аналоговый фотодатчик
- time:2025-07-23 15:17:10
- Нажмите:0
The Power of Precision: Unlocking Potential with Analog Photoelectric Sensors
Imagine a robotic arm smoothly placing components onto a circuit board. Its precision relies on knowing exactly how far away the board surface is. Or picture a bottling plant ensuring every container is filled to the perfect level, regardless of subtle variations in bottle height or clarity. These scenarios, and countless others across manufacturing, packaging, and automation, often hinge on a critical component: the аналоговый фотодатчик.
Unlike their digital counterparts that simply shout “object present” or “object absent” (like a basic on/off switch), analog photoelectric sensors whisper a continuous story. They detect subtle nuances in light intensity and translate them into a proportional electrical signal. This continuous analog output – typically ranging from 0-10 V or 4-20 mA – provides invaluable information about distance, reflectivity, transparency, or surface characteristics. It’s the difference between knowing something is there and knowing exactly where it is or precisely what state it’s in.
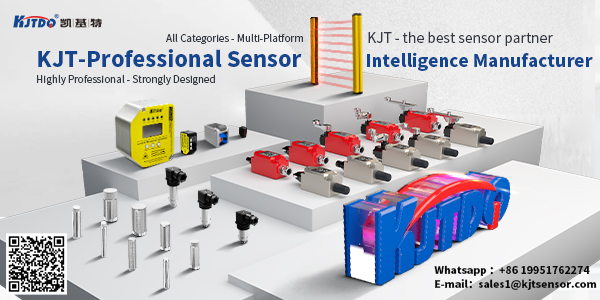
How Analog Photoelectric Sensors Work: Seeing the Unseen
At their core, all photoelectric sensors operate on the same fundamental principle: light emission, transmission, and reception. An internal light source (commonly infrared LED for its immunity to ambient light interference) projects a beam. A receiver, positioned strategically depending on the sensor type, detects this light. The key differentiator lies in the receiver’s output stage.
- Digital Sensors: The receiver circuitry acts like a strict judge. It compares the received light intensity to a pre-set threshold. If the intensity is above the threshold, it outputs a high signal (e.g., 24V). If it’s below, it outputs a low signal (0V). Simple, binary, limited.
- Analog Sensors: Here, the receiver circuitry is an interpreter. Instead of a simple threshold comparison, it outputs a continuously varying voltage or current signal that is directly proportional to the amount of light falling on the receiver element. More light received equals a higher output signal; less light equals a lower signal. This raw, proportional data is the sensor’s valuable “analog voice.” The real magic happens when you listen to this voice.
Key Sensor Types Explained
Understanding how the light beam travels is crucial. There are three primary configurations where analog output provides significant advantages:
- Diffuse Reflective (Proximity Mode): The emitter and receiver sit together in one housing. Light travels out, hits a target, and bounces back to the receiver. What makes analog special here? The strength of the return signal depends heavily on the target’s distance and reflectivity. An analog sensor doesn’t just detect presence; its output signal tells you how reflective the target is or provides a measure of its distance. This is invaluable for detecting varying surface finishes or objects at different ranges within its detection field.
- Retroreflective: The sensor head contains both emitter and receiver, but they rely on a separate reflector (prism or tape) placed opposite. The emitter’s light beam is bounced back by the reflector directly to the receiver. An object breaking this beam causes a drop in received light. Analog Advantage: While often used for presence detection like digitals, the analog output accurately indicates the degree of beam interruption. This is critical for detecting semi-transparent objects (like thin films, clear bottles) or measuring how much of the beam is blocked (e.g., edge guiding, fill level estimation in clear containers). The change in signal is proportional to opacity or beam obstruction area.
- Through-Beam (Transmissive): The emitter and receiver are in separate, opposing housings. The emitter projects light directly across a gap to the receiver. Objects passing through this gap interrupt the beam. Analog Power: Similar to retroreflective, the analog output provides a continuous measure of the beam interruption intensity. This allows for highly reliable detection of translucent objects, dust, or slight variations in web materials (paper, film) that might not fully block the beam but cause significant attenuation. It provides continuous feedback on transmission loss.
Why Choose Analog? Critical Applications
The beauty of the continuous signal output unlocks capabilities far beyond simple object detection:
- Precise Distance Measurement: In diffuse mode, the changing signal strength as a target moves closer or farther away allows for non-contact, continuous distance sensing. This is perfect for monitoring positions, controlling travel limits, or guiding robotic arms where smooth motion is essential.
- Detecting Semi-Transparent Targets: Digital sensors struggle mightily with clear glass, thin plastics, or liquids. Analog sensors excel here. The subtle reduction in light intensity caused by these materials is easily captured by the analog signal’s nuance, allowing for reliable detection and monitoring, crucial in packaging and quality control.
- Surface Reflectivity & Color Differentiation: Materials with different colors or finishes reflect light differently. Analog sensors can distinguish between these based solely on the strength of the reflected signal. This enables tasks like sorting by color, verifying label presence (often more reflective than the container), or checking surface quality consistency.
- Continuous Level Monitoring: Used in diffuse or retroreflective mode aimed at the surface of a material in a container (grain, powder, liquid), the changing reflection profile as the level rises or falls translates directly into a changing analog signal. This provides real-time, continuous level feedback without the need for multiple point-level digital sensors.
- Web Tension & Edge Guiding: In converting or printing machinery, monitoring the position of a moving web (paper, film, fabric) relative to a fixed point is vital. Analog through-beam or retroreflective sensors tracking the web edge provide the continuous positional feedback needed for precise closed-loop control systems.
- Intensity-Based Quality Control: Subtle variations in material composition, thickness, or coating can cause slight changes in how much light passes through (transmission) or is reflected. Analog sensors are sensitive enough to detect these variations, enabling real-time quality checks on production lines.
The Irresistible Advantage: Beyond On/Off
The core strength of the analog photoelectric sensor lies in its linear output relationship to the detected light parameter. It provides a magnitude, not just a state. This inherent capability for dynamic response – constantly reporting the degree of change – makes it uniquely suited for tasks demanding precision, differentiation of subtle variations, and continuous process monitoring. It transforms simple presence detection into rich, actionable data.
While digital sensors excel at robust, high-speed presence detection, analog sensors step in when the application requires more finesse. Their ability to quantify the interaction between light and the target environment provides engineers and designers with a powerful tool for optimizing processes, enhancing quality control, and achieving unparalleled levels of automation precision. From ensuring a bottle is perfectly filled to guiding a robot with micron-level accuracy, the analog photoelectric sensor delivers the nuanced information needed to truly unlock potential in an increasingly demanding industrial landscape.