Датчик приближения пластмассы
- time:2025-07-03 03:06:56
- Нажмите:0
Plastic Proximity Sensors: Revolutionizing Non-Contact Detection with Polymer Innovation
Imagine a factory floor where robotic arms move with lightning speed, precisely assembling delicate components. Or picture a sleek modern faucet turning water on automatically as your hands approach. At the heart of these seemingly effortless interactions often lies a critical, yet frequently overlooked component: the датчик приближения. And increasingly, the unsung hero in these scenarios is crafted not from metal, but from plastic. Plastic proximity sensors are rapidly transforming industries by offering a compelling blend of cost-efficiency, design freedom, and robust performance previously unattainable with their traditional metal-housed counterparts.
So, what exactly is a Датчик приближения пластмассы? At its core, it performs the same fundamental function as any other proximity sensor: detecting the presence, absence, or position of an object without physical contact. They achieve this through various principles like inductive, capacitive, ultrasonic, or optical (photoelectric) sensing. The revolutionary difference lies in the material used for the sensor housing and often critical internal components – high-performance engineering plastics and polymers.
Why Choose Plastic? The Compelling Advantages
The shift towards polymer-based proximity sensors isn’t arbitrary; it’s driven by tangible, significant benefits:
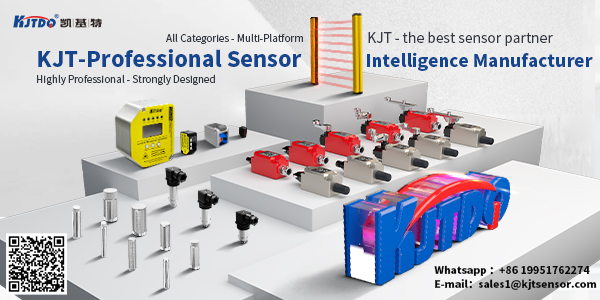
- Unmatched Cost Efficiency: Plastic materials are inherently less expensive than metals like stainless steel or brass. This translates directly to lower manufacturing costs for the sensors themselves. Furthermore, plastic housings can often be produced using efficient methods like injection molding, especially for high volumes, further reducing per-unit costs. This makes plastic proximity sensors highly accessible for budget-conscious applications or large-scale deployments.
- Unparalleled Design Flexibility & Freedom: Injection molding plastic gives engineers tremendous freedom to create complex sensor housing shapes that would be prohibitively expensive or even impossible to achieve with metal machining. This allows for ergonomic designs, easier integration into specific mounting spaces, and the creation of unique form factors tailored to niche applications. Designers can also incorporate features like integral clips, mounting flanges, or cable strain reliefs directly into the housing mold.
- Superior Corrosion & Chemical Resistance: This is arguably one of the most significant advantages. Engineering plastics like PBT (Polybutylene Terephthalate), PP (Polypropylene), or PVDF (Polyvinylidene Fluoride) offer exceptional resistance to a vast array of chemicals, solvents, cleaning agents, and corrosive atmospheres. This makes plastic proximity sensors ideal for harsh environments common in industries like:
- Chemical Processing: Resisting splashes and vapors.
- Food & Beverage: Withstanding aggressive washdowns (CIP/SIP) using caustic or acidic solutions.
- Water Treatment: Enduring constant moisture and treatment chemicals.
- Marine Applications: Resisting saltwater corrosion.
- Lightweight Construction: Plastic housings are significantly lighter than metal housings. This is crucial in applications where weight savings are critical, such as in robotics and mobile machinery, reducing strain on moving parts and improving overall system efficiency.
- Electrical Insulation: Plastics are natural insulators. Plastic housings provide inherent electrical insulation, enhancing safety and reducing the risk of short circuits compared to their conductive metal counterparts, especially important in compact or high-voltage environments.
