variable reluctance sensor
- time:2025-03-28 02:50:38
- Нажмите:0
Variable Reluctance Sensors: The Unsung Heroes of Precision Measurement
In an era where automation and precision dominate industries, a small yet mighty device plays a critical role in ensuring machinery operates flawlessly: the variable reluctance sensor (VRS). From automotive engines to aerospace systems, these sensors silently monitor rotational speed, position, and vibrations, acting as the “eyes and ears” of modern engineering. But what makes them so indispensable? Let’s dive into the science, applications, and advantages of this underrated technology.
Understanding the Science Behind Variable Reluctance Sensors
At its core, a variable reluctance sensor operates on the principle of magnetic reluctance—a measure of how much a material opposes magnetic flux. The sensor consists of a coil-wrapped ferromagnetic core and a toothed or notched target wheel (typically made of steel). When the target wheel rotates, the air gap between the teeth and the sensor changes, altering the magnetic circuit’s reluctance.
This fluctuation generates a voltage in the coil through Faraday’s Law of Induction. The resulting waveform—a series of voltage spikes—correlates directly with the target’s speed or position. No external power source is required for the sensor to function, making it inherently robust and ideal for harsh environments.
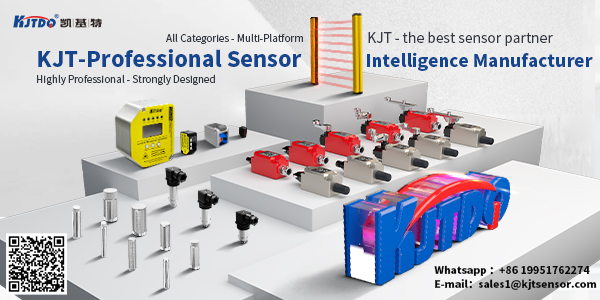
Key Applications: Where VRS Shines
- Автомобильная промышленность
Variable reluctance sensors are the backbone of crankshaft and camshaft position detection in internal combustion engines. By monitoring rotational speed, they ensure optimal ignition timing and fuel injection, directly impacting performance and emissions. For example, in anti-lock braking systems (ABS), VRS detects wheel speed to prevent skidding.
- Industrial Machinery
In manufacturing, these sensors monitor motor RPM, conveyor belt speeds, and turbine vibrations. Their ability to withstand extreme temperatures, dust, and moisture makes them perfect for heavy-duty equipment.
- Aerospace and Defense
From helicopter rotor speed measurement to aircraft landing gear alignment, VRS delivers reliability in mission-critical scenarios. Their fail-safe operation is vital for systems where downtime is not an option.
- Renewable Energy
Wind turbines rely on variable reluctance sensors to track blade rotation and generator health. By detecting imbalances early, they help prevent costly maintenance and extend equipment lifespan.
Advantages Over Competing Technologies
While Hall-effect sensors and optical encoders are popular alternatives, VRS holds unique benefits:
- Долговечность: With no moving parts or delicate electronics, these sensors thrive in dirty, high-vibration, or high-temperature environments.
- Эффективность затрат: Simplified design translates to lower production costs—a major advantage for large-scale industrial deployments.
- Zero Power Requirement: Unlike active sensors, VRS generates its own signal, reducing system complexity and energy consumption.
- High-Speed Capability: They excel in measuring rapid rotational changes, making them ideal for applications like turbocharger monitoring.
However, VRS isn’t without limitations. Its output signal strength depends on target speed—lower speeds yield weaker signals—and it struggles with very small air gaps. Engineers must carefully balance sensor placement and target geometry for optimal performance.
Choosing the Right Variable Reluctance Sensor
Selecting a VRS involves three critical considerations:
- Target Material and Geometry
The sensor’s output voltage depends on the target’s magnetic permeability. Ferromagnetic materials like iron or steel work best, while non-magnetic metals (e.g., aluminum) require additional modifications, such as embedded ferrous inserts.
- Operating Environment
For extreme conditions—such as underwater oil rigs or jet engines—look for sensors with IP67+ ratings, stainless steel housings, and high-temperature-resistant coatings.
- Signal Conditioning
Raw VRS signals are analog and often noisy. Pairing the sensor with a signal conditioner or microcontroller ensures clean, digitized output for modern control systems.
Innovations Driving VRS Forward
Recent advancements are expanding the sensor’s capabilities:
- Integrated Electronics: New models incorporate built-in amplification and filtering, reducing the need for external circuitry.
- Miniaturization: Compact VRS units now fit into tight spaces, such as medical robotics or drone motor assemblies.
- Smart Diagnostics: IoT-enabled sensors can predict failures by analyzing waveform patterns, aligning with Industry 4.0 trends.
Maintenance Tips for Longevity
To maximize a variable reluctance sensor’s lifespan:
- Regularly inspect for debris buildup around the target wheel.
- Ensure consistent air gaps (typically 0.5–2 mm) to avoid signal degradation.
- Use shielded cables to minimize electromagnetic interference in electrically noisy environments.
From keeping your car’s engine running smoothly to ensuring wind turbines generate clean energy efficiently, variable reluctance sensors prove that sometimes the most impactful technologies are the ones you never see. As industries push toward smarter, tougher, and more efficient systems, this decades-old innovation continues to evolve—proving its relevance in an increasingly digital world.