Фотоэлектрический вилочный датчик
- time:2025-07-23 12:24:10
- Нажмите:0
Photoelectric Fork Sensors: Your Essential Guide to Reliable Object Detection
In the humming heart of modern automation, where speed, precision, and reliability are paramount, countless processes rely on knowing one fundamental thing: Is the object there? Whether it’s a bottle moving down a conveyor, a component entering an assembly machine, or a label precisely positioned for application, detecting presence or absence is critical. This is where the often unsung hero, the Фотоэлектрический вилочный датчик, shines with remarkable effectiveness and simplicity.
Imagine a sturdy U-shaped bracket – the “fork” – housing two crucial components directly opposite each other: one an infrared light emitter, the other a receiver. This integrated design is the defining characteristic of a Фотоэлектрический вилочный датчик, also frequently known as a fork light barrier or U-shaped sensor. Its operation hinges on a straightforward yet powerful principle: the through-beam detection method. The emitter constantly projects a focused beam of infrared light across the gap to the receiver. When an object passes through the fork, it physically interrupts this beam. The receiver instantly detects this loss of light signal, triggering an output switch within the sensor (like turning a digital signal from “dark” to “light”, or vice versa, depending on configuration). This rapid electronic signal tells the controlling system, “Object detected!”.
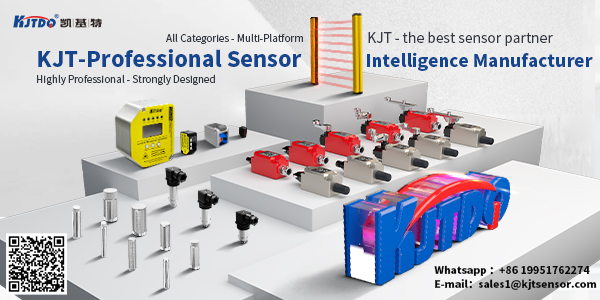
Why Choose a Photoelectric Fork Sensor? The Advantages Speak Volumes
The inherent design of the fork sensor delivers several compelling advantages that make it a preferred choice for countless applications:
- Unmatched Ease of Alignment: This is arguably its biggest strength. Because the emitter and receiver are factory-aligned and rigidly mounted within a single fork housing, there’s no complex setup or calibration needed during installation. Simply mount the sensor in position, ensuring objects pass through the gap, and it’s ready to go. This eliminates the tedious and time-consuming alignment process required when using separate emitter and receiver units.
- Exceptional Stability & Reliability: The fixed optical axis guarantees consistent beam alignment. Once installed, it’s highly resistant to misalignment caused by vibration, minor bumps, or thermal shifts – common challenges in industrial environments. This translates to consistent, dependable detection and reduced downtime.
- High Switching Frequency & Speed: Designed for fast-moving production lines, fork sensors boast extremely high response times, often in the microsecond range. They can reliably detect objects zipping through the gap at very high speeds.
- Precision Object Detection: The well-defined beam path allows for high positional accuracy. They excel at detecting very small objects, verifying the presence of specific features (like tabs or flags on components), or precisely detecting the leading or trailing edge of a product.
- Robustness: Built for demanding factory floors, these sensors typically feature rugged housings (often metal) resistant to impacts, dust, and sometimes even washdown conditions depending on the IP rating. They offer reliable performance in challenging environments.
Key Specifications to Consider When Selecting a Fork Sensor
Choosing the right Фотоэлектрический вилочный датчик involves evaluating several critical parameters to match your application:
- Sensing Gap (Width): This is the distance between the inner faces of the fork arms. Objects must fit comfortably through this gap to be detected. Common sizes range from just a few millimeters for tiny components up to large gaps handling substantial packages.
- Sensing Depth: How far into the gap does the detection zone extend? Crucial for ensuring detection occurs reliably regardless of minor object position variations within the fork.
- Beam Height/Aperture: The vertical dimension of the light beam at the gap. Affects the minimum detectable object size and resistance to stray light.
- Response Time/Frequency: How quickly can the sensor detect the beam interruption and change its output? Vital for high-speed applications.
- Output Type: Common options include:
- PNP (Sourcing): Outputs positive voltage when active.
- NPN (Sinking): Outputs a ground path when active.
- Relay: Useful for directly switching higher-power loads.
- Analog: Provides a variable signal proportional to the amount of light received (less common in standard fork sensors).
- Connection: M8 or M12 quick-disconnect connectors are industry standards.
- Housing Material: Typically stainless steel or robust plastic (PBT), chosen based on environmental demands.
- Protection Rating (IP): Indicates resistance to dust and liquids (e.g., IP65, IP67, IP69K for harsh washdown). Selecting the correct IP rating is essential for longevity.
- Light Source: Almost always infrared (IR) LEDs for immunity to ambient light interference. Some specialized variants might use visible red light for easier alignment checks, though IR dominates for reliability.
Where Photoelectric Fork Sensors Excel: Diverse Applications
Their unique blend of precision, speed, and reliability makes fork sensors indispensable across industries:
- Packaging & Filling Lines: Detecting bottles, cans, cartons on conveyors; verifying cap presence; counting items; triggering filling heads or labeling machines. Their speed is vital here.
- Перевозка материалов: Monitoring product flow on conveyors; detecting jams; verifying pallet presence; triggering sorting gates or diverters.
- Assembly Automation: Confirming component insertion; detecting missing parts; verifying the position of levers, gears, or flags; triggering next-stage processes. Precision detection is key.
- Printing & Converting: Detecting sheet/paper feed; verifying registration marks; controlling web guiding systems.
- Woodworking & Metalworking: Detecting board presence for sawing; verifying workpiece position in CNC machines; counting cut pieces.
- Textile Industry: Monitoring yarn breaks; detecting selvage edges; controlling fabric feed.
- Security/Fire Safety: Used in some specialized safety light curtains or door interlock systems.
Installation Tips for Optimal Performance
While inherently easier to install than separate sensors, maximizing the performance of your Фотоэлектрический вилочный датчик involves some best practices:
- Secure Mounting: Ensure the sensor is firmly fixed to prevent vibration-induced movement. Use appropriate brackets if needed.
- Avoid Obstructions: Keep the gap clear of any debris, stray wires, or other objects that could falsely interrupt the beam.
- Consider Object Properties: Ensure the object is large/opaque enough to reliably block the beam. Transparent objects might require specialized sensors or reflective markers.
- Mind the Environment: While rugged, excessive buildup of dust, mist, or oil can eventually coat the lenses and impair function. Ensure the IP rating is adequate and perform routine cleaning if necessary. Protect against strong, direct ambient light sources shining into the receiver aperture.
- Check Connection & Wiring: Verify the correct voltage supply and proper connection to the PLC or control system according to the datasheet.
The Simple Powerhouse of Detection
In a world of complex sensing technologies, the Фотоэлектрический вилочный датчик stands out for its elegant simplicity, inherent reliability, and plug-and-play operation. By integrating the emitter and receiver into a single, robust U-shaped housing, it solves the critical challenge of precise beam alignment in through-beam detection. The result is a sensor offering unmatched stability, high speed, and consistent performance for detecting the presence or absence of objects. From bustling production lines to intricate assembly systems, its ability to provide a definitive “Да.” or “Нет!” signal makes it a cornerstone technology, ensuring efficient, accurate, and reliable automated processes across countless industries.