индукционный датчик
- time:2025-07-11 00:07:11
- Нажмите:0
How Inductive Sensors Revolutionize Position Detection Without Contact
Imagine monitoring the position of a rapidly moving robotic arm, ensuring a safety door is securely closed before machinery starts, or detecting the precise fill level in a metal tank – all without the sensor ever physically touching the target. This is the fundamental magic and practical brilliance of inductive type sensors. These ubiquitous workhorses in industrial automation silently perform critical tasks based purely on electromagnetic principles, offering reliability where other technologies falter. Understanding their operation and strengths is key to unlocking their potential in countless applications.
At their core, inductive sensors are non-contact proximity sensors. They excel at detecting the presence or absence, and often the distance, of metallic objects within their sensing range. Unlike mechanical switches that wear out or optical sensors that can be blinded by dirt, inductive sensors thrive in harsh, dirty environments like machine shops, production lines, or foundries. Their robustness and lack of moving parts translate directly to reduced downtime and lower maintenance costs.
The Operating Principle: Harnessing Electromagnetic Fields
The magic lies in Faraday’s Law of Induction and the phenomenon of eddy currents. Here’s a breakdown of the process:
- Generating the Field: Inside the sensor’s active face, an electronic oscillator generates a high-frequency alternating magnetic field. This field extends outwards from the face of the sensor.
- Target Interaction: When a conductive metal target (like steel, aluminum, brass, copper, etc.) approaches this magnetic field, it doesn’t simply ignore it. The changing magnetic field induces swirling electrical currents within the metal itself – these are known as eddy currents.
- Energy Drain and Detection: The creation of these eddy currents consumes energy. This energy loss happens directly from the oscillator circuit within the sensor. As the target moves closer, more energy is absorbed by the eddy currents, causing the oscillator’s amplitude to decrease.
- Signal Processing: Sophisticated circuitry within the sensor continuously monitors the oscillator’s amplitude (or sometimes its frequency). When the amplitude drops below a predetermined threshold due to a sufficiently close target, the sensor’s solid-state switching element (usually an NPN or PNP transistor) changes state.
- Output Signal: This state change is the sensor’s output signal. It typically manifests as a discrete ON/OFF signal (e.g., 0V or 24V DC), clearly indicating the presence or absence of the target within the defined sensing range. This simple, robust signal is ideal for feeding into Programmable Logic Controllers (PLCs) and other control systems.
Why Choose an Inductive Sensor? Core Advantages
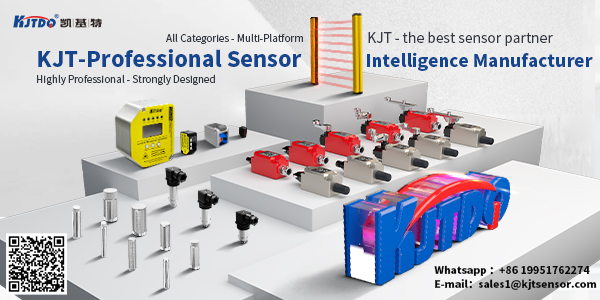
The operating principle translates into several compelling advantages that solidify their dominance in industrial settings:
- Non-Contact Operation: This is paramount. No physical wear occurs between the sensor and the target, leading to exceptionally long service life, especially important for high-cycle applications. The sensor doesn’t bump, scrape, or abrade the target.
- High Reliability & Longevity: With no moving parts to jam or mechanical contacts to arc and degrade, these sensors boast excellent reliability and longevity, often lasting for years or even decades in demanding environments.
- Robustness: Inductive sensors are virtually impervious to dirt, dust, oil, grease, moisture, and vibrations – common adversaries in industrial settings. Many are rated IP67, IP68, or IP69K, meaning they can withstand washdowns, submersion, and high-pressure cleaning.
- High Switching Speeds: Capable of detecting targets moving at very high speeds (kHz range), making them ideal for counting fast-moving parts or monitoring rapid machine movements.
