photoelectric rotary encoder
- time:2025-07-25 03:13:59
- Нажмите:0
Photoelectric Rotary Encoders: The Precision Engine Behind Modern Automation
Imagine a sophisticated robotic arm assembling microchips, a CNC machine crafting complex aerospace components, or a high-speed printing press synchronizing rolls perfectly. What invisible force enables such incredible precision and coordination? Often, it’s the unsung hero embedded within: the photoelectric rotary encoder. This ingenious device translates the fundamental physical movement – rotation – into a highly accurate, reliable digital language that control systems understand. In an era demanding micron-level accuracy and split-second timing, photoelectric encoders are indispensable, providing the critical feedback that keeps modern automation running smoothly and efficiently.
How Does the “Photo-Electric” Magic Work?
At its core, a photoelectric rotary encoder is a non-contact position sensor harnessing the principles of light and electronics. Its operation is elegant in its simplicity yet profound in its impact:
- The Light Source: An LED emits a focused beam of light.
- The Code Disc (or Slotted Disk): This is a precisely manufactured disk attached to the rotating shaft. It features alternating transparent and opaque segments arranged in a specific pattern (like radial lines).
- The Photodetector Array: Positioned opposite the light source, behind the code disc, sits one or more light-sensitive sensors (photodiodes or phototransistors).
- The Electronics: Circuitry processes the signals from the photodetectors.
As the shaft rotates, the code disc spins. The alternating segments either allow light to pass through to the detector or block it. This rapid switching creates a pulsed light signal at the photodetector. The onboard circuitry converts this optical signal into discrete electrical pulses or digital codes. By counting these pulses or interpreting the code pattern, the system precisely determines the shaft’s angular position, speed (RPM), and direction of rotation.
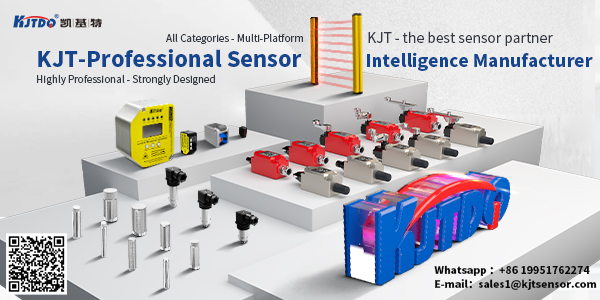
Why “Photoelectric” Reigns Supreme: Key Advantages
While other encoder technologies exist (like magnetic or capacitive), photoelectric encoders dominate applications demanding high precision due to several compelling advantages:
- Exceptional Resolution and Accuracy: The ability to manufacture extremely fine patterns on the code disc allows photoelectric encoders to achieve incredibly high resolution – meaning they can detect minute angular movements. This translates to superior position sensing accuracy, often down to fractions of an arc-second.
- High Speed Response: Light travels fast! This enables photoelectric encoders to operate at very high rotational speeds without losing signal integrity. They excel in capturing rapid motion.
- Non-Contact Sensing: The lack of physical wear between the light source, disc, and detectors (aside from bearings) results in long operational life and minimal maintenance compared to contacting technologies. Надежность is a major strength.
- Low Starting Torque: Since sensing is non-contact, there’s virtually no drag on the rotating shaft, making them ideal for low-power applications.
- Immunity to Magnetic Fields: Unlike magnetic encoders, photoelectric versions are unaffected by stray electromagnetic interference (EMI), enhancing stability in electrically noisy industrial environments.
Resolving the Position: Incremental vs. Absolute
Photoelectric encoders fall into two main categories defined by how they report position:
- Incremental Encoders: These generate a continuous stream of pulses as the shaft rotates. They have two primary output channels (typically called Channel A and Channel B) producing square waves offset by 90 degrees. This phase quadrature allows determination of both position change (by counting pulses) and direction (by which channel leads the other). They usually also include a reference pulse (Index or Z-pulse) output once per revolution for homing. Incremental encoders are simpler and often more cost-effective but only track relative movement from a start point. Power loss means position is lost.
- Absolute Encoders: These provide a unique digital code (binary, Gray code) for every single shaft position within one revolution or multiple revolutions (multi-turn absolute). This code represents the absolute angular position. Even after a power cycle, the encoder instantly knows its exact position without needing a reference run. Absolute encoders are essential for applications where knowing the exact position upon startup is critical, preventing potentially dangerous “homing” moves or costly recalibration.
Where Precision Matters: Ubiquitous Applications
The unique combination of high resolution, speed, and reliability makes photoelectric rotary encoders vital across countless industries:
- Industrial Automation & Robotics: Providing precise joint position and speed feedback in robotic arms, controlling servo motors in CNC machines, coordinating conveyors, and automating assembly lines.
- Motion Control: Found in servo motors, stepper motors, and actuators requiring accurate speed regulation and position control.
- Packaging Machinery: Ensuring precise positioning for filling, capping, labeling, and cutting operations at high speeds.
- Printing & Converting: Maintaining registration between printing stations, controlling web tension, and synchronizing rollers.
- Medical Equipment: Used in diagnostic imaging devices (CT, MRI scanners), robotic surgery systems, and infusion pumps requiring high precision and reliability.
- Воздушно - космические и Оборона: In guidance systems, antenna positioning, and flight control surface actuators.
- Semiconductor Manufacturing: Critical for the extreme precision required in wafer handling and lithography equipment.
- Consumer Electronics: Found in high-end cameras (lens focus/zoom) and some computer peripherals.
Beyond the Basics: Key Specifications for Selection
Choosing the right photoelectric rotary encoder involves considering several critical parameters:
- Resolution (PPR/CPR): Pulses Per Revolution or Cycles Per Revolution. Indicates the number of pulses per channel per revolution for incremental encoders. Higher PPR means finer position detection.
- Accuracy: How closely the reported position matches the true mechanical position. Often a small fraction of a degree.
- Interface/Output Type: Common types include quadrature A/B/Z (Open Collector/Line Driver), Sin/Cos (for interpolation to higher resolution), and various digital interfaces (SSI, BiSS-C, EtherCAT, Profinet) for absolute encoders.
- Max. Operating Speed (RPM): The highest rotational speed the encoder can accurately track.
- Environmental Rating (IP Rating): Protection against dust and moisture (e.g., IP64, IP67) is crucial for harsh industrial environments.
- Hollow Shaft vs. Solid Shaft: Hollow shaft models mount directly over a motor shaft, often simplifying installation.
- Bearing Type & Shaft Load: Affects lifespan and suitability for applications with significant radial or axial load.
The Foundation of Modern Control
Photoelectric rotary encoders are more than just components; they are the fundamental sensors that close the loop in countless motion control systems. By providing real-time, high-fidelity feedback on rotational movement, they empower controllers to make instantaneous adjustments, ensuring machines operate with unprecedented precision, speed, and efficiency. From the most delicate medical instruments to massive industrial robots, the subtle interplay of light and electronics within the rotary encoder is quietly enabling the sophistication of the automated world around us. As demands for precision and speed continue to escalate, especially with advancements in automation and robotics, the evolution and application of photoelectric encoder technology will remain at the forefront, driving innovation forward.