photoelectric encoder
- time:2025-07-24 01:52:21
- Нажмите:0
The Silent Sentinel: How Photoelectric Encoders Power Precision in Our Automated World
Imagine a high-speed robotic arm assembling a smartphone with micron-level accuracy, or a CNC machine carving intricate aerospace components. The flawless motion seems almost intuitive. But beneath the surface, a critical sensory system is constantly at work, translating movement into a language machines understand. This crucial interpreter is the photoelectric encoder, the unsung hero enabling precision in countless modern applications.
What Exactly is a Photoelectric Encoder?
At its core, a photoelectric encoder, often termed an optical encoder, is a sophisticated electro-mechanical device designed to convert mechanical motion – typically angular rotation or linear displacement – into precise electrical signals. It achieves this remarkable feat using the fundamental principles of light and optics. Think of it as the machine’s sense of touch and proprioception combined, providing real-time feedback on position, speed, direction, and even acceleration.
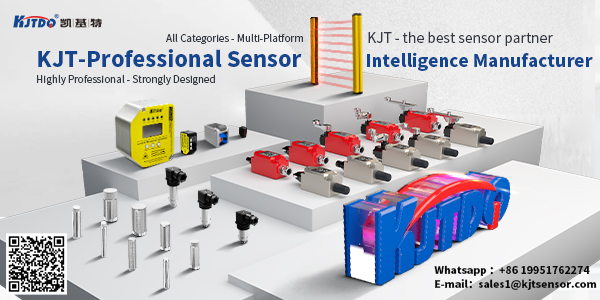
Illuminating the Working Principle: Light Becomes Data
The fundamental operation relies on interrupting or modulating a beam of light. Here’s a breakdown of the typical components and process:
- Light Source: An LED (Light Emitting Diode) generates a stable, focused beam of light, usually infrared for reliability and noise immunity. Consistency here is paramount for accurate signal generation.
- Code Disc or Scale: This is the heart of the movement sensing. In a common rotary encoder, it’s a disc attached to the rotating shaft. The disc features precisely etched patterns – alternating transparent and opaque sections (like slots and bars) or intricate coded tracks. For linear encoders, this becomes a stationary or moving scale with similar patterns.
- Photodetectors (Sensors): Positioned strategically opposite the light source (with the disc/scale in between), these light-sensitive components (like photodiodes or phototransistors) detect the incoming light pulses. As the shaft rotates or the scale moves, the pattern interrupts the light beam falling on the photodetectors.
- Signal Conditioning Circuitry: The raw electrical pulses generated by the photodetectors as the light flickers are weak and noisy. This circuitry amplifies, shapes, and often converts these pulses into clean, standardized digital outputs (like square waves) usable by control systems (PLC/Controllers).
Absolute vs. Incremental: Reading the Code
Photoelectric encoders come in two primary flavors, defined by how they report position:
- Incremental Encoders: These are the most common type. They generate a simple, repeating pulse train as the shaft rotates. Each pulse corresponds to a fixed angular increment. Typically, they provide two main outputs (Channel A and B) slightly out of phase (known as quadrature signals). This allows the control system to determine both distance moved (by counting pulses) and direction of rotation (by seeing which channel leads the other). Some include a Z-index or reference pulse (one pulse per revolution) for establishing a home position. They are cost-effective and excellent for measuring speed and relative position.
- Absolute Encoders: These provide unique position information for every single point within their range, even immediately upon power-up. This is achieved through a complex multi-track pattern on the disc (like a unique binary or Gray code) read simultaneously by multiple photodetectors. A 12-bit absolute encoder, for example, can distinguish 4096 (2^12) unique positions per revolution. Absolute encoders are essential where knowing the exact position without movement or after a power loss is critical, such as in robotics, antenna positioning, or critical industrial valves.
Where Precision Matters: Ubiquitous Applications
The unique combination of non-contact sensing, high resolution, speed, and reliability makes photoelectric encoders indispensable across diverse sectors:
- Industrial Automation & Robotics: Found in servo motors driving robotic joints, conveyors, pick-and-place machines, and packaging lines, providing the essential position feedback for closed-loop control.
- Computer Numerical Control (CNC) Machinery: Ensuring accurate movement of spindles, cutting tools, and worktables in milling machines, lathes, and grinders. Achieving tight tolerances is impossible without high-resolution encoders.
- Motion Control Systems: Driving precision stages in semiconductor manufacturing, microscopy, laser processing, and 3D printing. They enable sub-micron resolutions in advanced setups.
- Medical Devices: Used in imaging equipment (CT/MRI scanners), surgical robots, infusion pumps, and diagnostic instruments where smooth, precise motion is vital.
- Printing & Packaging: Synchronizing rollers for registration control, ensuring colors and cuts align perfectly every time.
- Aviation & Aerospace: Monitoring flap positions, throttle controls, and antenna pointing mechanisms.
Why Choose Photoelectric Technology? The Compelling Advantages
While alternatives like magnetic or capacitive encoders exist, photoelectric encoders offer distinct benefits driving their widespread adoption:
- High Resolution and Accuracy: Optical systems can achieve extremely fine resolutions (thousands of pulses per revolution - PPR - or more for high-end units) and superior accuracy due to the precision achievable in patterning the disc/scale. This is crucial for demanding applications.
- High Speed Response: Photodetectors react extremely quickly to changes in light, enabling the measurement of very high rotational speeds or rapid linear movements.
- Non-Contact Operation: The sensing mechanism relies purely on light, meaning there is no physical wear between the disc/scale and sensors. This translates directly to exceptional longevity and maintenance-free operation in clean environments.
- Low Starting Torque: Since only the lightweight disc needs to rotate, they impose minimal drag on the shaft. This is critical for low-power systems.
- Immunity to Magnetic Fields: Unlike magnetic encoders, optical versions operate unaffected by external magnetic influences. Robustness in electrically noisy environments is a significant advantage.
The Unseen Engine of Precision
From the robots building our cars to the printers creating intricate packaging, photoelectric encoders operate silently and relentlessly in the background. They transform physical motion into the precise digital signals that modern control systems depend on. By mastering the interplay of light and precise patterning, these ingenious devices are fundamental to the high accuracy, speed, and repeatability that define advanced automation and technology today. Choosing the right optical encoder – whether incremental for relative tracking or absolute for definitive position knowledge – is a cornerstone decision in designing systems where motion precision is paramount. Their role as the silent sentinel of position feedback remains utterly indispensable in our increasingly automated world.