vibration proximitor proximity sensor
- time:2024-12-19 02:56:49
- Нажмите:0
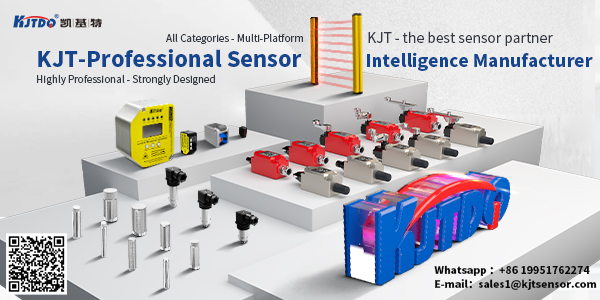
Vibration Proximitor: Understanding the Power of Proximity Sensors
In today’s technologically advanced landscape, sensors play a critical role in various industries. Among these, vibration proximity sensors, also known as viproxi or vibro-acoustic sensors, have emerged as essential tools for predictive maintenance and structural monitoring. This article delves into the fundamentals, applications, and benefits of vibration proximity sensors to provide a comprehensive understanding of their significance in modern technology.
What Are Vibration Proximitors?
Vibration proximity sensors are specialized devices designed to detect and measure the distance to a target object by analyzing vibrations or acoustic waves. They operate based on the principle of vibro-acoustics, where mechanical vibrations produce sound waves that travel through a medium such as air, water, or solid materials. These sensors are particularly adept at identifying and quantifying the minute changes in these vibrations, allowing for precise measurement of proximity.
**How Do Vibration Proximitors Work?
The working mechanism of a vibration proximity sensor involves generating a specific frequency of vibrations or acoustic waves and then measuring the time it takes for these waves to travel to the target and back. The sensor analyzes the reflected waves to calculate the distance. This non-contact method ensures high accuracy and reliability, making these sensors indispensable in applications requiring precise distance measurements without physical contact.
Applications of Vibration Proximitors
- Predictive Maintenance in Industrial Machinery: One of the most prevalent applications of vibration proximity sensors is in predictive maintenance. By continuously monitoring the proximity and vibration patterns of machinery components, these sensors can predict potential failures before they occur. This proactive approach helps reduce downtime and maintenance costs while extending the lifespan of equipment.
- Structural Health Monitoring: In civil engineering and architecture, vibration proximity sensors are used to monitor the structural health of buildings, bridges, and other infrastructure. By detecting early signs of wear and tear or damage, these sensors enable timely interventions, ensuring safety and longevity of structures.
- Автомобильная промышленность: In vehicles, these sensors are employed for various purposes, including monitoring the clearance between parts to prevent collisions, detecting the proximity of obstacles for advanced driver assistance systems (ADAS), and ensuring proper alignment during manufacturing processes.
Advantages of Vibration Proximitors
- Non-Contact Measurement: Unlike traditional contact-based sensors, vibration proximity sensors do not require physical contact with the target object, reducing wear and tear and minimizing the risk of interference with the monitored system.
- High Precision: These sensors offer exceptional accuracy in distance measurement, often within micrometers, providing detailed and reliable data for critical applications.
- Многогранность: Vibration proximity sensors can be used in a wide range of environments and applications, from harsh industrial settings to delicate electronic components, due to their non-invasive nature and robust design.
- Real-Time Monitoring: With the ability to continuously monitor vibrations and proximity, these sensors provide real-time data, enabling instant feedback and quick decision-making.
Выводы
Vibration proximity sensors represent a significant advancement in sensor technology, offering high precision, reliability, and versatility. Whether it’s in predictive maintenance, structural health monitoring, or the automotive industry, these sensors prove to be indispensable in ensuring efficiency, safety, and longevity. As technology continues to evolve, the adoption and integration of vibration proximity sensors across various sectors will undoubtedly grow, paving the way for more intelligent and responsive systems.