ifm laser level sensor
- time:2025-03-08 03:55:51
- Нажмите:0
IFM Laser Level Sensors: Revolutionizing Precision Measurement in Industrial Automation
In an era where industrial efficiency and accuracy are non-negotiable, laser level sensors have emerged as game-changers for industries ranging from water treatment to chemical processing. Among these cutting-edge devices, IFM laser level sensors stand out for their reliability, precision, and adaptability. Whether you’re managing liquid storage tanks, monitoring bulk solids, or ensuring safe material handling, understanding how these sensors work—and why IFM’s technology leads the pack—can transform your operational workflows.
The Science Behind Laser Level Sensing
At its core, a лазерный датчик уровня жидкости operates by emitting a focused laser beam toward a target surface. The device then measures the time it takes for the reflected light to return, calculating the distance to the object with remarkable accuracy. IFM’s laser sensors leverage advanced time-of-flight (ToF) or phase-shift measurement principles, enabling sub-millimeter precision even in challenging environments.
What sets IFM apart is its integration of self-cleaning optics and adaptive signal processing. These features minimize interference from dust, steam, or fluctuating ambient light—common pain points in industrial settings. For instance, in a wastewater treatment plant, where foam and debris often obscure measurements, IFM sensors deliver consistent data without manual intervention.
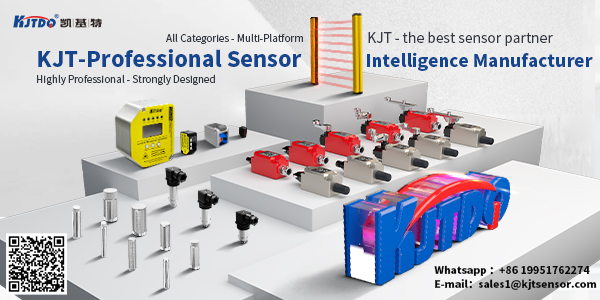
Key Advantages of IFM Laser Level Sensors
- Non-Contact Measurement
Unlike float switches or capacitive probes, laser sensors don’t physically touch the medium. This eliminates wear and tear, reduces maintenance costs, and ensures longevity—a critical factor for industries like food and beverage, where hygiene standards are stringent.
- High Accuracy Across Distances
IFM’s devices excel in both short- and long-range applications. For example, the LFP/LFP Inox series offers measurements from 0.1 meters up to 30 meters, making it ideal for silo monitoring or large-scale storage tanks.
- Versatility in Harsh Conditions
With IP67/IP69K ratings and stainless steel housings, these sensors thrive in extreme temperatures, corrosive environments, or high-pressure zones. A chemical plant using IFM sensors, for instance, can reliably track aggressive liquids without sensor degradation.
- Easy Integration with IoT Systems
IFM prioritizes Industry 4.0 compatibility. Many models feature IO-Link connectivity, enabling real-time data transmission to PLCs or cloud platforms. This seamless integration supports predictive maintenance and process optimization.
Applications That Showcase IFM’s Expertise
- Water and Wastewater Management: Detecting water levels in clarifiers or pump stations with millimeter precision, even in turbulent flows.
- Bulk Solid Monitoring: Accurately measuring grains, powders, or pellets in silos, reducing overfill risks and material waste.
- Pharmaceutical Production: Ensuring sterile, non-invasive level control for sensitive liquid or granular ingredients.
- Renewable Energy: Monitoring coolant levels in solar thermal systems or biomass storage with fail-safe reliability.
A case study from a European cement plant highlights IFM’s impact: After replacing mechanical sensors with IFM’s LR5600 laser sensors, the plant reduced downtime by 40% and achieved 99.8% measurement accuracy—even in dusty kiln feed areas.
Why Choose IFM Over Competing Brands?
While compes offer similar technologies, IFM’s laser level sensors distinguish themselves through:
- Customizable Outputs: Analog, digital, or relay options tailored to specific machinery.
- Intuitive Setup: User-friendly interfaces like the EFCNR260 configuration tool simplify calibration.
- Global Support: IFM’s 24⁄7 technical assistance ensures minimal disruption during installation or troubleshooting.
Будущие тенденции и инновации
The demand for laser-based sensing is surging as industries prioritize automation and sustainability. IFM is already pioneering AI-driven predictive analytics within its sensor ecosystems. Imagine a sensor that not only detects tank levels but also predicts leaks based on historical data—preventing spills before they occur.
Additionally, advancements in miniaturized laser diodes are paving the way for compact, energy-efficient sensors. IFM’s R&D teams are actively exploring these innovations, ensuring their products remain at the forefront of industrial technology.
Best Practices for Maximizing Sensor Performance
To get the most from your IFM laser level sensor:
- Regularly clean the lens using compressed air (avoid abrasive materials).
- Align the sensor perpendicular to the target surface to avoid signal deflection.
- Use mounting brackets to minimize vibrations in high-machinery zones.
- Update firmware periodically to access new features and performance enhancements.
By adhering to these guidelines, operators can extend sensor lifespan and maintain peak accuracy—turning a “smart investment” into a long-term competitive advantage.
From optimizing resource management to enabling smarter automation, IFM laser level sensors are redefining what’s possible in industrial measurement. As technology evolves, one thing remains clear: precision isn’t just a goal—it’s a necessity.