датчик нулевой скорости конвейера
- time:2025-03-28 02:46:16
- Нажмите:0
Zero Speed Sensors for Conveyors: Essential Protection for Modern Material Handling Systems
Imagine a bustling factory floor where conveyor belts hum with activity, transporting raw materials, packages, or industrial components. Now picture what happens when one of those conveyors suddenly stops—unnoticed. The result? Overloaded motors, jammed products, costly downtime, or even catastrophic equipment failure. This is where zero speed sensors for conveyors step in as unsung heroes, safeguarding operations by detecting unexpected halts and triggering instant corrective actions.
In today’s fast-paced industrial environments, ensuring conveyor reliability isn’t just about efficiency—it’s a matter of safety and profitability. Let’s explore how zero speed sensors work, why they’re indispensable, and how to choose the right one for your system.
What Is a Zero Speed Sensor, and How Does It Work?
А.zero speed sensor is an electromechanical or electronic device designed to monitor the rotational movement of conveyor belts, pulleys, or shafts. Its primary function is to detect when a conveyor stops moving—even if the motor is still running—and send a signal to the control system to halt operations or activate alarms.
Most zero speed sensors operate using one of two principles:
- Magnetic Proximity Sensing: A rotating gear or disc with embedded magnets passes by the sensor. Each rotation generates a pulse; if pulses cease, the sensor triggers an alert.
- Inductive or Optical Detection: Sensors measure the presence or absence of motion through changes in electromagnetic fields or light beams interrupted by rotating components.
These devices are often integrated with programmable logic controllers (PLCs) to automate responses, such as shutting down upstream equipment or activating backup systems.
Why Zero Speed Sensors Are Non-Negotiable for Conveyor Systems
Conveyors are the lifelines of industries like mining, agriculture, manufacturing, and logistics. A sudden stoppage can cascade into severe consequences:
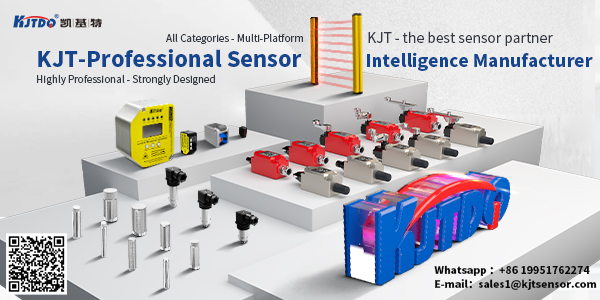
- Mechanical Damage: Overloaded rollers or misaligned belts due to blockages.
- Product Spillage: Uncontrolled stops lead to material buildup, increasing cleanup costs and safety risks.
- Downtime Costs: Idle labor, missed deadlines, and emergency repairs strain budgets.
- Safety Hazards: Stalled conveyors near heat sources or in hazardous environments may pose fire or chemical exposure risks.
By installing a zero speed sensor, operators gain real-time visibility into conveyor health, enabling proactive maintenance and minimizing operational risks. For example, in coal-handling plants, these sensors prevent belt slippage that could ignite combustible materials.
Key Applications of Zero Speed Sensors
While their core function is universal, zero speed sensors adapt to diverse industrial scenarios:
- Mining and Bulk Material Handling: Detecting belt slippage or breaks in high-load environments.
- Food and Beverage Production: Ensuring hygienic processing by preventing product jams in washdown-safe sensors.
- Packaging Lines: Avoiding misaligned labels or crushed boxes caused by uneven conveyor speeds.
- Airport Baggage Systems: Reducing luggage mishandling by monitoring belt continuity.
In each case, the sensor acts as a fail-safe mechanism, bridging the gap between mechanical performance and automated control.
Choosing the Right Zero Speed Sensor: 5 Factors to Consider
Not all sensors are created equal. Selecting the ideal device requires evaluating your system’s unique demands:
- Environmental Conditions: Dust, moisture, temperature extremes, or explosive atmospheres dictate whether you need ruggedized, IP67-rated, or intrinsically safe models.
- Output Signal Type: Match the sensor’s output (e.g., NPN, PNP, or relay contacts) to your PLC’s input requirements.
- Mounting Flexibility: Adjustable brackets or modular designs simplify installation on cramped or complex conveyor frames.
- Adjustable Sensitivity: Sensors with tunable detection thresholds accommodate varying conveyor speeds.
- Полученные сертификаты: Look for industry-specific approvals (ATEX, ISO, FDA) to meet compliance standards.
For instance, in a flour mill prone to dust explosions, a zero speed sensor with ATEX certification and stainless steel housing would be non-negotiable.
Installation and Maintenance Best Practices
Even the best sensor underperforms if poorly installed. Follow these guidelines:
- Positioning: Mount the sensor close to the monitored shaft or pulley for accurate detection. Avoid vibration-prone areas.
- Alignment: Ensure the sensing element (e.g., magnet or gear) rotates within the sensor’s detection range.
- Testing: Simulate a stoppage during commissioning to verify alarm triggers and system response times.
- Routine Checks: Clean lenses or sensing surfaces regularly; inspect wiring for wear in high-vibration zones.
Pro tip: Pair zero speed sensors with predictive maintenance software to track performance trends and preempt failures.
The Future of Zero Speed Sensing
As Industry 4.0 reshapes manufacturing, zero speed sensors are evolving beyond basic motion detection. Smart sensors now integrate with IoT platforms, providing data on vibration patterns, temperature fluctuations, and energy consumption. This shift enables predictive analytics, where sensors not only alert to stoppages but also forecast wear-and-tear issues before they escalate.
For example, a sensor embedded with AI algorithms could analyze rotational inconsistencies to predict bearing failures, transforming conveyor maintenance from reactive to proactive.
From preventing downtime to enhancing worker safety, zero speed sensors for conveyors are no longer optional—they’re a cornerstone of resilient industrial operations. By understanding their role, selecting the right technology, and adhering to best practices, businesses can turn potential disasters into manageable incidents, keeping their workflows