датчик диффузного отражения
- time:2025-07-23 16:03:04
- Нажмите:0
The Essential Guide to Diffuse Reflective Sensors: Unpacking Their Operation & Widespread Impact
Ever wondered how self-checkout lanes “see” your groceries pass by, how garage doors know to stop when something’s in the way, or how automated factories flawlessly count products on a conveyor? More often than not, the unsung hero enabling these everyday marvels is a датчик диффузного отражения. This remarkably versatile and robust sensing technology is a cornerstone of modern automation, offering a simple yet highly effective solution for countless object detection tasks.
Decoding the Principle: Beyond Simple Reflection
At its core, a diffuse reflective sensor (often simply called a Диффузионный датчик) operates on a fundamentally different principle than its beam-breaking or specular reflection counterparts. Unlike:
- Through-Beam Sensors: Which require a separate transmitter and receiver unit, creating a light beam broken by an interrupting object.
- Retro-Reflective Sensors: Which rely on a reflector bouncing the light beam directly back to a combined transmitter/receiver unit, also interrupted by an object blocking the beam.
…the diffuse sensor functions entirely within a single housing. Here’s the elegant science:
- Integrated Emitter: The sensor contains an infrared (IR) or sometimes visible light emitter (LED).
- Illumination: This emitter constantly projects a light beam outward.
- Diffuse Reflection: When this beam strikes a surface within its detection range, the light doesn’t bounce back cleanly like a mirror (specular reflection). Instead, it scatters in all directions because most real-world surfaces (plastic, cardboard, wood, fabric, skin, etc.) are rough at a microscopic level. This scattered reflection is known as diffuse reflection.
- Integrated Receiver: Positioned right next to (or around) the emitter within the same housing is a photodetector (receiver).
- Detection Logic: In the absence of a target object, the receiver typically sees minimal reflected light because the emitted light scatters away. When a target object enters the detection zone, a portion of this diffusely scattered light bounces back towards the sensor housing and impinges on the receiver. The sensor’s internal circuitry detects this significant increase in received light intensity.
- Output Signal: Based on the received light level crossing a predefined threshold, the sensor triggers its output signal (e.g., switches ON or OFF, provides an analog value).
Essentially, the diffuse sensor detects the presence of an object by sensing the light diffusely reflected from the object’s surface itself.
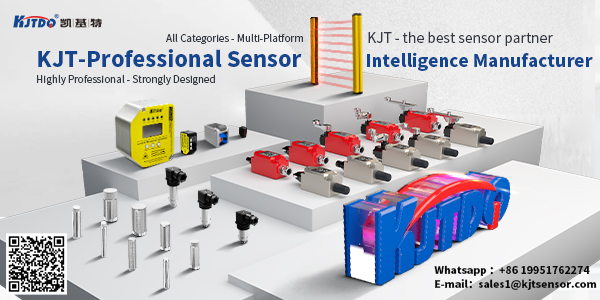
Core Components: Anatomy of a Diffuse Sensor
Understanding the key parts clarifies functionality:
- Light Source (Emitter): Typically an infrared LED for insensitivity to ambient light. Red or laser light sources are used for specialized applications requiring smaller spots or longer ranges.
- Photodetector (Receiver): Usually a phototransistor or photodiode, tuned to be sensitive to the emitter’s wavelength.
- Optics: Lenses often shape the emitted beam and focus the receiver’s field of view, optimizing range and detection characteristics. Some sensors use co-axial optics for very precise detection.
- Signal Processing Circuitry: The brain behind the operation. It powers the emitter, adjusts sensitivity (often via potentiometer or teach-in), amplifies the receiver signal, compares it to the detection threshold, and controls the output switching.
- Output Stage: Switches (PNP/NPN transistor) or analog outputs (0-10V, 4-20mA) to interface with controllers (PLCs, robots).
Why Choose Diffuse? Key Advantages Driving Adoption
This single-housing design translates into significant practical benefits:
- Simplified Installation & Setup: Arguably the biggest advantage. Only one unit needs to be mounted and wired, drastically reducing installation time, complexity, and cost compared to through-beam or retro-reflective sensors requiring alignment of separate components. Wiring is significantly simpler.
- Cost-Effectiveness: Fewer components (only one housing, one connection point) make diffuse sensors generally less expensive than equivalent through-beam or retro-reflective pairs.
- Adaptability to Various Targets: Capable of detecting objects with non-reflective, matte, or uneven surfaces that wouldn’t work well with specular reflection principles. Doesn’t require a specific reflector.
- Compact Size: The integrated design allows for very small sensor heads, ideal for tight spaces.
Navigating the Limitations: Understanding the Trade-Offs
While highly versatile, diffuse sensors have inherent characteristics to consider:
- Sensitivity to Object Properties: Detection reliability and range are highly dependent on the target object’s color, surface texture, and material. Light-colored, matte objects reflect much more light and are detected at greater distances than dark-colored, shiny, or highly absorbent objects. Background suppression technology is a crucial advancement addressing this (see below).
- Shorter Usable Ranges: Due to the inverse square law governing diffuse reflection (light intensity weakens rapidly with distance), typical practical detection ranges are shorter than those achievable with through-beam or retro-reflective sensors. Ranges vary significantly based on object reflectivity.
- Ambient Light Sensitivity: While IR emitters help, extremely bright ambient light (direct sunlight, powerful spotlights) hitting the receiver can potentially saturate it or cause false triggers. Proper shielding and sensor selection mitigate this.
- Background Interference: Without suppression technology, the sensor cannot easily distinguish between light reflected from the intended target object and light reflected from surfaces behind the target (like the machine frame or a wall), potentially causing false detections when the object moves or if the background is highly reflective.
The Power of Background Suppression (BGS): Overcoming Key Challenges
Modern diffuse sensors often incorporate Background Suppression (BGS), a sophisticated optical technique that dramatically enhances performance:
- Principle: BGS sensors use triangulation or specialized optics to measure the distance from which the received light originates.
- Benefit: They effectively “tune out” reflections coming from beyond a preset distance (the background suppression point). Only reflections originating closer than this point trigger the sensor output.
- Impact: This allows reliable detection of dark objects against potentially highly reflective backgrounds (e.g., a black rubber gasket on a shiny metal conveyor) and significantly minimizes false triggering from the background. It also makes detection less dependent on object color and reflectivity, providing more consistent performance across varied targets. Fixed-field and Adjustable-field BGS variants offer application flexibility.
Beyond Simple Presence: Analog Diffuse Sensors
While the majority are switching sensors (ON/OFF), analog diffuse sensors output a continuous signal (voltage or current) proportional to the distance to the detected object or the intensity of reflected light. This enables applications like:
- Position monitoring
- Distance measurement (within limits)
- Checking fill levels of translucent containers or detecting label presence/thickness
- Distinguishing subtle differences in surface reflectivity