pneumatic proximity sensor
- time:2025-07-03 03:00:55
- Нажмите:0
The Silent Guardians of Automation: How Pneumatic Proximity Sensors Work and Why They Shine
In the bustling heart of modern industry, where dust flies, fluids splash, and electromagnetic interference crackles, reliability is non-negotiable. Machines need to sense the presence or absence of objects reliably, often in conditions that would cripple delicate electronics. Enter the often-overlooked yet remarkably robust workhorse: the pneumatic proximity sensor. These unsung heroes leverage the power of compressed air to deliver unwavering performance where other sensors might falter. Understanding their operation and unique advantages is key to optimizing automation in demanding settings.
Despite the dominance of electronic sensing technologies, pneumatic proximity sensors remain a critical solution in numerous industrial applications. Why? At their core, they offer a fundamentally different approach: detection via air. Unlike optical sensors that rely on light beams or inductive sensors using electromagnetic fields, pneumatic variants utilize changes in air pressure or airflow triggered by the proximity of a target object. This seemingly simple principle grants them extraordinary resilience.
So, how does a pneumatic proximity sensor actually work?
The core mechanism is elegantly straightforward, focusing on air pressure detection or airflow disruption:
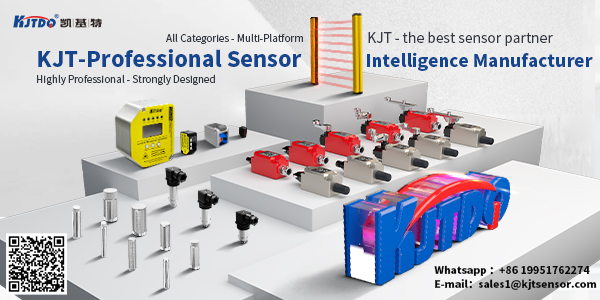
- Constant Air Supply: A regulated supply of clean, compressed air is continuously fed to the sensor through an inlet port.
- The Sensing Nozzle: This air flows through a small, precisely engineered orifice or nozzle located at the sensor’s tip. This is the critical sensing point.
- Interaction with the Target: When no object is near the nozzle, air escapes freely into the atmosphere. However, as a target object approaches the nozzle (within its specified detection range), it begins to obstruct this free airflow.
- Pressure Differential: This obstruction causes a significant change within the sensor’s internal chamber. Depending on the design:
- Backpressure Type: The restricted airflow causes pressure behind the nozzle to increase. This rising pressure is detected internally.
- Venturi/Vacuum Type (Differential Pressure): Some designs use a venturi effect. When the airstream exiting the nozzle is obstructed, it creates a pressure drop (vacuum) in a secondary chamber connected via a small bleed hole. This differential pressure is the signal.
- Signal Generation: The internally detected pressure change (increase or decrease) acts on a sensitive diaphragm, piston, or similar mechanical element. This movement either directly actuates a snap-action pneumatic pilot valve (for an on/off output) or, in amplified versions, modulates a small pilot signal that controls a larger pneumatic output.
- Output: The result is a distinct pneumatic signal – a shift in air pressure or flow at the sensor’s output port. This signal can directly actuate pneumatic valves, cylinders, or serve as an input to a pneumatic logic circuit or an interface converting it to an electrical signal.
The Compelling Advantages: Why Choose a Pneumatic Proximity Sensor?
Their unique operating principle translates into a suite of powerful benefits that make them ideal for harsh environments:
- Immunity to Electromagnetic Interference (EMI) & Radio Frequency Interference (RFI): Containing no delicate electronic components susceptible to interference from welders, motors, or variable frequency drives, pneumatic proximity sensors operate flawlessly in electrically noisy areas. This is a major advantage over electronic sensors.
- Intrinsic Safety: Since they operate purely on compressed air and generate no sparks or significant heat, pneumatic sensors are inherently explosion-proof. They are the go-to choice for hazardous locations where flammable gases, vapors, or dust are present, eliminating the need for costly additional safeguards.
- Robust Resistance to Contaminants: Impervious to dust, dirt, oil, coolants, and most chemical splashes, these sensors thrive in foundries, machine shops, food processing plants, and washdown applications where electronic sensors require constant shielding or frequent replacement.
- High Temperature Tolerance: Capable of operating reliably in ambient temperatures that would destroy or derate many electronic sensors (often exceeding 120°C / 250°F or more).
- Simple Installation and Operation: Requiring only a compressed air line and no electrical power at the sensing point, installation is often simpler and potentially safer, especially in wet zones. They integrate seamlessly into existing pneumatic systems.
- Sensing Difficult Surfaces: They reliably detect objects regardless of surface material – metal, plastic, glass, wood, rubber, liquid surfaces, or uneven textures – overcoming limitations of technologies like inductive or capacitive sensors.
Where Do Pneumatic Proximity Sensors Excel? Key Applications
Their strengths dictate their prime deployment areas:
- Hazardous Areas: Oil & gas refineries, chemical processing plants, paint booths, grain handling.
- High-Contamination Environments: Metal stamping/punching, foundries, machining centers, material handling with heavy dust/debris, paper mills.
- Food & Beverage & Pharmaceutical Processing: Areas requiring frequent washdown with caustic chemicals; intrinsically safe operation near ingredients or packaging.
- High-Temperature Processes: Foundries, die casting, heat treating lines, oven entry/exit points.
- Wet/Damp Environments: Car washes, plating lines, wastewater treatment.
- Position Sensing in Pneumatic Systems: Direct feedback on cylinder piston position, gripper actuation, or part presence within pneumatic transfer lines.
Selecting and Using Pneumatic Proximity Sensors Effectively
To harness their full potential, consider these factors:
- Detection Range: Choose a sensor with a range suitable for your application distance. Ranges are typically shorter than many electronic sensors.
- Output Type: Determine if you need a direct pneumatic pilot output (to control a valve) or an amplified output for longer signal lines or higher flow rates. Some models offer integral electrical switches activated by the pneumatic signal.
- Air Supply: Ensure clean, dry, regulated air at the specified pressure and flow rate. Contaminated air is the most common cause of failure.
- Target Characteristics: While material-agnostic, the target size, shape, and approach angle can affect reliable detection.
- Environment: Match the sensor body material (stainless steel, brass, specialized plastics) to the specific environmental challenges (corrosion, chemical exposure, impact).
- Response Time: Understand if the sensor’s switching speed meets your cycle time requirements.
In the complex landscape of industrial automation, the pneumatic proximity sensor stands as a testament to robust, reliable engineering. By harnessing the fundamental properties of air pressure and flow, it delivers critical presence detection where electronic sensors simply cannot survive. Their immunity to harsh conditions, intrinsic safety, and material versatility make them not just an alternative, but often the optimal solution for safeguarding processes and ensuring uptime in the most demanding corners of the factory floor.