turck inductive sensor
- time:2025-07-04 00:42:23
- Нажмите:0
The Unseen Guardian: How Turck Inductive Sensors Revolutionize Industrial Automation
Imagine a critical production line grinding to a sudden, costly halt. Downtime ticks away at thousands per minute, all because a simple position sensor failed to detect a passing metal component. These failures aren’t just inconvenient; they represent massive operational inefficiencies and lost revenue. In the high-stakes world of industrial automation, reliability isn’t a luxury – it’s the foundation of success. At the heart of countless machines, working tirelessly and often unseen, lies the Turck inductive sensor, a technological cornerstone ensuring seamless operation and precision where it matters most.
Understanding the Core: What are Inductive Sensors?
Turck inductive sensors belong to the category of non-contact proximity switches. Unlike mechanical limit switches requiring physical contact, they operate on a fundamental principle: electromagnetic induction. When energized, the sensor generates an oscillating electromagnetic field around its active face. When a metallic target enters this field – be it steel, aluminum, copper, brass, or other electrically conductive materials – it disturbs the field, inducing tiny electrical currents called eddy currents within the target.
Turck’s proprietary designs excel at reliably detecting this disturbance. Internal circuitry continuously monitors the state of the oscillator. The induced eddy currents cause a measurable energy loss or dampening effect within the sensor’s coil. Sophisticated electronics detect this change in oscillation amplitude or frequency and trigger a clean, digital output signal (like switching a relay or transistor). This entire process happens without physical contact, making them incredibly durable and virtually immune to wear and tear. Whether detecting a piston position in a hydraulic cylinder, a metal pallet on a conveyor, or verifying the presence of a component on an assembly line, this contactless detection is revolutionary.
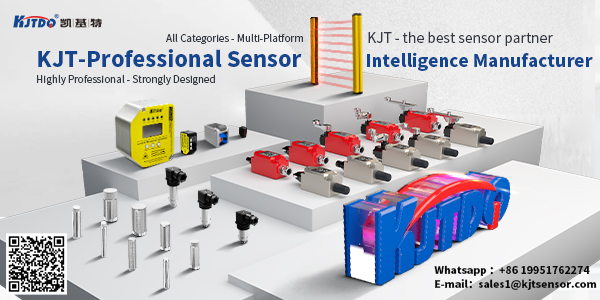
Why Turck Inductive Sensors Are the Industry Standard: Key Advantages
Turck has built a formidable reputation in industrial sensing for good reason. Their inductive sensors deliver tangible advantages that directly translate to operational benefits:
- Unparalleled Robustness: Engineered for demanding industrial environments, Turck sensors boast exceptional resistance to shock, vibration, dirt, oil, and coolant splashes. Many models achieve robust IP67, IP68, or IP69K ratings, protecting against dust ingress and high-pressure washdowns. This intrinsic durability minimizes unexpected failures and extends operational life.
- Exceptional Reliability & Precision: Consistent detection is paramount. Turck sensors offer highly reliable switching behavior with minimal hysteresis. Their designs ensure accurate detection distances (e.g., detecting steel targets at ranges up to 20mm or more, depending on model) are maintained consistently, even under challenging conditions like varying ambient temperatures or target speeds. This precision ensures processes run smoothly without false triggers or missed detections.
- High Switching Frequencies: Modern automation demands speed. Turck inductive sensors offer fast response times and high switching frequencies (up to 3000 Hz or more). This capability allows them to reliably detect individual components moving rapidly on high-speed assembly lines or packaging machinery where milliseconds count. No contact means no bouncing or sticking at high speeds.
- Reduced Maintenance & Costs: The absence of physical contact and moving parts makes these sensors remarkably low maintenance. They don’t wear out from repeated actuation. This translates directly to lower Total Cost of Ownership (TCO) through reduced spare part inventories, minimized maintenance downtime, and fewer disruptions to production schedules.
- Versatility in Design: Turck offers an extensive portfolio to fit virtually any application. Choose from diverse form factors: M8, M12, M18, M30 barrel sensors, rectangular block designs, specialized high-temperature variants, factor-1 (minimal space) options, analog sensors for distance measurement, and advanced sensors with IO-Link connectivity for Industry 4.0 integration. This breadth ensures the right sensor is available for the specific mounting constraints and functional needs.
Turck Sensors in Action: Real-World Applications
The versatility and robustness of Turck inductive sensors make them ubiquitous across countless industries:
- Automotive Manufacturing: From robot welding cells detecting arm position and fixture clamps securing parts, to confirming gear presence in transmissions and monitoring paint shop conveyors. Their resilience to sparks, weld spatter, and harsh chemicals is critical.
- Material Handling & Logistics: Ensuring pallet positioning on conveyors, verifying carton height at sorting gates, detecting forks on forklifts, and confirming container presence automatically. Reliable detection keeps warehouses flowing efficiently.
- Packaging Machinery: Counting cans/bottles on filling lines, verifying cap placement, detecting metal components in processing units, and controling servo-driven packaging operations at high speeds.
- Food & Beverage Processing: Hygienic stainless-steel variants withstand rigorous CIP (Clean-in-Place) washdowns while reliably detecting tanks, valves, mixers, and labeling components. IP69K rating is essential here.
- Metalworking & Machinery: Monitoring lathe chuck positions, verifying tool presence in spindles, controlling cylinder strokes, and safeguarding presses. Their ability to function reliably amidst metal chips and coolants is unmatched.
- Intralogistics & Robotics: Providing critical position feedback for autonomous guided vehicles (AGVs), ensuring robotic arms accurately pick and place metal objects, and verifying pallet engagement.
Beyond Basic Detection: The Turck Difference
Turck doesn’t just offer sensors; they provide sophisticated solutions. Many Turck inductive sensors integrate IO-Link communication technology, transforming them into intelligent data points on the factory network. IO-Link enables:
- Remote configuration and parameter setting.
- Real-time monitoring of sensor diagnostics and health data.
- Enhanced diagnostics for predictive maintenance.
- Simplified wiring using standard unshielded cables.
This intelligence significantly enhances process transparency and uptime. Furthermore, Turck’s commitment to quality is evident in stringent manufacturing processes and comprehensive global support, providing engineers and maintenance teams with the confidence they need.
From ensuring pinpoint accuracy in a delicate robotic assembly task to enduring the punishing environment of a steel mill foundry, Turck inductive sensors operate as the vigilant, unseen guardians of industrial processes. Their blend of ruggedness, precision, and reliability sets the benchmark for non-contact object detection. By eliminating mechanical wear and offering consistent performance even in the harshest conditions, they are not merely components; they are strategic investments in operational stability, minimizing costly downtime and maximizing productivity. When the seamless flow of automated operations relies on detecting metal, the Turck inductive sensor consistently proves itself as the trusted standard, silently enabling the future of efficient manufacturing.