индукционный датчик приближения
- time:2025-07-11 00:00:07
- Нажмите:0
The Unseen Guardian: How Inductive Proximity Sensors Revolutionize Industrial Detection
Inductive Proximity Sensors: The Robust, Non-Contact Solution for Metal Detection
Imagine a high-speed assembly line where robotic arms move with blinding speed. How do they know precisely when a metal component is in position for welding or gripping, without ever touching it? The silent, unsung hero ensuring this flawless operation is often the индукционный датчик приближения. This remarkably reliable device forms the backbone of modern industrial automation, offering a robust, non-contact method for detecting the presence or absence of metallic objects. Understanding its operating principle and wide-ranging applications is crucial for optimizing machinery efficiency, enhancing safety, and ensuring smooth production flow.
At its core, an inductive proximity sensor is an electronic proximity switch specifically designed to detect ferrous and non-ferrous metals without physical contact. Unlike mechanical limit switches prone to wear, inductive sensors offer wear-free operation, significantly reducing maintenance downtime and costs. Their fundamental operation relies on the principles of electromagnetic induction.
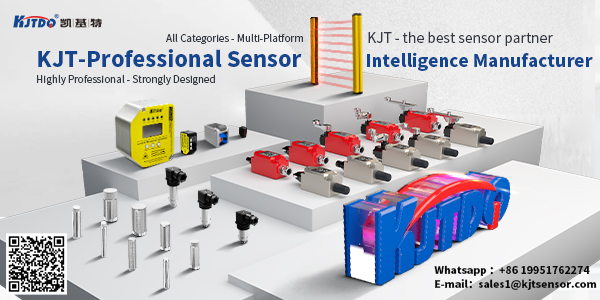
Here’s how an индукционный датчик приближения works its magic:
- The Oscillator: Inside the sensor’s face (sensing surface), a coil is connected to a high-frequency oscillator circuit. This generates a constantly fluctuating electromagnetic field that radiates outward from the active surface.
- The Eddy Current Effect: When a metallic target enters this electromagnetic field, tiny circulating electrical currents, known as eddy currents, are induced on the surface of the target material. This is a direct consequence of Faraday’s law of induction.
- Field Dampening: The creation of these eddy currents draws energy from the sensor’s own oscillating circuit. This effectively dampens the amplitude of the electromagnetic field generated by the coil.
- Detection Circuit & Signal Switch: A dedicated circuit within the sensor continuously monitors the strength of the oscillation. When the damping reaches a sufficient threshold (indicating a target is close enough), the sensor triggers its solid-state switching element (typically a transistor). This changes the sensor’s output state (e.g., from OFF to ON, or vice-versa), signaling the presence of the target.
- Target Departure: As the target moves away from the sensing range, the eddy currents diminish, the oscillation amplitude recovers, and the sensor returns to its original output state.
The key features enabled by this inductive working principle make these sensors indispensable:
- Non-Contact Operation: Eliminates physical wear and tear on both the sensor and the target, ensuring unparalleled longevity and reliability. This is perhaps their most significant advantage.
- Прочная структура: Typically housed in durable materials like nickel-plated brass, stainless steel, or rugged plastics (PBT), inductive sensors are exceptionally resistant to dust, dirt, oils, coolants, and vibrations. Many achieve high IP (Ingress Protection) ratings like IP67 or IP69K.
- High Switching Frequency & Speed: Capable of detecting objects at incredibly high speeds (thousands of times per second), perfect for fast-moving assembly lines or counting applications.
- Reliable in Harsh Environments: Their sealed design and lack of moving parts make them ideal for demanding industrial settings where other sensor types might fail. They are unaffected by ambient light, water spray, or grime.
- Simple Installation & Operation: Generally featuring two or three wires for power and output, they are relatively easy to integrate into control systems (PLCs).
Where do Inductive Proximity Sensors Shine? Their versatility makes them ubiquitous across countless industries:
- Position Sensing: Verifying the presence/absence of machine parts (e.g., cylinder end position, pallet location, robotic arm position). “Is the metal part in place for the next operation?”
- End-of-Travel Detection: Replacing mechanical limit switches on actuators, slides, and conveyors.
- Object Counting: Counting metallic objects on a conveyor belt (e.g., cans, bottles with metal caps, machined parts).
- Speed Monitoring: Detecting the teeth of a rotating metal gear to calculate rotational speed.
- Level Control: Detecting the presence of liquid metal or metallic powders in bins or hoppers.
- Machine Safety: Used as components within safety circuits to confirm guards are closed or dangerous zones are clear.
Choosing the Right Inductive Proximity Sensor involves considering several factors:
- Sensing Range: The maximum distance at which the sensor can reliably detect a standard target. This varies significantly between models.
- Target Material: Different metals (steel, aluminum, brass, stainless steel) affect the effective sensing range. Always consult the sensor datasheet for correction factors. Ferrous metals generally provide the longest ranges.
- Target Size & Shape: Small targets may require a sensor with a shorter, focused sensing range or a reduced-flush-mountable design.
- Housing Style & Size: Cylindrical (e.g., M8, M12, M18, M30) or rectangular block styles are common. Choose based on available space and mounting constraints.
- Electrical Output Type: NPN vs. PNP transistors, NO (Normally Open) vs NC (Normally Closed) switching logic. Must be compatible with the control system input (PLC input card).
- Flush or Non-Flush Mounting: Flush-mountable sensors can be installed embedded in metal without affecting their operation, offering better protection. Non-flush types offer longer ranges but require surrounding clearance.
- Environmental Ratings: Ensure the IP rating and temperature range suit the operating environment.
Looking ahead, advancements in inductive sensor technology continue. Miniaturization allows for installation in incredibly tight spaces. Sensors are becoming smarter, incorporating features like IO-Link communication for parameterization, diagnostics, and process data integration into Industry 4.0 frameworks. Improved immunity to electrical noise and enhanced performance with challenging targets like thin aluminum foil are also ongoing developments.
In essence, the индукционный датчик приближения is a triumph of practical engineering. By harnessing the invisible power of electromagnetic induction, it provides an extraordinarily durable, reliable, and cost-effective solution for detecting metal in the demanding world of automation. Its non-contact nature, robustness, and versatility ensure it remains a fundamental component in factories worldwide, silently enabling the precise, efficient, and automated processes we rely on every day. Understanding its core inductive principle empowers engineers and technicians to deploy these sensors effectively, maximizing system uptime and productivity.