festo proximity sensor
- time:2025-07-04 00:36:18
- Нажмите:0
Unseen Guardians: How Festo Proximity Sensors Power Reliable Industrial Automation
Imagine a high-speed packaging line humming along, precisely placing products into boxes. Or a robotic arm performing intricate welding, millimeter-perfect, every single time. What invisible force ensures this flawless, efficient operation? Often, it’s the unsung heroes embedded within the machinery: Festo proximity sensors. These compact devices are fundamental pillars of modern automation, providing the critical detection that keeps systems running smoothly, safely, and predictably. Understanding their capabilities isn’t just technical detail; it’s key to unlocking peak performance in countless industrial applications.
Beyond Simple Switches: The Essence of Festo Proximity Detection
Unlike mechanical switches requiring physical contact, Festo proximity sensors operate contactlessly. They detect the presence or absence of a target object (metal, plastic, liquid, etc.) within a specific sensing range without touching it. This non-contact principle delivers significant advantages:
- Exceptional Reliability & Longevity: No moving parts mean minimal mechanical wear and dramatically reduced failure rates compared to mechanical switches. They thrive in millions of operation cycles.
- High-Speed Operation: Capable of detecting objects moving at very high speeds, making them ideal for fast-paced assembly lines and robotics.
- Resilience in Harsh Environments: Engineered to withstand industrial realities – dust, dirt, coolants, oils, vibrations, and significant temperature fluctuations are par for the course. Robust enclosures, often meeting МП67 ratings or higher, ensure dependable operation.
- Simplified Installation & Maintenance: Contactless sensing eliminates the need for complex actuation mechanisms and precise alignment tolerances required by mechanical alternatives. Their compact size allows integration even in confined spaces.
Decoding the Technology: Festo’s Sensing Arsenal
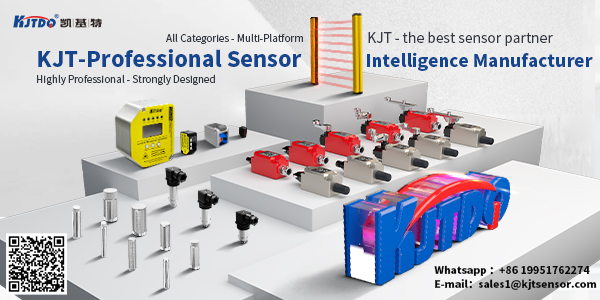
Festo offers a sophisticated range of proximity sensor technologies, each tailored to specific material types and environmental demands:
- Inductive Sensors (SIEN, SIE, SMT Series): The undisputed champions for detecting ferrous and non-ferrous metals. They generate an electromagnetic field. When a metal target enters this field, it induces eddy currents, causing a measurable change in the sensor’s oscillation. Key advantages include immunity to dirt, dust, and non-metallic contaminants, exceptional durability, and high switching frequencies. Ideal for position feedback on cylinders (piston detection), metal part presence on conveyors, and end-stop detection.
- Capacitive Sensors (SICT, SCE Series): Master detectors for nearly any material – metals, plastics, glass, wood, cardboard, liquids, and granules. They sense changes in an electrostatic field caused by the dielectric properties of a target entering the sensing zone. This makes them invaluable for level detection in tanks (liquids, powders), detecting non-metallic objects, or seeing through thin non-metallic container walls. Their versatility fills critical gaps where inductive sensors fall short.
- Magnetic Sensors (DNNI, SME Series): Specifically designed to detect the magnetic field generated by permanent magnets. Primarily used for piston position detection inside pneumatic cylinders where direct mounting or external triggers are impractical. They provide reliable binary signals confirming cylinder extension or retraction, crucial for sequencing logic.
- Photoelectric Sensors: While technically “proximity” in function for some variants, Festo’s photoelectrics (like the SOEG series) deserve mention. They use light beams (visible red, infrared, laser) for longer-range detection or specific object properties (color, contrast, transparency). Often used alongside inductive/capacitive sensors for comprehensive object handling tasks.
