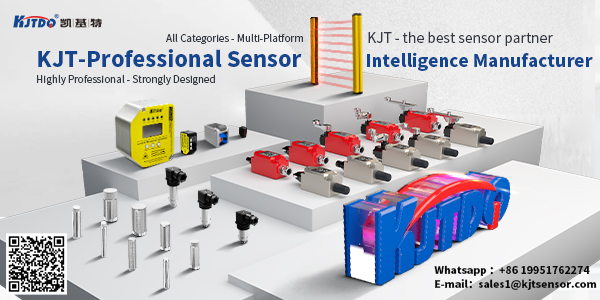
Effector proximity sensors operate on several well-established principles, chosen based on the application:
- Inductive Proximity Sensors: Detect the presence of metallic objects. They generate an electromagnetic field; when a metal target enters this field, it induces eddy currents, causing a detectable change in the sensor’s oscillation. Ideal for detecting metal parts, gripper jaws, or tool changers. Key benefits include robustness and insensitivity to dust or oil (though not immune to metal chips).
- Capacitive Proximity Sensors: Detect the presence of almost any material (metal, plastic, wood, liquid, granules) by sensing changes in capacitance. The sensor forms one plate of a capacitor; the target object (or a change in dielectric constant) forms the other. Changes in this capacitance trigger the sensor. Perfect for detecting non-metallic objects, fill levels in containers near the effector, or presence of materials like plastic or wood.
- Optical Proximity Sensors (Diffuse Reflective): Emit a light beam (visible, infrared, or laser) and detect the reflection from an object. The distance at which an object can be reliably detected depends on the sensor’s power, optics, and the reflectivity of the target. Excellent for detecting small objects, various colors (depending on type), and offering precise, non-contact detection at slightly longer ranges than inductive or capacitive sensors near the effector. Susceptible to interference from ambient light or highly reflective/absorbent surfaces.
The Indispensable Value Proposition: Why Effector Mounting is Critical
Mounting proximity sensors directly on the effector unlocks unique advantages crucial for modern automation:
- Collision Avoidance: This is paramount. An effector proximity sensor acts as the first line of defense, detecting obstacles (other robots, machinery, fixtures, humans, misplaced parts) immediately in the path or working zone of the effector. This allows the control system to halt motion instantly or trigger an evasive maneuver, preventing expensive damage to the robot, tooling, or workpiece. The cost savings from preventing just one major collision can far outweigh the sensor investment.
- Enhanced Precision and Process Control: Detecting the presence, absence, or precise position of a part right at the point of interaction is vital. Did the gripper successfully pick up the component? Is the part correctly seated in the fixture before welding? Is the dispensing nozzle at the correct height above the surface? Effector proximity sensors provide this instantaneous feedback, ensuring process reliability and reducing errors.
- Part Verification and Positioning: Ensuring the right part is present and oriented correctly before the effector engages is critical. Proximity sensors on the effector can verify part features, height, or simple presence, preventing misoperations downstream.
- Tool Change Verification: In systems with automatic tool changers, sensors on the effector or tool holder confirm the successful engagement and locking of the new tool, preventing a robot from operating without the correct tool or with a loose tool.
- Guarding Complex Geometries: Effectors often have intricate shapes. Strategically placing small proximity sensors on the effector allows for guarding specific vulnerable protrusions or corners that larger fixed guards might miss.
- Enabling Delicate Operations: In tasks requiring extreme precision or handling fragile items (e.g., electronics assembly, food handling), the immediate feedback from an effector proximity sensor allows for gentle, controlled approaches and manipulations, impossible with slower feedback loops from sensors farther away.
Applications: Where Effector Proximity Sensors Shine
Their versatility makes them ubiquitous across automation:
- Роботизированная рука: Picking/placing, machine tending, assembly, welding, dispensing, painting, inspection.
- Autonomous Mobile Robots (AMRs) & AGVs: Obstacle detection for manipulator arms on mobile platforms, low-level guarding near the effector during operation.
- Packaging Machinery: Verifying presence of items before sealing, controlling position of sealing heads.
- CNC Machining Centers: Tool breakage detection, part presence verification in pallets or fixtures near the spindle.
- Перевозка материалов: Detecting bin-picking success, monitoring gripper open/close positions, preventing jams.
Integration and Selection Considerations
Successfully leveraging effector proximity sensors requires thoughtful integration:
- Mounting: Sensors must be securely attached to withstand robot motion, vibrations, and potential incidental contact. Compact designs are essential.
- Environment: Consider temperature extremes, exposure to coolants, oils, dust, welding sparks, or washdowns. Choose sensors with appropriate IP (Ingress Protection) ratings (e.g., IP67, IP69K).
- Target Material and Size: Dictate whether inductive, capacitive, or optical sensing is best suited. Consider the minimum detectable object.
- Required Sensing Distance: The needed range influences sensor type and model selection.
- Output Type: PNP/NPN, NO/NC outputs must match the robot or PLC input requirements.
- Cabling: Flexible, highly durable cabling is crucial to withstand constant effector movement; consider modular connectors for easy replacement. Robust strain relief is mandatory.
Selecting the Right Guardian
Choosing the optimal effector proximity sensor involves balancing factors like detection principle, target characteristics, environmental conditions, required sensing range, physical size constraints, and output compatibility. Consult manufacturer datasheets carefully and prioritize sensors designed specifically for the harsh realities of robotic motion.
Conclusion: The Unseen Enabler
While often small and unobtrusive, the effector proximity sensor plays an outsized role in the world of automation. By providing critical, instant, non-contact detection right at the point of interaction, they are fundamental to achieving the levels of safety, precision, efficiency, and reliability demanded by modern manufacturing, logistics, and beyond. They are the silent, vigilant guardians ensuring robots dance their complex routines with grace and without mishap, proving that the smallest components often bear the greatest responsibility.