Where Plastic Proximity Sensors Shine: Key Applications
The unique advantages of non-contact plastic sensors make them the optimal choice across diverse sectors:
- Food & Beverage & Pharmaceutical: Crucial for hygiene and sanitation. Resistant to frequent high-pressure, high-temperature washdowns using caustic and acidic cleaners. Used for detecting containers, fill levels, lids, or position verification on production lines.
- Chemical Processing & Water/Wastewater Treatment: Withstanding corrosive chemicals, solvents, and high humidity environments where metal sensors would rapidly degrade. Detecting tank levels, valve positions, pump operation.
- Automotive Manufacturing: Used robotically for part positioning, weld gun verification, and assembly line object detection. Lightweight and resistant to oils and coolants.
- Consumer Electronics & Appliances: Enabling touchless interfaces (faucets, soap dispensers, hand dryers), door/window position sensing, and detecting user presence due to design flexibility and cost-effectiveness.
- Medical Equipment: Finding use in diagnostic machines, automated analyzers, and dispensers where corrosion resistance and electrical safety are paramount.
- Packaging Machinery: Detecting boxes, bottles, labels, and fill levels reliably on fast-moving lines.
Understanding the Technology Inside the Plastic Shell
While the housing defines its robustness and chemical compatibility, the sensing principle determines what the Датчик приближения пластмассы can detect and its operational range:
- Inductive Plastic Proximity Sensors: Detect metallic objects only using an electromagnetic field. Excellent for detecting pistons, gears, or metal parts in machinery. Ideal for metallic object detection in harsh, dirty industrial environments.
- Capacitive Plastic Proximity Sensors: Detect any material that alters an electrostatic field (metals, plastics, wood, liquids, granules). Perfect for level detection in tanks (liquids or powders) or detecting non-metallic objects on conveyor belts.
- Photoelectric (Optical) Plastic Sensors: Use light beams (visible, infrared, laser) to detect objects. Variants include through-beam (separate emitter/receiver), retro-reflective (bounces off reflector), and diffuse (reflects off the object). Offer longer detection ranges and detect almost any material. Common for object counting, web-break detection, and precision positioning.
- Ultrasonic Plastic Proximity Sensors: Emit sound waves and detect echoes. Detect a wide range of materials and are excellent for distance measurement, level sensing (especially for challenging surfaces like foam), and object detection in dusty conditions.
Key Technical Specifications remain crucial when selecting any sensor, including plastic-bodied ones: Sensing Distance/Range, Operating Voltage, Output Type (PNP/NPN, NO/NC, Analog), Switching Frequency, Degree of Protection (IP Rating - critical for washdown environments, typically IP67, IP68, IP69K), Temperature Range, and Material Construction (specifying the plastic type, e.g., PBT).
Addressing Potential Limitations and the Future
While polymer-based sensors offer immense benefits, it’s important to acknowledge trade-offs:
- Temperature Limits: Engineering plastics generally have lower continuous operating temperature limits (e.g., often max ~85-120°C for PBT/PP) compared to specialized high-temperature metals. Careful selection for hot environments is essential.
- Mechanical Strength: While robust, most plastics cannot withstand the same level of crushing force or extreme mechanical shock as heavy-duty metal housings without reinforcement or careful design. Selecting plastics with high impact resistance is key.
- UV Degradation: Some plastics can degrade under prolonged intense UV exposure. UV-stabilized plastics are used for outdoor applications.
However, the field of plastic proximity sensor technology is constantly evolving. Advances in polymer science yield materials with enhanced temperature stability, mechanical strength, and UV resistance. Sensor fusion (combining multiple sensing principles in one plastic housing) and increased integration of smart features (IO-Link communications, diagnostics) within compact plastic units are exciting trends driving future adoption. The integration of plastic sensors into complex sensing networks within IoT frameworks is also rapidly expanding.
The Indispensable Sensor Solution
Plastic proximity sensors are far more than just a cheaper alternative. They represent a fundamental shift enabled by innovative materials science. Their **superior resistance to