cnc proximity sensor
- time:2025-01-22 02:55:28
- Нажмите:0
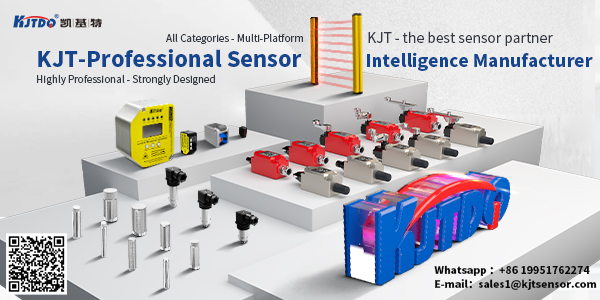
Title: “Maximizing Efficiency with CNC Proximity Sensors: A Comprehensive Guide”
Introduction
In the realm of precision manufacturing, the significance of CNC (Computer Numerical Control) proximity sensors cannot be overstated. These advanced devices play a pivotal role in ensuring accuracy and efficiency within CNC machines, which are integral to modern production lines across various industries. This article delves into the world of CNC proximity sensors, exploring their functionalities, benefits, and how they contribute to streamlining operations and enhancing productivity.
Understanding CNC Proximity Sensors
CNC proximity sensors, also known as proximity effect sensors or electronic proximity sensors, are sophisticated instruments designed to detect the presence or absence of an object without physical contact. They operate based on principles such as capacitive, inductive, or magnetic fields, allowing them to sense metallic and non-metallic objects alike. In the context of CNC machining, these sensors serve as critical components for position feedback, tool detection, and collision avoidance, ensuring seamless and precise control over the manufacturing process.
The Advantages of Incorporating CNC Proximity Sensors
- Повышение точности: By providing real-time feedback on tool positions and part dimensions, CNC proximity sensors enable micron-level accuracy, reducing errors and waste. This level of precision is particularly crucial in industries like aerospace, automotive, and medical device manufacturing, where tight tolerances are mandatory.
- Increased Production Speed: With rapid response times and the ability to monitor multiple points simultaneously, proximity sensors facilitate faster cycle times and reduced downtime for tool changes or adjustments. This translates into higher throughput and cost-effectiveness for manufacturers.
- Improved Safety and Tool Lifespan: By detecting potential collisions or misalignments early on, CNC proximity sensors prevent damage to tools, workpieces, and machinery, thereby extending their lifespan and minimizing maintenance needs. They also contribute to a safer working environment for operators.
- Многофункциональность и адаптивность: Modern CNC proximity sensors are compatible with a wide range of materials and can withstand harsh industrial environments, including high temperatures, humidity, and vibrations. This versatility allows them to be integrated into diverse CNC applications, from milling and turning to grinding and punching.
Applications in CNC Machining
CNC proximity sensors find applications in various stages of the machining process, including:
- Tool Length Measurement: Ensuring accurate tool changes and compensation for wear.
- Workpiece Positioning: Verifying correct placement before machining begins.
- Collision Avoidance: Monitoring for unexpected contact between the tool and the workpiece or machine bed.
- Quality Control: Measuring finished product dimensions to ensure adherence to specifications.
Conclusion
Integrating CNC proximity sensors into your manufacturing workflow offers a multitude of advantages, from heightened precision and speed to enhanced safety and adaptability. As technology continues to advance, these sensors are poised to become even more integral to the future of smart manufacturing, empowering businesses to stay competitive in an ever-evolving industrial landscape. By understanding their capabilities and implementing them strategically, manufacturers can unlock new levels of efficiency and productivity in their CNC operations.