distance sensor types
- time:2025-07-03 02:36:48
- Нажмите:0
Beyond Touch: Demystifying Distance Sensor Types for Precise Measurement
In a world increasingly driven by automation, robotics, and smart interaction, the ability for machines to perceive their environment accurately is fundamental. At the heart of this perception often lies a crucial capability: measuring distance. Whether it’s a robot arm assembling components with micron precision, an AGV navigating a warehouse floor, or your smartphone camera focusing instantly, distance sensors are the unsung heroes enabling these marvels. Understanding the diverse landscape of distance sensor types empowers engineers, designers, and enthusiasts to choose the optimal technology for their specific application.
Why Distance Sensing Matters: The Core of Spatial Awareness
Distance measurement transcends simple proximity detection. It provides quantitative spatial data essential for control, navigation, safety, and quality assurance. Distance sensors convert physical separation into usable electrical signals, acting as the electronic measuring tape for machines. The challenge? No single sensor type fits every scenario. Factors like range, accuracy, resolution, target material, environmental conditions, speed, and cost profoundly influence the best choice. This necessitates a clear understanding of the available distance sensor technologies.
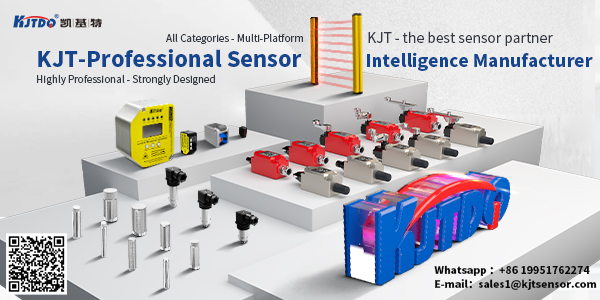
Navigating the Spectrum: Key Distance Sensor Technologies Explained
Here’s a breakdown of the most prominent distance sensor types, highlighting their working principles, strengths, and limitations:
- Ultrasonic Sensors: Sound Waves for Versatility
- How They Work: Emit high-frequency sound pulses and measure the time-of-flight (ToF) for the echo to return after bouncing off a target.
- Key Advantages:
- Cost-effective and widely available.
- Tolerant to target color, transparency, or surface finish (good for liquids, irregular surfaces).
- Robust in dusty or humid environments (non-optical).
- Moderate range capabilities (cm to several meters).
- Limitations:
- Accuracy and resolution are generally lower than optical methods.
- Slow measurement speed due to sound propagation limits.
- Sensitive to temperature changes (affects speed of sound).
- Narrow beam angles or large targets are needed for reliable detection; hard surfaces work best.
- Typical Uses: Tank level sensing, parking assistance, object detection in automation, simple robotics.
- Infrared (IR) / Time-of-Flight (ToF) Sensors: Light Speed Measurement
- How They Work (General Principle): Utilize infrared light. The Time-of-Flight (ToF) variant measures the time taken for a modulated light pulse to travel to the target and back, directly calculating distance.
- Key Advantages:
- Fast measurement speed due to light speed.
- Solid accuracy and resolution, especially modern ToF sensors.
- Compact size feasible.
- Resistant to ambient light (when using modulated IR).
- Limitations:
- Performance depends heavily on target surface properties. Dark, matte, or absorbing surfaces drastically reduce range and signal strength.
- Highly reflective or transparent surfaces can cause errors or missed detections.
- Sensitive to optical interference like dirt, fog, or strong ambient IR.
- Typical Uses: Proximity detection in devices, gesture recognition, simple obstacle avoidance, some mobile robotics, presence detection. (Modern ToF sensors offer enhanced capabilities).
- Laser Triangulation Sensors: Precision Focused Light
- How They Work: Project a visible or infrared laser spot onto the target. A position-sensitive detector (like a CCD or CMOS array) sees the spot from an offset angle. Distance is calculated based on the geometric triangulation principle – the position of the spot on the detector shifts as the target distance changes.
- Key Advantages:
- Exceptionally high accuracy and resolution over short to medium ranges.
- Excellent performance on most solid targets, regardless of color (within reason).
- Small, well-defined spot size enables precise point measurement.
- High measurement speed possible.
- Limitations:
- Cost is generally higher than ultrasonic or basic IR.
- Requires a relatively cooperative surface – transparent, shiny, or very dark surfaces can scatter or absorb the laser, causing errors.
- Dust, steam, or debris in the optical path can interfere.
- Range typically limited compared to LiDAR (cm to meters).
- Typical Uses: Industrial inspection (height, thickness, warp), precision assembly, displacement monitoring, 3D scanning components, robotics guidance.
- LiDAR (Light Detection and Ranging): Mapping the World in 3D
- How They Work: Essentially an advanced form of laser ToF. Emits rapid laser pulses (often infrared, sometimes visible) across a field of view (scanned or flash). Measures the Time-of-Flight for each pulse to return, building a detailed point cloud map of the surrounding environment.
- Key Advantages:
- Generates rich 3D spatial data (point clouds).
- Long range capabilities achievable (meters to kilometers).
- High angular resolution for detailed environmental mapping.
- Generally high accuracy.
- Limitations:
- High cost, especially for high-resolution units.
- Performance can suffer with adverse weather (heavy rain, fog, snow).
- Safety concerns with high-power lasers require careful handling.
- Data processing requirements are significant for point clouds.
- Typical Uses: Autonomous vehicles, aerial surveying, robotics navigation, high-definition mapping, forestry management, archaeology.
- Inductive & Capacitive Proximity Sensors: For Metal and More
- Inductive: Detect presence of metallic objects only. Generate an electromagnetic field; an approaching metal target induces eddy currents, changing the field and triggering detection. Does not provide analog distance measurement, just on/off presence within a specific range.
- Capacitive: Detect presence of any material that alters the sensor’s electrostatic field (including liquids, powders, plastics, wood). Measures the change in capacitance caused by the target entering the field. Primarily binary output (on/off), though some offer analog distance output with limitations.
- Key Advantages:
- Robust, sealed designs for harsh industrial environments.
- No moving parts, long lifespan.
- Fast response times.
- Capacitive sensors are material agnostic.
- Limitations:
- Inductive: Only work on metals; detection range is short and highly dependent on metal type and size.
- Capacitive: Detection range is very short and highly sensitive to environmental factors (moisture, humidity). Difficult to get consistent analog distance measurement.
- Typical Uses: Inductive: Position sensing of metal parts (machine tools, cylinders), counting metal objects. Capacitive: Liquid level detection, material presence detection on conveyors, non-metallic object detection.
Choosing Your Champion: Matching Sensor to Application
Selecting the right distance sensor type is critical for success. Start by defining your core requirements:
- What range do you need to measure? (Millimeters? Meters? Kilometers?)
- What level of accuracy and resolution is essential?
- What are the characteristics of your target? (Material, color, surface finish, size, reflectivity?)
- What is the operating environment? (Temperature, dust, moisture, vibration, ambient light?)
- What are your speed/sampling requirements?
- What is your budget?
For instance:
- Need cheap, robust presence detection in a dusty environment? Consider Ultrasonic.
- Require high precision on small features in a controlled setting?