высокотемпературный фотодатчик
- time:2025-07-25 03:34:27
- Нажмите:0
Thermal Warriors: How High Temperature Photoelectric Sensors Conquer the Heat
Modern industry thrives on pushing boundaries, often operating in environments where temperatures soar beyond what conventional electronics can endure. Monitoring, controlling, and ensuring safety in these extreme conditions demands specialized sensing technology. Enter the high temperature photoelectric sensor – a resilient category engineered to deliver reliable object detection, level control, distance measurement, and more, even amidst intense thermal challenges. This article explores the unique capabilities, critical design considerations, and vital applications of these robust sensing solutions.
Understanding the Core Principle and the Heat Challenge
At its heart, a photoelectric sensor functions by projecting a light beam (visible, laser, or infrared) towards a target. A receiver then detects either:
- The reflected light beam (in diffuse or retro-reflective models).
- The interruption of a beam traveling to a separate reflector (in through-beam models).
The presence or absence of the light signal at the receiver triggers the sensor’s output, indicating object detection. This non-contact method offers significant advantages, including wear-free operation, fast response times, and the ability to detect diverse materials.
However, conventional photoelectric sensors falter when ambient temperatures climb significantly above room temperature. Standard electronic components, plastic housings, and optical elements degrade, melt, or malfunction. Signal drift, reduced sensing range, permanent damage, or complete failure become likely outcomes. This limitation renders them unsuitable for critical processes in foundries, metal processing, glass manufacturing, power generation, and numerous other high-heat applications.
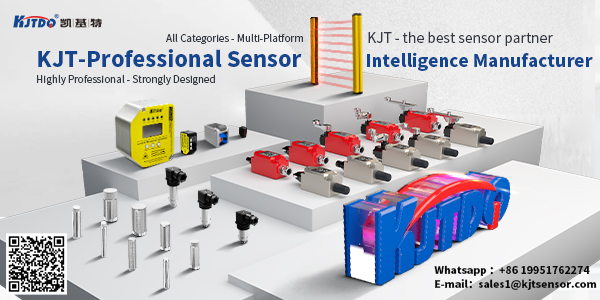
Engineering Resilience: How High Temp Sensors Tame the Heat
High temperature photoelectric sensors overcome these barriers through deliberate, robust engineering. Key design strategies include:
- Specialized Materials: Moving away from standard plastics, these sensors utilize housings and optical components crafted from heat-resistant metals (like stainless steel alloys) and advanced ceramics. These materials withstand thermal expansion, resist chemical corrosion common in hot environments, and maintain structural integrity.
- High-Temp Electronics: Internal circuitry employs components rated for extended temperature ranges, often utilizing specialized semiconductors and passive elements. Efficient thermal management designs, sometimes incorporating heat sinks or thermal barriers within the housing, help isolate sensitive electronics from external heat sources.
- Enhanced Optical Design: Lenses and optical windows are typically made from sapphire, quartz, or specialized high-temperature glass. These materials maintain high optical clarity and resistance to thermal shock and chemical attack. Optical filtering is often employed to minimize interference from hot glowing objects (blackbody radiation) that could swamp the sensor’s receiver.
- Active Cooling Systems (For Extreme Cases): In the most severe applications (e.g., near furnaces or molten metal), sensors may integrate thermoelectric (Peltier) coolers or compressed air purge/cooling systems. These actively maintain the internal electronics and optics within their functional temperature window, significantly extending the sensor’s operational envelope.
- Ruggedized Construction: Beyond heat, these environments often involve vibration, dust, moisture, and aggressive chemicals. Sealed enclosures (IP67, IP69K ratings) and robust mechanical construction are standard features for high temperature photoelectric sensors.
Where the Heat Doesn’t Quit: Vital Applications
The unique resilience of high temperature photoelectric sensors makes them indispensable in sectors where heat is inherent to the process:
- Metals Industry: Monitoring billet presence in hot rolling mills, detecting slabs in reheat furnaces, controlling ladle positioning near molten metal, verifying casting mold closures, and managing ingot handling in forges.
- Glass Manufacturing: Detecting glass bottles or containers on annealing lehr conveyors (where temperatures gradually decrease but start high), monitoring glass levels in forehearths, verifying gob presence in forming machines.
- Ceramics & Cement Production: Monitoring kiln car positions within high-temperature tunnel kilns, detecting brick stacking heights before firing, level control in preheater towers.
- Power Generation: Ash level monitoring in boilers and hoppers, turbine blade monitoring, fuel handling systems within power plants.
- Chemical & Petrochemical: Level detection in hot chemical storage tanks, monitoring catalyst movement in high-temperature reactors, presence detection on heated conveyor lines.
- Automotive & Aerospace Manufacturing: Paint shop processes (high-temperature curing ovens), detecting parts in heat treatment furnaces, composite curing applications.
- Waste Incineration & Recycling: Monitoring material flow on gratings within incinerators, detecting objects on sorting lines subjected to radiant heat.
Key Advantages Driving Adoption
Beyond their core ability to survive the heat, high temperature photoelectric sensors offer compelling benefits:
- Non-Contact Operation: Eliminates wear and tear on both the sensor and the target object, crucial for delicate or hot surfaces.
- High Speed & Precision: Capable of detecting small objects or rapid movements on fast production lines, unaffected by thermal inertia.
- Многогранность: Available in various configurations (through-beam, retro-reflective, diffuse) and light sources (visible, laser, infrared) for diverse detection needs.
- Improved Process Reliability & Safety: Continuous, reliable monitoring prevents costly downtime, ensures equipment operates correctly (e.g., preventing overfills), and enhances worker safety by automating hazardous zone tasks.
- Reduced Maintenance Costs: Durable construction and non-contact operation significantly lower the total cost of ownership compared to mechanical switches needing frequent replacement in harsh conditions.
Selecting the Right Sensor for the Hot Zone
Choosing the optimal high temperature photoelectric sensor demands careful consideration:
- Ambient Temperature Range: Be precise about the continuous operational temperature the sensor body will experience, not just the target temperature. Exceeding this range is the primary failure risk.
- Target Characteristics: Material, size, color, surface finish, and temperature all influence reflectivity and detection reliability. Consider using high-power models or specific wavelengths (e.g., infrared for hot, dark objects).
- Required Sensing Distance: Account for thermal haze and potential beam distortion in hot environments; longer sensing ranges typically require more powerful emitters or specific optical setups. Through-beam models generally offer the longest, most reliable range in tough conditions.
- Environmental Hazards: Besides heat, assess exposure to dust, water, steam, chemicals, or vibration. Match the sensor’s IP rating and construction materials accordingly.
- Required Output & Connectivity: Ensure compatibility with existing PLCs or control systems (e.g., PNP/NPN, analog, IO-Link).
As manufacturing and energy sectors continue to operate at higher intensities and temperatures, the demand for robust sensing technology escalates. High temperature photoelectric sensors stand as engineered solutions, overcoming the formidable barrier of intense heat to deliver the essential non-contact detection capabilities underpinning efficiency, safety, and reliability where conventional sensors simply cannot survive. Their specialized design transforms them from vulnerable components into thermal warriors, safeguarding processes deep within the industrial heat zone.