Фотоэлектрический датчик приближения
- time:2025-07-07 08:44:52
- Нажмите:0
Photoelectric Proximity Sensors: The Eyes of Modern Automation
Imagine a factory humming with activity. Bottles whizz by on a conveyor belt, robotic arms assemble components with precision, and doors slide open silently as workers approach. Behind these seamless interactions often lies a small, unassuming hero: the Фотоэлектрический датчик приближения. These ubiquitous devices are fundamental to countless automated processes, acting as the invisible eyes that detect objects, ensure positioning accuracy, and trigger actions without physical contact. Understanding how they work and why they are so widely adopted is key to appreciating modern industrial efficiency.
How Does a Photoelectric Proximity Sensor Work? The Core Principle
At its heart, a Фотоэлектрический датчик приближения operates on a beautifully simple principle: it uses light to detect the presence or absence of an object within its detection range. It contains two essential components housed within a single unit or positioned separately:
- Emitter: This component, typically an infrared (IR) LED, generates a beam of light (usually invisible to the human eye). Some types use visible red light or even laser light for specialized applications requiring high precision or long ranges.
- Receiver: This component, typically a phototransistor or photodiode, detects the light emitted by the emitter. Its electrical state changes dramatically depending on whether it receives the light beam or not.
The detection principle hinges on the interruption or reflection of this emitted light beam by the target object. The sensor’s integrated electronics continuously monitor the receiver’s signal. When the object interacts with the light, the signal change is processed, ultimately triggering the sensor’s output switch (like turning on or off a transistor).
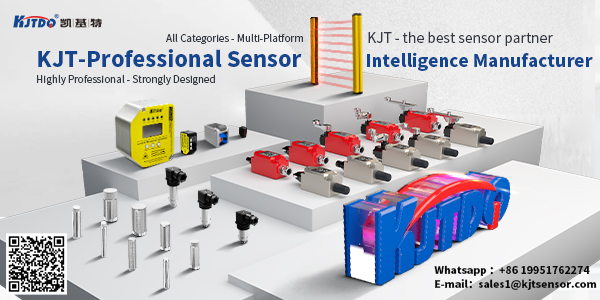
Key Types: Choosing the Right “Light Path”
Not all objects or environments are the same. Photoelectric proximity sensors come in distinct configurations to tackle diverse detection challenges:
- Through-Beam Sensors (Opposed Mode):
- How it Works: The emitter and receiver are separate units, positioned opposite each other. The emitter sends a beam directly to the receiver. Detection occurs when an object physically interrupts this beam.
- Strengths: Longest detection ranges (often meters), highest reliability (requires complete interruption), excellent performance in dusty/dirty environments (the beam is strong).
- Weakness: Requires mounting two separate components with precise alignment, which can be more complex and costly for installation.
- Retro-Reflective Sensors (Reflex Mode):
- How it Works: The emitter and receiver are housed together. A special reflector (often prismatic tape or a dedicated reflector plate) is mounted opposite the sensor. The emitter sends a beam towards the reflector, which bounces it back to the receiver. Detection occurs when an object interrupts this reflected beam path.
- Strengths: Easier installation than through-beam (only sensor and reflector need alignment, wiring only at sensor side), good range (though typically less than through-beam), cost-effective.
- Weakness: Requires a reflector. Shiny or reflective targets might confuse the sensor by bouncing light back themselves (polarized filters often solve this). Dust/grime on the reflector can impair performance.
- Diffuse Reflective Sensors (Proximity Mode or Diffuse Mode):
- How it Works: The emitter and receiver are housed together. The emitter sends light towards the target object. The target object itself reflects some of this light diffusely (scatters it) back towards the receiver. Detection occurs when the receiver senses enough reflected light.
- Strengths: Simplest installation – only needs one component mounted near the detection point. Detects objects without any separate reflector. Wide variety of housings and beam patterns.
- Weakness: Detection range is shortest and highly dependent on the target’s size, color (darker absorbs light), and surface reflectivity. Background objects can cause false triggers if they are reflective and close enough. Performance can be affected by ambient light extremes or dirty environments.
Why Choose Photoelectric Proximity Sensors? The Compelling Advantages
The dominance of Фотоэлектрический датчик in industrial automation isn’t accidental. They offer a powerful combination of benefits:
- Non-contact detection: The single most critical advantage. No physical touch means zero wear and tear on the sensor or the target object, enabling ultra-long operational lifespans and suitability for delicate items.
- Fast Response Times: These sensors detect and switch outputs incredibly quickly, often in microseconds. This high-speed capability is essential for modern high-throughput production lines.
- Long Detection Ranges: Especially true for through-beam sensors, photoelectric proximity sensors can detect objects from millimeters up to tens of meters away, offering great flexibility.
- Многогранность: They can detect virtually any material type – metal, plastic, wood, glass, liquid (level), cardboard, etc. – as long as it interacts with light.
- High Reliability and Repeatability: When correctly selected and installed, these sensors provide exceptional accuracy and consistency over long periods.
- Compact and Robust Designs: Modern sensors are built tough for demanding industrial environments, featuring rugged housings resistant to vibration, moisture (many IP67+ rated), and common chemicals.
Ubiquitous Applications: Where Do You Find Them?
Photoelectric proximity sensors are truly the workhorses of countless industries:
- Manufacturing/Assembly: Bottle/can presence on fillers/cappers, label detection, part presence/positioning on conveyors, robotic arm guidance, end-of-stroke detection, palletizing/depalletizing, machine guarding.
- Packaging: Detecting cardboard flaps, verifying case sealing, counting items through a chute, film break detection in wrapping machines, label application verification.
- Перевозка материалов: Detecting objects on conveyors (start/stop control), level detection in bins/silos (drip, bulk), package dimensioning for sorting systems, presence detection at loading docks.
- Food & Beverage: Bottle/can presence, cap on/off detection, fill level control (transparent bottles), conveyor jam detection.
- Automotive: Detecting parts in presses, verifying door/window positions, weld nut detection, component presence during robotic assembly.
- Building Automation: Automatic doors (detect approaching people), elevator door safety, people counting, security systems.
Selecting and Using: Key Considerations
Choosing the right Фотоэлектрический датчик приближения is crucial for optimal performance:
- Detection Task: What exactly needs to be detected? (Presence, absence, position, level, count?)
- Target Properties: Size, color, material, surface finish (shiny, matte)? These drastically impact Диффузионный датчик performance.
- Required Range: How far away is the target?
- Environment: Is it dusty, humid, steamy, filled with spray or vibration? What’s the ambient light level like? Choose an appropriate housing rating (IP67, IP69K, etc.) and sensing mode.
- Mounting Constraints: Space limitations? Is a reflector feasible? Sensor size/form factor?
- Output Type: NPN or PNP transistor? Normally Open (NO) or Normally Closed (NC)? Analog output for distance measurement? Logic-level compatible?
Installation and Maintenance Tips:
- Secure Mounting: Ensure the sensor (and reflector if applicable) is rigid