Why Festo Proximity Sensors Stand Out in the Automation Landscape
Choosing Festo for your proximity sensing needs brings distinct advantages beyond the core technology:
- Seamless System Integration: Festo sensors are designed as integral components within the Festo automation ecosystem. They connect effortlessly with Festo valves, controllers (CPX/MPA), drives, and software (Automation Suite). This simplifies design, commissioning, diagnostics, and maintenance significantly.
- Standardization & Flexibility: Offering both standard M8, M12, and M18 threaded cylindrical designs and innovative flat-pack formats, Festo provides immense mounting flexibility. Consistent connection methods (cable or connector versions) streamline cabling.
- Advanced Diagnostics & Communication: Modern Festo sensors often feature AS-Interface (AS-i) connectivity or IO-Link capability. This enables real-time sensor status monitoring, remote parameterization (e.g., adjusting sensitivity), predictive maintenance data, and simplified wiring structures, elevating overall system intelligence and uptime.
- Proven Durability & Quality: Manufactured to stringent industrial standards, Festo sensors are renowned for their long service life and consistent performance in demanding applications. This translates directly to reduced downtime and lower total cost of ownership.
- Application-Specific Expertise: Festo offers variants optimized for specific challenges, such as sensors with particularly long sensing ranges, extraordinarily high temperature resistance, or enhanced resistance to welding interference (for use near welding robots).
Powering Precision Across Industries: Where Festo Sensors Shine
The application landscape for Festo proximity sensors is vast and critical:
- Factory Automation & Robotics: Position feedback for robots and linear actuators, part presence/absence on conveyors, pallet detection, gripper status, machine guarding.
- Packaging & Handling: Detecting cartons, bottles, caps; verifying fill levels in containers; controlling product flow; end-of-stroke detection in pushers and lifters.
- Automotive Manufacturing: Monitoring component placement on assembly lines, verifying robot tooling positions, ensuring correct fixture clamping, detecting metal parts in welding cells.
- Food & Beverage Processing: Sanitary environment detection of containers (plastic, glass), level control in tanks (liquids, powders), presence detection on filling lines. Specific hygienic design options are available.
- Material Handling & Logistics: Detecting pallets, totes, and parcels on conveyors; verifying bin levels; controlling sorting gates; position sensing on stackers/cranes.
- Machine Tooling: Tool presence detection, workpiece clamping verification, coolant level monitoring, door position sensing.
Implementing Success: Key Considerations
Selecting the right Festo proximity sensor involves evaluating several factors:
- Target Material: Metal? Plastic? Liquid? Cardboard? (Inductive for metals, Capacitive for almost anything).
- Sensing Distance: Required gap between sensor and target (ensuring the chosen sensor’s nominal range is adequate).
- Operating Environment: Temperature extremes? Presence of dust, moisture, oils, chemicals? Electromagnetic interference? (Choose appropriate IP rating and housing material).
- Output Type & Connection: PNP/NPN switching? NO/NC? Cable or connector? AS-Interface/IO-Link needed?
- Mounting Constraints: Space limitations often dictate sensor shape (cylindrical vs. flat-pack) and size.
- Required Features: Need diagnostic LEDs? Adjustable sensitivity? High switching frequency? Welding immunity?
The Foundation of Unseen Efficiency
Choosing the right sensor technology is fundamental to building robust, efficient, and intelligent automation systems. Festo proximity sensors, backed by deep engineering expertise and seamless integration within a comprehensive automation platform, deliver the reliability, precision, and durability demanded by modern industry. Whether ensuring a cylinder has fully retracted, confirming a bottle is present for filling, or safeguarding a robotic cell, Festo’s proximity solutions are the unseen guardians enabling the smooth, continuous flow of automated processes. Investing in these critical components translates directly into enhanced productivity, minimized downtime, and greater operational confidence.