- Insensitivity to Ambient Light: Unlike optical sensors, they are completely unaffected by ambient light, welding flashes, or total darkness.
- Variety: Available in diverse shapes, sizes, sensing ranges (from fractions of a millimeter up to several centimeters), output types (DC 2-wire, 3-wire NPN/PNP, analog, IO-Link), and housing materials (nickel-plated brass, stainless steel, plastic) to fit almost any application requirement.
Understanding Limitations: Material Sensitivity & Range
While powerful, inductive sensors aren’t universal proximity detectors. Their key limitation is material specificity. They reliably detect:
- Ferrous Metals: Iron, steel (best detection range and sensitivity).
- Non-Ferrous Metals: Aluminum, brass, copper, etc. (requires a shorter sensing range than ferrous metals).
Crucially, they generally cannot detect:
- Non-metallic materials (plastic, wood, glass, paper, liquids like water or oil).
- Pure magnetic fields alone (without a conductive target).
Additionally, the sensing range is inherently finite and relatively short compared to technologies like ultrasonic sensors. The achievable range is also significantly influenced by the target material type, size, and shape. Smaller targets require closer detection than larger ones.
Where Inductive Sensors Shine: Real-World Applications
Their unique blend of features makes them indispensable across countless industrial sectors:
- Position Detection: Verifying cylinder piston position in pneumatic or hydraulic systems, checking end-of-travel on linear slides or conveyors, confirming gear position in transmissions.
- Presence/Absence: Counting metal parts on a conveyor belt, detecting the presence of a tool in a holder, confirming a metal lid is on a container, ensuring a robot gripper has secured a metal workpiece.
- Speed Monitoring: Measuring the rotational speed of gear teeth or detecting the passage of targets (e.g., bolts) for speed calculation.
- Safety Interlocks: Ensuring machine guards or safety doors are correctly closed before equipment starts (e.g., detecting the latch position).
- End-of-Travel Detection: Providing precise limits for moving parts without mechanical stops. Critical for preventing over-travel damage.
- Fill Level Monitoring: Detecting the presence of a metal float in a tank to determine liquid levels.
- Machine Tooling: Tool breakage detection, tool changer positioning, chuck clamping confirmation.
Selecting the Right Inductive Sensor
Choosing the optimal inductive sensor involves several key factors:
- Target Material: Ferrous metal, non-ferrous metal? This drastically affects the required sensing range. Sensor data sheets list separate nominal ranges (Sn) for steel and various non-ferrous materials like aluminum or brass (typically 30-60% of the steel range).
- Required Sensing Range (Sn): How far away does the sensor need to reliably detect the target? Factor in the target material (see point 1) and ensure the sensor’s nominal range meets the application’s distance requirement.
- Operating Environment: Temperature extremes? Exposure to chemicals, oils, coolants, washdowns? Vibration levels? Choose an appropriate housing material (stainless steel highly recommended for harsh environments) and IP rating.
- Electrical Requirements: Power supply voltage (commonly 10-30V DC)? Required output type (2-wire AC/DC vs. 3-wire NPN/PNP sourcing vs. analog)? Output current rating?
- Size & Mounting: Physical constraints necessitate specific barrel sizes (e.g., M5, M8, M12, M18, M30) or rectangular/flat designs. Flush or non-flush mounting capabilities are also crucial; shielded (flush-mountable) sensors have a shorter range but allow mounting flush in metal, while unshielded (non-flush) offer longer ranges but require a metal-free surrounding zone.
- Special Features: Needs like resistance to welding fields, high-temperature ratings (>100°C), analog output (0-10V or 4-20mA for distance measurement), or IO-Link communication for digital data exchange require specific sensor variants.
Inductive sensors stand as a testament to elegant engineering solving practical problems. Their ability to reliably detect metal targets without contact, coupled with incredible durability and speed, makes them fundamental building blocks in modern manufacturing, automation, and countless other industrial processes. Their simple output signal