индуктивный датчик
- time:2025-07-10 00:42:10
- Нажмите:0
The Unseen Force: How Inductance Sensors Power Precision in Our Automated World
Indductance Sensors: The Silent Sentinels of Modern Automation
Imagine parking your car, guided by unseen beacons that sense the proximity of concrete walls without a single touch. Or picture a high-speed production line where components fly into place, precisely detected and positioned by an invisible force field. This isn’t science fiction; it’s the pervasive, often overlooked reality enabled by inductance sensors. These robust and reliable workhorses form a critical backbone in countless industrial, automotive, and consumer applications, operating silently yet indispensably through the fundamental principles of electromagnetism.
At their core, inductance sensors are a specific type of датчик приближения designed primarily to detect the presence or absence of metallic objects without physical contact. They achieve this remarkable feat through the magic of magnetic fields and Faraday’s Law of Electromagnetic Induction.
How Does an Inductance Sensor Work? The Physics Unveiled
Every индуктивный датчик contains a critical component: a coil wound around a ferrite core. When an alternating electrical current flows through this coil, it generates an oscillating magnetic field that emanates from the sensor’s active face. This magnetic field is the sensor’s “sensing range.”
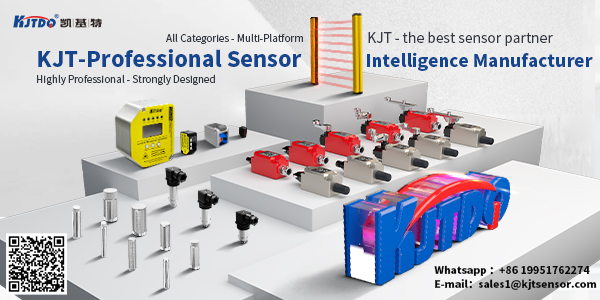
Here’s where the key principles kick in:
- The Magnetic Field: The energized coil creates this dynamic field.
- Eddy Currents: When a conductive metal target (like steel, aluminum, copper, brass, etc.) enters this magnetic field, something fascinating happens. The changing magnetic field induces swirling electrical currents within the target material itself. These are called eddy currents.
- The Opposition (Lenz’s Law): According to Lenz’s Law, these induced eddy currents generate their own magnetic field, which opposes the original magnetic field produced by the sensor’s coil.
- Impedance Shift: The opposition from the target’s magnetic field effectively loads the sensor’s coil. This changes the coil’s electrical characteristics – specifically, it increases the coil’s impedance (a combination of resistance and inductive reactance to AC current).
- Detection & Signal Processing: The sensor’s built-in electronic oscillator and evaluation circuitry constantly monitor the coil impedance or the amplitude of the current oscillation. A significant change (caused by the eddy currents from a nearby target) triggers the sensor’s output to switch state (e.g., from OFF to ON or vice-versa). This output signal is then used by the control system.
Why Choose Inductance Sensors? Key Characteristics and Advantages
The fundamental operating principle grants inductance sensors several distinct advantages that make them highly desirable in demanding environments:
- Non-Contact Operation: The absence of physical contact means no wear and tear on the sensor or target, leading to virtually limitless operational life and eliminating mechanical stress.
- Robustness: Typically housed in rugged materials like nickel-plated brass or stainless steel and often Potted (filled with epoxy) internally, they are highly resistant to dust, dirt, moisture, oil, vibration, and harsh chemicals. Many boast high IP ratings (Ingress Protection) like IP67 or IP68.
- High Switching Frequencies: Capable of detecting rapidly moving targets at speeds far exceeding mechanical switches or even many other sensor types – crucial for high-speed automation lines.
- Insensitivity to Surface Conditions: Factors like dirt, dust, or minor condensation on the target usually don’t affect detection reliability (unlike optical sensors), as the sensor interacts with the target material itself electromagnetically.
- Long Sensing Ranges (for inductive): While limited compared to ultrasonic or photoelectric sensors, they offer respectable non-contact detection ranges, typically proportional to the sensor head diameter (e.g., a 12mm sensor might detect 4mm).
Where Inductance Sensors Shine: Diverse Applications
Their unique blend of features makes inductance sensors ubiquitous across industries:
- Factory Automation & Robotics: Position sensing (end-of-arm tools, cylinder position), part counting on conveyors, presence/absence detection (e.g., verifying a drill bit is present), machine guarding (non-contact limit switches). High reliability is paramount here.
- Automotive Manufacturing & Components: Detecting pistons, gears, shafts; verifying valve position; sensing clutch or brake pedal positions; counting camshaft rotations. Harsh environments demand their robustness.
- Перевозка материалов: Monitoring conveyor belt speed via detecting metallic segments; pallet presence detection in warehousing systems.
- Станки: Tool breakage detection (sensing the presence of a metallic tool tip), spindle position control, workpiece positioning on CNC machines.
- Consumer Products: Coin detection in vending machines and gaming devices, lid/door position detection in appliances (where metallic parts are involved).
Not Without Considerations: Understanding Limitations
Like any technology, inductance sensors have specific boundaries:
- Metal Targets Only: Their fundamental reliance on inducing eddy currents means they only detect conductive metals. Non-metallic objects (plastic, wood, paper, liquids, human skin) are invisible to a standard inductive sensor.
- Target Material & Size Impact: Different metals affect the sensing range. Ferrous metals (like steel) are detected at longer ranges than non-ferrous metals (like brass or aluminum). Very small targets may fall below the minimum detectable size.
- Limited Sensing Range: Compared to optical or ultrasonic sensors, their air gap range is relatively short.
- Temperature Effects: Extreme temperatures can slightly alter the sensing distance, though high-quality sensors compensate well within their specified operating range.
- Mutual Interference: Placing multiple sensors very close together can cause their magnetic fields to interfere, requiring careful spacing or specialized designs.
Inductance vs. Capacitance Sensors: A Quick Comparison
Особенности |
Inductance Sensor |
Capacitance Sensor |
Detection Principle |
Eddy currents in metal targets |
Change in capacitance by any material |
Primary Target |
Metallic objects only |
Metals, plastics, liquids, powders, wood, etc. |
Effect of Material |
Range varies significantly with metal type |
Range varies with material permittivity |
Effect of Target Size |
Requires minimum detectable size |
Can detect very small targets |
Typical Environment |
Robust for dirty, wet, oily conditions |
Sensitive to contamination/humidity |
The Indispensable Engine of Detection
From the relentless pace of an automotive assembly line to the intricate choreography of robotic arms and the mundane reliability of your washing machine lid switch, inductance sensors operate silently and effectively. Their mastery of electromagnetic principles, particularly harnessing eddy currents induced in metal targets, provides a blend of ruggedness, reliability, and non-contact operation that is unmatched for metallic object detection. They are fundamental building blocks in modern industrial automation, transportation, and countless devices, proving that unseen forces – governed by Faraday’s insights – are often the most critical in powering our technological world. Their continued evolution ensures they remain essential for precision detection tasks in metal-rich environments.