фотоэлектрический датчик Фэнса
- time:2025-07-25 01:16:31
- Нажмите:0
The Unseen Power: Understanding How Photoelectric Sensors Work & Transform Automation
Ever had a supermarket door slide open magically as you approached? Or seen a factory assembly line flawlessly count thousands of identical parts? The silent hero behind these everyday (and industrial) marvels is often the Фотоэлектрический датчик. Far more than just a component, understanding its function – or fungsi – unlocks the key to reliable, non-contact detection in countless applications. These sensors are the vigilant eyes of modern automation, employing light to perceive the world around them with remarkable precision.
At its core, the fundamental function of a photoelectric sensor is remarkably straightforward: it uses light to detect the presence, absence, distance, or specific characteristics of an object, all without any physical contact. This non-intrusive nature is a cornerstone of its value. Imagine a machine needing to confirm a bottle is correctly positioned on a filling line. A mechanical sensor might bump the bottle, potentially causing spillage or misalignment. A photoelectric sensor, however, can perform this check silently, cleanly, and instantly using a beam of light.
So, how does this clever detection actually work? It all revolves around a simple trio:
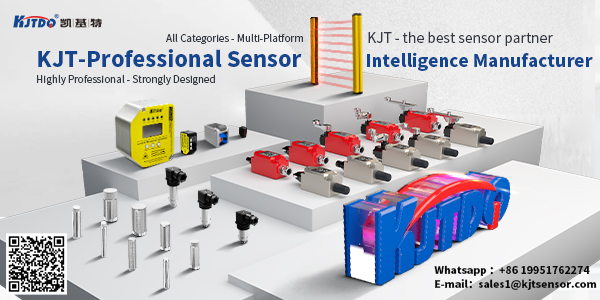
- The Emitter: This component generates a beam of light, typically using an LED (Light Emitting Diode) for visible red, infrared (IR), or laser light. Infrared is especially common in industrial settings due to its resistance to ambient light interference.
- The Target: This is the object the sensor is designed to detect. It interacts with the emitted light beam. Its properties – like reflectivity (for shiny metal), opacity (for cardboard blocking light), or even colour/contrast (for label detection) – determine how it affects the light.
- The Receiver: Positioned strategically relative to the emitter, the receiver “sees” the light beam after its interaction (or lack thereof) with the target. Its job is to convert the incoming light signal into an electrical signal.
The critical function occurs when the receiver assesses the light it receives. Depending on the sensor’s specific mode of operation and its programming (logic), it interprets changes in the light signal:
- Is the light beam present or absent? (e.g., blocked by an opaque object).
- Has the intensity of the reflected light changed? (e.g., a reflective object has moved into position).
- Has the time taken for the light to return changed? (e.g., an object is now closer or farther away).
Based on this analysis, the sensor triggers its output switch. This switch, often a transistor, changes state – turning “ON” (conducting) or “OFF” (not conducting) – to send a clear signal to the connected control system (like a PLC - Programmable Logic Controller). This output signal is the sensor’s primary communication, essentially saying “Target Detected” or “Target Not Detected”. This binary information is the lifeblood feeding automated decision-making processes.
To handle diverse detection challenges, Фотоэлектрический датчик come in several distinct operational types, each with its own strengths:
- Through-Beam (Opposed Mode): Considered the most robust and capable of the longest sensing ranges (sometimes over 100 meters). It consists of separate, opposing units: an emitter and a receiver. The emitter projects a continuous beam directly at the receiver. The core function here is simple: *Object presence = beam blocked.* When an object interrupts the beam, the receiver loses the light signal and triggers the output switch. Ideal for detecting opaque objects of any color or surface finish, even in demanding environments with dust or vibration. Think of high-speed bottle counting on a conveyor.
- Retroreflective (Reflex Mode): Uses a single housing containing both the emitter and receiver, along with a specialized reflector (like a prismatic tape or corner cube reflector) mounted opposite. The emitter sends light towards the reflector, which bounces it directly back to the receiver. The key function is similar to through-beam: *Object presence = reflected beam blocked.* When an object blocks the path between the sensor and reflector, the reflected beam is interrupted, causing the sensor to trigger. Excellent for medium-range detection and often easier to install since wiring is only needed at one point. Common on automated doors and pallet position checks.
- Diffuse (Proximity Mode): Also uses a single housing combining the emitter and receiver. However, it relies on the target object itself to reflect the emitted light back to the receiver. The fundamental function shifts: *Object presence = sufficient reflected light received.* The sensor detects when enough of its own emitted light bounces off the target and returns. Effectiveness depends heavily on the target’s size, color, texture, and distance (generally shorter ranges than through-beam or retro-reflective). Shiny or light-colored objects reflect well; dark or matte objects reflect poorly. Diffuse sensors are versatile for detecting a wide variety of objects without needing a separate reflector, like verifying the presence of a box on a conveyor or a component in a machine fixture. Many modern diffuse sensors incorporate Background Suppression (BGS) technology or Distance-Settable capability, allowing them to focus detection within a specific range and ignore objects beyond it, significantly enhancing reliability.
- Convergent Beam (Fixed Focus Diffuse): A specialized type of diffuse sensor designed for high-precision detection at a specific, fixed distance. Using lenses, it focuses the emitted light to a very small point at its preset sensing range. Its critical function is detecting objects only when they pass through this precise focal point. This makes them ideal for small object detection, verifying component height, or precisely detecting edges or labels on products.
- Colour & Contrast Sensors: Building on diffuse principles, these advanced sensors specifically detect differences in colour or contrast rather than just presence/absence. They are crucial where distinguishing between similar-looking items is essential, like verifying label colours on pharmaceutical packaging or ensuring correct component orientation based on color marks. Their function revolves around analyzing the wavelength or intensity of reflected light to identify specific targets.
The functions of photoelectric sensors permeate industrial automation and beyond:
- Object Detection & Presence: Confirming parts are present for assembly, tracking products on conveyors, verifying package filling levels.
- Position Verification: Ensuring robotic arms pick up components correctly, checking pallet position in warehouses.
- Counting: Tallying bottles, cans, pills, or other discrete items moving on a line.
- Level Monitoring: Detecting the fill level in bins or tanks (often using multiple sensors).
- Dimension Checking: Verifying object height, width, or diameter using specialized sensors like convergent beam.
- Web Break Detection: Sensing if materials like paper, plastic film, or textiles break or run out.
- Safety Applications: Used in Light Curtains and Safety Scanners to create invisible safety zones around hazardous machinery.
Choosing the right photoelectric sensor involves a careful assessment of the application: What is the target? What’s the required sensing range? Environmental conditions (dust, moisture, temperature extremes)? Speed of detection? Mounting constraints? Understanding the precise function needed is the first step to unlocking the immense potential these reliable optical guardians offer. Their ability to perform non-contact, high-speed, and precise detection makes them utterly indispensable in building smarter, more efficient, and safer automated systems across every conceivable industry. They truly are the unseen