термостойкий датчик приближения
- time:2025-07-04 03:55:13
- Нажмите:0
Heat Resistant Proximity Sensors: Mastering Detection in the Crucible of Industry
Imagine a foundry where molten metal flows like liquid fire, temperatures soaring past 1000°C. Or a glass manufacturing line, glowing sheets moving rapidly amidst intense radiant heat. In these infernos, standard proximity sensors – the workhorses of automation – would simply melt, fail, or deliver wildly inaccurate readings. This is the critical challenge that heat resistant proximity sensors are engineered to conquer. They are not mere sensors; they are specialized guardians enabling automation to thrive where others cannot, ensuring safety, precision, and productivity in the most thermally hostile environments.
The Crucible: Why Heat is the Enemy of Standard Sensors
Standard inductive, capacitive, or photoelectric proximity sensors are precision instruments designed for moderate environments. When subjected to extreme temperatures, several critical failures occur:
- Material Degradation: Plastics melt, deform, or lose structural integrity. Seals fail, allowing contaminants and moisture ingress. Metals can warp, affecting sensing distance and alignment.
- Electronic Failure: Sensitive internal circuitry, especially integrated circuits (ICs) and soldering points, exceed their thermal operating limits, leading to malfunction or permanent damage.
- Signal Instability: Temperature fluctuations cause expansion/contraction in components, altering inductance, capacitance, or optical properties, resulting in unreliable, drifting signals or false triggers.
- Reduced Lifespan: Continuous exposure to high heat drastically accelerates the aging process of all components, leading to premature failure and costly downtime.
The consequence? Unplanned stops in critical processes, safety hazards from undetected objects or equipment, poor product quality due to inconsistent positioning, and high replacement costs.
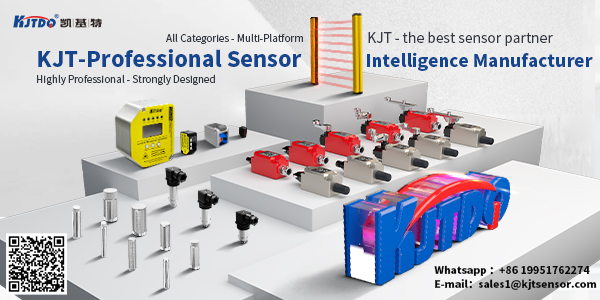
Forged in Fire: Key Technologies Powering Heat Resistance
Heat resistant variants are fundamentally re-engineered to withstand these punishing conditions. Several core technologies converge to achieve this resilience:
- Advanced Materials:
- Specialized Plastics: Moving beyond standard polymers, these sensors employ high-temperature thermoplastics like PEEK (Polyether Ether Ketone), PTFE (Teflon), or PI (Polyimide). These materials retain strength and dimensional stability far beyond 200°C, often up to 250°C, 260°C, or even 300°C continuously.
- Ceramics: Used for sensing faces, housings, or internal components, ceramics offer exceptional thermal stability, electrical insulation, and resistance to thermal shock at temperatures exceeding 1000°C.
- High-Temperature Alloys: Stainless steel (particularly grades like 316L) remains vital, but specialized nickel or cobalt-based alloys are sometimes used for extreme corrosion/heat combinations.
- Robust Seals: Viton or Kalrez fluorocarbon elastomers replace standard nitrile or silicone seals, maintaining integrity at much higher temperatures.
- Thermal Management & Armored Design:
- Thermal Barriers: Strategic placement of ceramic or insulating materials internally shields the sensitive electronics from direct heat radiated or conducted from the sensing face.
- Extended Bodies / Cooling Fins: Some designs feature elongated bodies or integrated cooling fins, increasing surface area for heat dissipation away from the electronics housing. Passive air cooling is enhanced by the sensor’s physical design.
- Active Cooling (Specialized): In the most extreme scenarios (e.g., continuous >300°C), sensors might be integrated with forced air or water-cooled jackets, though this adds complexity.
- Armored Construction: Enhanced mechanical protection against physical impact and thermal stress, often with thicker walls or specialized coatings.
- Optimized Sensing Technology: While the core principles (inductive, capacitive, photoelectric) remain, components are chosen or modified for thermal stability:
- High-temperature stable coils and cores for индукционный датчик.
- Special dielectrics and electrode materials for конденсаторный датчик.
- High-temperature lenses, light sources (e.g., specific LEDs with better thermal tolerance), and detectors for Фотоэлектрический датчик. Fiber optic variants are often preferred for the harshest photoelectric applications, keeping the sensitive amplifier remotely cooled.
Where the Heat is On: Critical Applications
The demanding nature of these sensors means they are deployed where reliability is non-negotiable:
- Metal Processing: Foundries (molten metal handling, casting lines, die casting), forging presses, heat treatment furnaces, continuous casting, hot rolling mills. Monitoring molds, ladles, billets, and robot positions amidst intense heat and splatter.
- Glass Manufacturing: Forming lines, annealing lehrs, tempering ovens. Detecting glass sheets, gobs, molds, and position controls where temperatures are extreme and radiative heat is intense.
- Plastic & Rubber Processing: Injection molding machines (near heated nozzles and barrels), extrusion lines, vulcanization presses. Ensuring mold clamping, ejection, and part presence despite proximity to heaters.
- Ceramics & Cement Kilns: Monitoring material movement within or near the scorching environment of rotary kilns.
- Automotive Manufacturing: Paint shop ovens (curing lines), welding applications near heat sources.
- Power Generation: Monitoring coal-fired boiler components, gas turbine areas, or other high-heat zones.
- Food & Beverage: Industrial ovens, sterilization processes, frying operations where heat and potential washdown combine.
The Unyielding Advantages: Beyond Just Survival
Investing in properly specified high-temperature proximity sensors delivers tangible benefits:
- Unmatched Reliability: Minimize costly unplanned downtime caused by sensor failure in critical high-heat zones. Operational continuity is paramount.
- Повышение безопасности: Ensure accurate detection of machine guards, tooling positions, and material presence, preventing accidents in hazardous environments.
- Improved Process Control: Maintain precise positioning and timing, crucial for product quality in demanding manufacturing processes. Consistent signals prevent faults.
- Extended Service Life: Withstand the thermal degradation that cripples standard sensors, significantly reducing replacement frequency and associated costs. Long-term cost-effectiveness despite a higher initial price.
- Reduced Maintenance: Engineered for endurance in tough conditions, requiring less frequent intervention than standard sensors struggling near their thermal limits.
Choosing the Right Sentinel
Selecting the optimal термостойкий датчик приближения requires careful consideration:
- Maximum Ambient Temperature: The most crucial spec. Does it cover peak and sustained temperatures? (Look for continuous operating temp ratings).
- Required Sensing Distance: Performance can vary slightly with temperature; ensure specs are met within the operating range.
- Sensing Technology: Inductive for metals, capacitive or photoelectric for non-metals. Fiber optics excel for photoelectric in severe heat.
- Environmental Factors: Beyond heat: presence of spl