Тип фотоэлектрического датчика
- time:2025-07-28 09:28:16
- Нажмите:0
Photoelectric Sensor Types: Illuminating Detection Solutions for Automation
Light: The Invisible Workhorse of Modern Automation. Its properties form the basis of some of the most reliable and versatile sensors used across countless industries. Photoelectric sensors, operating on the fundamental principles of light emission and reception, are the unsung heroes ensuring smooth production lines, efficient packaging, precise object counting, and robust safety systems. Understanding the different types of photoelectric sensors is crucial for selecting the optimal solution for any application.
How Do Photoelectric Sensors Work?
At their core, all photoelectric sensors consist of two primary components: an Emitter (light source) and a Receiver (light detector). The sensor detects the presence, absence, or distance of an object by analyzing how emitted light interacts with the target. This interaction can be the interruption of a light beam, the reflection of light off a surface, or a change in the intensity of reflected light. The specific mechanism defines the sensor type.
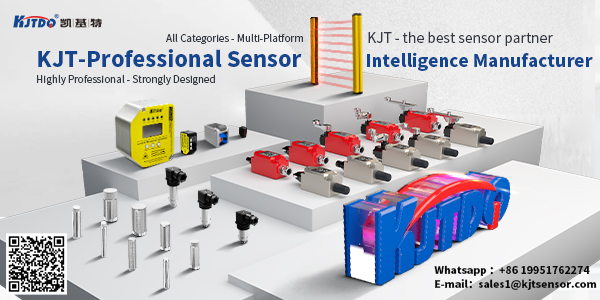
Exploring the Primary Photoelectric Sensor Types
- Through-Beam Sensors (Opposed Mode)
- Mechanism: Considered the most robust and capable of the longest sensing ranges. The emitter and receiver are housed in separate units, positioned directly opposite each other. The emitter projects a continuous beam of light (often infrared, laser, or visible red) towards the receiver. Detection occurs when an object physically interrupts this beam, blocking light from reaching the receiver.
- Key Advantages: Highest reliability and immunity to environmental factors (dust, target color/surface). Longest sensing ranges – often many meters.
- Key Limitations: Requires precise alignment of two separate units. Installation complexity can be higher, especially over longer distances. Requires wiring for both components.
- Ideal Applications: Detecting large objects, checking for tears in webs/materials, high-speed counting, safety light curtains (a specialized form), applications requiring maximum range or reliability in challenging environments.
- Retroreflective Sensors (Reflex Mode)
- Mechanism: The emitter and receiver are housed within a single unit. A specialized retroreflector (corner-cube reflector) is mounted opposite the sensor. The emitter projects light towards the reflector, which sends the light beam directly back to the receiver housed in the same sensor body. Detection occurs when an object interrupts the beam, preventing the reflected light from returning to the receiver.
- Key Advantages: Simpler installation than through-beam (only one unit to wire; reflector is passive). Good sensing ranges, typically longer than diffuse sensors but less than through-beam. More tolerant of minor misalignment than through-beam.
- Key Limitations: The target must be opaque enough to block the beam. Performance can be affected by highly reflective or shiny targets passing near the beam path, potentially bouncing light back to the receiver and causing false triggers. Requires mounting a reflector.
- Ideal Applications: Conveyor object detection, presence checking at entry/exit points, pallet detection, applications where running cables for a separated emitter/receiver unit is impractical.
- Diffuse Reflective Sensors (Proximity Mode)
- Mechanism: Like retroreflective sensors, the emitter and receiver are integrated into a single housing. However, no external reflector is used. Instead, detection relies on light emitted from the sensor reflecting directly off the target object itself and bouncing back to the receiver. The sensor triggers when enough reflected light intensity is detected.
- Key Advantages: Simplest installation – only one unit needs mounting and wiring. No reflector required. Suitable for detecting objects where mounting reflectors isn’t feasible.
- Key Limitations: Sensing range is inherently shorter than through-beam or retroreflective types. Performance is highly dependent on the target’s color, surface texture, reflectivity, and size. Dark, matte, or very small objects may reflect insufficient light. Background objects can potentially cause false triggers. Sensitivity adjustments (gain) are often critical.
- Ideal Applications: Detecting objects at close range, presence detection of non-shiny objects on conveyors, label detection, bottle cap detection, applications requiring simple setup and no reflector.
Advanced Diffuse Sensor Variants:
- Background Suppression (BGS) / Fixed Field (Fixed Focus): These sensors use optical triangulation. The emitter sends out light converging at a specific distance. The receiver looks for light reflected only from this focused spot. Objects beyond the focal point reflect light hitting the receiver at a different angle, which is ignored. Crucial for reliably detecting targets close to a reflective background.
- Foreground Suppression (FGS): Less common, designed to ignore objects closer than a set distance and only detect objects beyond that point. Useful in specific material handling scenarios.
- Polarized Retroreflective: Incorporate optical filters. The emitter’s light is polarized in a specific orientation. The retroreflector is designed to twist (depolarize) the light before reflecting it back. The receiver has a filter matching the emitter’s polarity. Highly effective at rejecting false triggers from shiny objects (like metal cans) since their direct reflections retain the original polarization and are blocked by the receiver filter.
Selecting the Right Sensor Type: Key Considerations
Choosing the optimal photoelectric sensor type demands careful analysis of your specific application:
- Required Sensing Distance: Through-beam > Retroreflective > Standard Diffuse.
- Target Characteristics: Size, shape, color, surface texture (shiny, matte, transparent).
- Environmental Conditions: Dust, moisture, fog, ambient light levels.
- Presence of Background/Foreground Objects: Necessitates BGS, FGS, or careful diffuse sensor placement.
- Installation Constraints: Space for separate emitter/receiver units? Ability to mount a reflector? Ease of access for alignment?
- Cost Considerations: Typically, standard diffuse sensors are the least expensive, followed by retroreflective, then through-beam (due to needing two components). Advanced features like BGS or polarization add cost.
Выводы
From the robust and long-range through-beam sensors to the conveniently integrated retroreflective and diffuse types (including specialized background suppression variants), photoelectric sensor technology offers a solution for nearly any object detection challenge in industrial automation, packaging, material handling, and beyond. Understanding these core types and their unique operating principles, advantages, and limitations is the essential first step toward implementing reliable, efficient, and cost-effective sensing solutions that keep processes running smoothly and intelligently. The right photoelectric sensor becomes the eyes of the machine, powered by light.