inductive coil sensor
- time:2025-07-10 00:49:10
- Нажмите:0
Inductive Coil Sensors: The Invisible Workhorses Powering Modern Automation
Imagine a world where machines operate blindly, unable to sense the presence, position, or condition of objects around them. Production lines would halt, vehicles would malfunction, and countless automated processes would fail. Thankfully, we don’t live in that world, largely due to the silent, often unseen operation of sensors like the inductive coil sensor. These remarkably robust devices serve as the fundamental eyes of countless industrial and automotive systems, translating physical proximity into reliable electrical signals using the timeless principles of electromagnetic induction.
Unveiling the Core Principle: Faraday’s Law in Action
At its heart, an inductive coil sensor operates on the foundational laws discovered by Michael Faraday. The core component is precisely that – a coil of wire wound around a ferromagnetic core. When an alternating current (AC) flows through this coil, it generates an oscillating electromagnetic field around the sensor head. This is the sensor’s active zone.
Here’s where the magic happens: When a metallic object (typically ferrous, but often non-ferrous metals work too) enters this electromagnetic field, eddy currents are induced on the surface of the target object. According to Faraday’s Law of Induction, these eddy currents create their own opposing magnetic field, which interacts with the field generated by the coil.
This interaction changes the characteristics of the sensor’s coil circuit itself. Specifically, it causes a measurable shift in the inductance of the coil and/or an increase in energy loss (damping) within the oscillator circuit driving the coil. The sensor’s integrated electronics detect this change, processes it, and triggers an output signal – typically switching a solid-state output ON or OFF – indicating the presence of the target.
Key Components and Variations
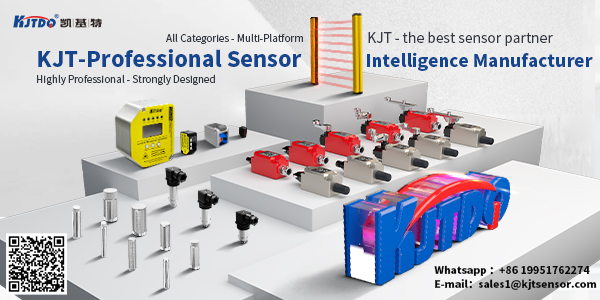
While the principle is elegant, practical implementation involves several key elements:
- The Sensing Coil: The heart of the device, generating the electromagnetic field. Its design and core material significantly influence range and sensitivity.
- Oscillator: Creates the high-frequency AC current fed through the coil.
- Demodulator/Detector: Monitors the oscillator’s condition (amplitude or frequency shift) caused by the target entering the field.
- Output Circuit: Converts the detection signal into a usable output, most commonly a solid-state switch (PNP/NPN transistor) for discrete signals, though analog variants exist providing distance-proportional output. Proximity sensors are the most ubiquitous type of inductive coil sensor.
- Housing: Protects the internal electronics from environmental factors like dust, moisture, chemicals, and physical impact, contributing to the sensor’s legendary robustness.
Beyond basic proximity detection, inductive coil sensors form the basis of more complex devices:
- Inductive Position Sensors (LVDTs/RVDTs): Use multiple coils to provide precise linear or rotary position measurements.
- Resolver Sensors: Employ coils to measure the absolute angular position of a rotor shaft with high accuracy, vital in demanding applications like aerospace and robotics.
- Inductive Encoders: Detect the position or speed of rotating metallic objects using patterned targets and sensing coils.
Where You’ll Find Them: Ubiquitous Applications
The reliability, durability, and non-contact nature of inductive coil sensors make them indispensable across a vast array of industries:
- Factory Automation: Counting objects on conveyors, verifying part presence/jaw closure in robotic arms, detecting end-of-stroke in cylinders, monitoring machine tool positions. Their immunity to dirt, oil, and vibration makes them ideal for harsh plant floors.
- Automotive: Detecting gear position, brake pad wear monitoring (indirectly), suspension position sensing, anti-lock braking system (ABS) wheel speed sensing (using metallic tone wheels).
- Перевозка материалов: Monitoring fill levels in tanks (with float targets), detecting metal in packaging lines, controlling elevator floor levels.
- Machining & Metalworking: Tool breakage detection, workpiece positioning on CNC machines, spindle orientation.
- Аэрокосмическая деятельность: Landing gear position detection, flap/slat position monitoring.
- Consumer Products: Lid closure detection in appliances (washing machines, printers), tamper detection mechanisms.
The Compelling Advantages: Why Choose Inductive?
The dominance of inductive coil sensors in industrial settings isn’t accidental. They offer a unique combination of benefits:
- Non-Contact Operation: No physical wear on the sensor or target, leading to an exceptionally long operational lifespan.
- Extreme Ruggedness: Highly resistant to shock, vibration, dirt, dust, oil, and water (often IP67/IP68 rated or higher). Can operate in very high or low temperatures.
- Reliability: Few moving parts and robust construction result in outstanding operational reliability and minimal maintenance needs.
- High Switching Frequency: Capable of detecting rapidly moving targets at speeds unsuitable for mechanical switches.
- Immunity to Environmental Factors: Unlike optical sensors, they are unaffected by ambient light, dust, smoke, or fog (provided these aren’t metallic or conductive).
- Cost-Effectiveness: Generally offer a very favorable price-to-performance ratio, especially for standard proximity sensing tasks.
Understanding Limitations: It’s Not Magic
While incredibly versatile, inductive coil sensors have inherent limitations to consider:
- Metallic Targets Only: They fundamentally require a conductive metal target to operate. Plastics, wood, liquids (unless conductive, like salt water), and ceramics are generally invisible to them.
- Limited Sensing Range: The effective sensing distance is relatively short, typically a few millimeters up to about 60mm for very large industrial sensors. The range is affected by the target size, shape, and material.
- Target Material Dependency: The sensing range varies significantly between different metals. Ferrous metals (iron, steel) offer the longest range. Non-ferrous metals like aluminum, brass, or copper have a shorter “factor” (e.g., 50% of the rated range for steel). Sensor specifications clearly state the reference target material (usually mild steel).
- Not for Fine Positioning (Basic Models): While specialized inductive sensors (LVDTs) excel at precision, standard proximity sensors provide a simple ON/OFF signal at a preset distance, not fine-grained distance measurement.
Selecting the Right Inductive Sensor: Key Considerations
Choosing the optimal inductive coil sensor requires analyzing several factors:
- Required Sensing Distance: Always consider the “effective operating distance” and the reduction factor for non-steel targets.
- Target Material: Know what metal the sensor needs to detect and apply the appropriate correction factor.
- Output Type Needed: Discrete (NPN/PNP NO/NC) or Analog (0-10V, 4-20mA)? What voltage level (e.g., 12-24V DC)?
- Environmental Conditions: Temperature extremes, washdown requirements (IP69K?), exposure to chemicals or welding sparks?
- Electrical Connection: Pre-wired cable, quick-disconnect (M8/M12 connector), or terminal block?
- Size and Form Factor: Cylindrical (threaded barrel), rectangular block, or specialized shape? Must it fit a specific mounting location?
- Shielding: Shielded sensors have a more focused electromagnetic field directed forward, allowing flush mounting in metal. Unshielded sensors have a larger lateral field but require some clearance around them when mounted.
The Unseen Engine of Efficiency
From the relentless pace of an automotive assembly line to the precise movements of a robotic arm and the safety systems in modern aircraft, inductive coil sensors function as the silent, dependable sentinels. They translate