balluff laser distance sensor
- time:2025-07-04 01:12:30
- Нажмите:0
Balluff Laser Distance Sensors: Precision Measurement Powering Modern Industry
Imagine this: A robotic arm smoothly glides across an automotive assembly line, effortlessly placing a windshield into its frame. A crucial quality check verifies the precise gap dimension between complex metal components without physical contact. High-speed packaging machinery adjusts flawlessly to varying product sizes. At the heart of these demanding industrial processes often lies a critical, unsung hero: the Balluff laser distance sensor. These sophisticated devices deliver exceptional precision, robust reliability, and unparalleled versatility in non-contact measurement, solidifying their position as indispensable tools across countless industries.
So, how do these remarkable sensors achieve such feats? Balluff laser distance sensors primarily utilize either the triangulation method or time-of-flight (ToF) measurement principle.
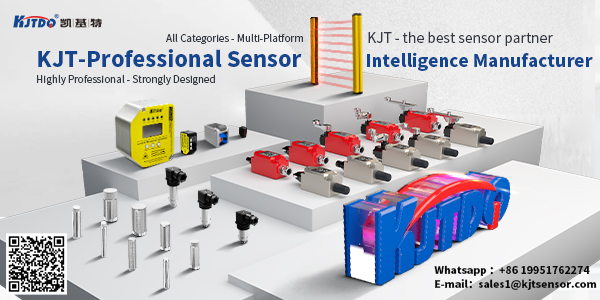
- Triangulation Sensors: Emit a focused laser point onto the target surface. The reflected light hits a receiving element (like a CCD or CMOS array) at an angle relative to the emitter. The position of the reflected spot on this array directly corresponds to the distance to the target. This method is renowned for delivering extremely high resolutions, often down to the micrometer range, making them ideal for demanding short-range applications requiring sub-millimeter accuracy (e.g., ±0.05mm). Balluff offers these as compact, high-precision solutions perfect for intricate positioning tasks.
- Time-of-Flight (ToF) Sensors: Measure the time it takes for a laser pulse to travel to the target and back. Since the speed of light is constant, this time measurement provides a direct calculation of the distance. This technology excels at measuring longer ranges – from several meters up to hundreds of meters – even on challenging surfaces. While potentially offering slightly lower resolution than triangulation at close range, ToF sensors like Balluff’s BOD series are incredibly robust, fast, and designed for industrial environments, providing reliable long-range distance data critical for level monitoring or large object positioning.
The significant advantages of Balluff laser distance sensors stem directly from their underlying laser technology and robust design:
- Non-Contact Measurement: The fundamental benefit. Physically touching a target is eliminated, preventing damage to delicate surfaces, avoiding sensor wear, and enabling measurements on hot, vibrating, or hazardous objects.
- Exceptional Accuracy and Resolution: Balluff laser sensors provide pinpoint precision, whether it’s the ultra-fine resolution of triangulation sensors or the reliable accuracy of ToF sensors over distance. This is paramount for quality control, positioning, and automated processes where tolerances are tight. Consistent, trustworthy data is non-negotiable.
- High Speed and Responsiveness: Laser light travels fast! Balluff sensors offer incredibly rapid measurement cycles often in the microsecond or millisecond range, enabling real-time process control and monitoring even on high-speed production lines.
- Robustness for Industrial Environments: Designed for the factory floor. Balluff encases its laser distance sensors in rugged metal housings, often featuring high IP protection ratings (like IP67, IP69K) for resistance to dust, moisture, oils, and washdowns. They withstand significant shock and vibration, ensuring longevity and reliability where other sensors might fail.
- Ability to Measure Diverse Surfaces: While performance varies, Balluff laser sensors generally handle challenging surfaces better than many optical alternatives. Specialized models or settings can effectively measure dark, shiny, or transparent objects – a common hurdle in industrial settings. Advanced evaluation functions within the sensors intelligently filter out background noise and interference.
- Compact Design and Flexible Integration: Space is often limited. Balluff offers a range of compact laser distance sensors suitable for confined mounting locations. Furthermore, standardized interfaces like IO-Link provide not just distance readings but also a wealth of diagnostic data, simplifying integration, configuration, and predictive maintenance within modern IIoT/Industry 4.0 architectures.
The diverse capabilities of Balluff laser distance sensors translate into transformative solutions across a wide spectrum of industrial applications:
- Precise Positioning and Dimensioning: Verifying part presence, position, height, or diameter. Ensuring components are correctly assembled (e.g., gap measurement on car doors, windshields). Measuring object dimensions for sorting or packaging. Their accuracy is crucial for tolerances measured in fractions of a millimeter.
- Robotics and Automation: Providing essential feedback for robotic guidance, enabling tasks like precise picking/placing, seam tracking (with specialized sensors), and synchronized motion with moving targets or conveyors. Critical for flexible automation.
- Logistics and Material Handling: Palletizing/depalletizing verification, stack height measurement, warehouse crane positioning, and conveyor object detection/sizing. Long-range ToF sensors excel here.
- Quality Assurance & Process Control: Performing non-contact inspections – thickness, warpage, fill level, or profile checks – directly on the production line, enabling real-time feedback and immediate process correction. Detecting even minute deviations ensures consistent quality.
- Level Monitoring: Measuring the fill level of bulk solids in silos or liquids in tanks (especially using long-range ToF sensors). A vital application demanding reliability.
- Roll Diameter Measurement: Accurately measuring large rolls in paper, foil, or textile production without contact. Balluff offers specialized sensors tailored for this exact task.
- Handling Transparent Objects: Unique configurations allow reliable detection and measurement of glass bottles, plastic films, or vials – surfaces that trip up many other sensor types.
Choosing the right Balluff laser distance sensor involves careful consideration of several factors guided by the specific application need:
- Required Range and Accuracy: Pinpointing the minimum/maximum distance and the necessary precision level dictates the suitable technology (triangulation vs. ToF).
- Target Surface Characteristics: The material, color, and surface finish (matte, shiny, transparent) influence sensor choice and performance.
- Environmental Conditions: Ambient light levels, exposure to dust/moisture/washdown, and potential shock/vibration dictate the required robustness and IP rating.
- Measurement Speed: How rapidly does the sensor need to update its reading? High-speed processes demand high-speed sensors.
- Output Requirements: Does the system need a simple switch signal, analog output (4-20mA, 0-10V), or digital communication like IO-Link for richer data?
- Mounting Constraints: Physical size and mounting options (bracket availability).
In the relentless pursuit of efficiency, quality, and automation, Balluff laser distance sensors represent a cornerstone technology. By harnessing the focused power of light, they deliver unrivaled non-contact measurement performance – accuracy, speed, and reliability – where it matters most. Whether it’s ensuring the perfect fit of a luxury car component, guiding a robot with micron-level precision, monitoring critical silo levels, or verifying packaging integrity at blistering speeds, Balluff laser sensors provide the critical data foundation. Their robust construction ensures they thrive in demanding industrial environments, while flexible interfaces and IO-Link capabilities make them integral components of smart factories. For engineers and integrators deploying automation, understanding and leveraging the power of a Balluff laser distance sensor is fundamental to unlocking new levels of performance and control.