smc proximity sensors
- time:2025-07-07 11:10:44
- Нажмите:0
Unlock Precision & Efficiency: SMC Proximity Sensors as the Heartbeat of Modern Automation
In the relentless hum of the modern factory floor or the intricate dance of automated machinery, unseen heroes tirelessly monitor positions, detect objects, and safeguard processes. Among these critical components, proximity sensors stand as fundamental enablers of feedback and control. When seeking peak reliability, durability, and seamless integration within demanding industrial environments, SMC proximity sensors emerge as the trusted choice for engineers and system integrators worldwide. Understanding their capabilities is key to unlocking new levels of efficiency and machine intelligence.
Beyond Touch: The Power of Non-Contact Sensing
Unlike mechanical limit switches requiring physical contact, inductive proximity sensors, a core specialty of SMC, operate on the principle of electromagnetic induction. They detect the presence of metallic objects without ever touching them. Here’s how it works:
- The Sensor’s Coil: An oscillator circuit generates a high-frequency electromagnetic field emanating from the sensor’s sensing face.
- Target Interaction: When a conductive metal target (like steel, aluminum, brass) enters this field, tiny eddy currents are induced on the target’s surface.
- Field Dampening: The creation of these eddy currents absorbs energy from the sensor’s oscillating circuit, causing a measurable change – typically a dampening of the oscillation amplitude.
- Signal Output: The sensor’s built-in electronics detect this amplitude change. When it crosses a pre-defined threshold, the sensor triggers its output switch (PNP/NPN transistor or analog signal), signaling the presence of the target.
SMC’s Mastery in Proximity Technology: Types and Specializations
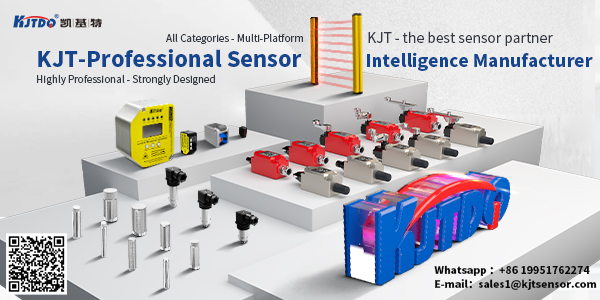
SMC offers a comprehensive portfolio of proximity sensors, extending beyond just inductive variants, meeting diverse application needs:
- Inductive Proximity Sensors: The backbone of industrial metal detection. SMC excels in providing variants in various form factors (cylindrical, block-shaped), sensing distances (from millimeters to tens of millimeters), housing materials (robust stainless steel, nickel-plated brass, PBT plastic), connection types (pre-wired cables, connectors), and output configurations. Models often feature IP67, IP68, or IP69K ratings, crucial for operation in environments exposed to dust, coolants, oils, or high-pressure washdowns common in automotive manufacturing or food & beverage processing.
- Capacitive Proximity Sensors: While inductive sensors need metal targets, конденсаторный датчик detect the presence of nearly any material – liquids, plastics, powders, wood, glass, or even different types of metal. They work by sensing changes in capacitance caused by the target material entering the electrostatic field. SMC capacitive sensors are indispensable for tasks like detecting filled containers, monitoring liquid levels in non-metallic tanks, or verifying the presence of labels/plastic parts on production lines.
- Magnetic Proximity Sensors: These detect the presence of permanent magnets. They are frequently used in conjunction with pneumatic cylinders featuring embedded magnets in the piston. SMC magnetic sensors provide a highly reliable means to confirm cylinder piston position (extended/retracted) for critical sequencing logic.
Why SMC Proximity Sensors Dominate Industrial Landscapes
Choosing SMC proximity sensors translates into tangible operational advantages:
- Reliability & Longevity: Engineered for industrial harshness, SMC sensors resist shock, vibration, extreme temperatures, and chemical exposure. Their non-contact nature inherently eliminates mechanical wear, leading to significantly extended lifespans and reduced downtime compared to mechanical switches.
- Precise Detection: High repeatability ensures that objects are detected with consistent accuracy cycle after cycle, critical for maintaining tolerances in precision assembly or machining operations.
- Speed: Capable of detecting targets at high speeds (kHz range), SMC proximity sensors keep pace with fast-moving production lines, enabling maximum throughput. Their instantaneous response is vital for high-speed counting or position verification.
- Ease of Installation & Integration: A vast range of sizes, mounting styles (flush or non-flush mounting for inductive), and connection options (M8/M12 connectors, cables) simplify integration into both new machinery and retrofits. Wider sensing ranges on some models offer greater mounting flexibility. Compatibility with standard PLC inputs is a given.
- Robust Environmental Resistance: The prevalence of high IP ratings (IP67, IP68, IP69K) across the range means reliable operation in challenging conditions – from dusty warehouses and machine shops to environments requiring frequent cleaning with water jets, such as food processing plants or pharmaceutical cleanrooms.
- Cost-Effectiveness Over Time: While the initial purchase price might be comparable to compes, the combination of exceptional durability, minimal maintenance requirements, and prevention of costly production stoppages delivers a superior total cost of ownership.
Critical Applications Driving Modern Automation
SMC proximity sensors are ubiquitous across nearly every sector where automation exists:
- Position Detection: Confirming the presence or end position of machine components (slides, arms, cylinders), workpieces on conveyors, tool holders, or clamps. Magnetic sensors specifically excel at cylinder position feedback.
- Object Counting: Accurately tallying products on high-speed lines, bottles on filling lines, or components feeding into an assembly station.
- Level Control: Capacitive sensors reliably detect fill levels of liquids, granular materials, or powders in tanks, silos, or hoppers, often constructed from non-metallic materials.
- End-of-Arm Tooling (EOAT): Verifying part pickup/drop-off and tool presence on robotic arms in demanding automotive assembly or electronics manufacturing.
- Speed Monitoring: Detecting the rotation of gears or sprockets equipped with metallic targets for speed feedback or overspeed protection.
- Safety & Error Detection: Confirming guards are closed, doors are secured, or that a part is correctly positioned before initiating a potentially hazardous machine cycle. Preventing jams by detecting missing parts on feeders.
SMC: More Than Just a Sensor Supplier
SMC isn’t just known for its extensive proximity sensor catalog. Their unique strength lies in providing complete automation solutions. Sensors seamlessly integrate with SMC’s world-leading pneumatic components (valves, cylinders, FRLs), vacuum products, and sophisticated control platforms. This ecosystem approach simplifies design, procurement, installation, troubleshooting, and ongoing maintenance for system builders. Furthermore, SMC’s global technical support network provides invaluable expertise for selecting the optimal sensor variant for any specific, challenging application.
Выводы
In the intricate choreography of industrial automation, unseen signals drive visible results. SMC proximity sensors – whether inductive for metal detection, capacitive for diverse materials, or magnetic for cylinder positioning – are the silent, dependable sentinels providing essential machine intelligence. Their unmatched reliability, durability under pressure, precision sensing capabilities, and ease of integration make them a cornerstone technology. By leveraging the power of SMC proximity sensors, engineers empower machines with the critical feedback needed to operate efficiently, safely, and intelligently, pushing the boundaries of what’s possible in manufacturing and process automation. Choosing SMC is an investment in operational resilience and long-term performance.