датчик приближения цветных металлов
- time:2025-07-04 03:43:11
- Нажмите:0
Non-Frous Proximity Sensors: Detecting the Undetectable for Smarter Automation
Imagine a high-speed bottling line where clear plastic containers whizz by. Traditional metal-sensing proximity sensors remain inert, oblivious to the crucial components made of plastic, glass, or aluminum passing inches away. This is the domain where non-ferrous proximity sensors shine – specialized devices engineered to detect the presence or absence of materials that conventional inductive sensors cannot. These unsung heroes of industrial automation unlock capabilities essential for modern manufacturing and process control, ensuring efficiency and reliability where standard tools fall short.
Understanding the Core Technology: Beyond Ferrous Metals
Standard inductive proximity sensors generate an electromagnetic field and detect disturbances caused by ferrous metals like iron and steel. When these metals enter the field, eddy currents are induced, changing the sensor’s oscillation amplitude, triggering an output signal. Simple, effective, but fundamentally limited.
Non-ferrous proximity sensors overcome this limitation. While they are often still fundamentally inductive sensors, they are specifically designed and tuned to detect materials that do not exhibit strong ferromagnetic properties. These include:
- Metals: Aluminum, copper, brass, bronze, titanium, stainless steel (austenitic grades).
- Non-Metals: Plastic, glass, wood, cardboard, paper, ceramics, liquids (depending on type).
The Inductive Approach: Tuning for Specifics
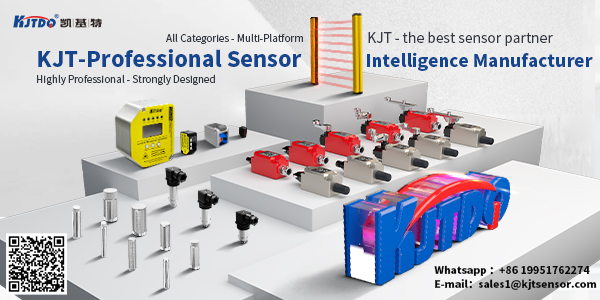
Inductive non-ferrous sensors work on the same core electromagnetic principle as their ferrous-detecting counterparts. However, critical design differences enable them to “see” the weaker influence of non-ferrous metals:
- Higher Operating Frequencies: They typically operate at significantly higher frequencies (often in the hundreds of kHz range). This makes them more sensitive to the capacitive effects and eddy currents generated in lower-conductivity materials like aluminum.
- Specialized Coil Design: The internal coil (oscillator coil) and associated circuitry are optimized. This might involve using materials like aluminum for the coil itself, or intricate winding patterns, to maximize sensitivity to the specific electromagnetic signature of non-ferrous targets.
- Sophisticated Signal Processing: Advanced electronic circuits provide high-precision damping measurement, distinguishing the subtle changes caused by non-ferrous metals from background noise or environmental factors.
For non-ferrous metals, the sensor detects the eddy currents induced in the material, albeit weaker than in ferrous metals. For non-metallic materials, detection relies on the capacitive effect – detecting changes in capacitance when the dielectric material (like plastic or wood) enters the field. Inductive sensors optimized for non-ferrous detection usually have a stronger capacitive coupling element in their design, giving them sensitivity to a broader range of materials.
Capacitive Sensors: The Non-Metal Specialists
While inductive sensors can be tuned for non-ferrous detection, capacitive proximity sensors are often the primary choice for reliably detecting non-conductive materials like liquids, powders, plastics, wood, and glass. They generate an electrostatic field rather than an electromagnetic one.
- Electrostatic Field Generation: The sensor face acts as one plate of a capacitor; the target (or background) acts as the other.
- Dielectric Constant Detection: When a material (the dielectric) enters this field, it changes the capacitance of the system. The magnitude of this change depends on the material’s dielectric constant (εr).
- Detection Threshold: Once the capacitance change exceeds a pre-set threshold (adjustable on most sensors), the sensor triggers its output.
Capacitive sensors offer unparalleled versatility for non-metallic materials. They can detect through non-metallic container walls (e.g., monitoring liquid levels in plastic tanks) and are less susceptible to dust and other contaminants affecting the target surface compared to some optical methods.
Where Non-Ferrous Detection Powers Industries
The ability to reliably detect diverse materials without physical contact makes these sensors indispensable in countless applications:
- Packaging & Labeling: Detecting plastic bottles, glass jars, cardboard boxes, filled vs. empty containers, verifying label presence on non-metallic packages. Ensuring accuracy and preventing jams.
- Food & Beverage: Monitoring fill levels in plastic bottles or glass containers on conveyors, detecting caps (plastic/aluminum), verifying stacked cartons, controlling ingredient flow (e.g., flour, sugar). Critical for hygiene and compliance.
- Automotive: Verifying the presence of plastic components (bumpers, trim, fluid reservoirs), aluminum engine parts, brake fluid level in reservoirs, detecting plastic spools on wire harnesses. Essential for assembly line integrity.
- Pharmaceuticals: Detecting plastic vials, blister packs, glass ampoules, verifying fill levels through containers, monitoring presence of pills in bottles. Requires high reliability and often washdown-rated sensors.
- Woodworking & Furniture: Detecting wooden boards, MDF panels, verifying glue bead application, sensing stacks of paper or cardboard. Crucial for precision wood processing.
- Metal Processing: Distinguishing between different types of non-ferrous metals (e.g., sorting aluminum vs. brass), detecting aluminum billets, monitoring position of copper wire spools, verifying presence of stainless steel parts.
Key Advantages Driving Adoption
Why choose non-ferrous proximity sensors? The benefits are compelling:
- Material Versatility: Their primary advantage – detecting a vast array of materials traditional sensors miss.
- Non-Contact Operation: Like all proximity sensors, they offer wear-free sensing, eliminating mechanical wear and tear, leading to longer service life and reduced maintenance.
- High Reliability & Speed: Immune to surface dirt (within limits), unaffected by target color or surface finish (unlike optical sensors), and capable of very high switching frequencies (thousands of Hertz), making them ideal for high-speed automation.
- Environmentally Robust: Available in rugged housings (IP67, IP69K) with resistance to dust, moisture, oils, and chemicals. Inductive variants are particularly robust in harsh industrial environments.
- Simplified Installation: Easy to integrate into machinery without complex mechanics, reducing setup time.
Choosing the Right Sensor: Key Considerations
Selecting the optimal non-ferrous proximity sensor requires careful thought:
- Target Material: What exactly needs detecting? (Aluminum, copper, plastic, glass, liquid)? This is fundamental.
- Required Sensing Distance: Nominal sensing distance (Sn) varies significantly between sensor types (inductive, capacitive) and specifically with the target material. Always refer to manufacturer specs for your specific target. Capacitive sensors often require closer proximity than inductive ones for equivalent materials.
- Sensor Type (Inductive vs. Capacitive):
- Inductive: Generally preferred for non-ferrous metals (Al, Cu, brass). More robust against environmental interference (EMC) typically. Requires a “conductive” target.
- Capacitive: Essential for non-conductive materials (plastic, wood, liquids) and also works for metals. Can detect through non-metallic container walls. Sensitivity often adjustable for different materials. Can be