keyence lr x50
- time:2025-03-09 04:07:37
- Нажмите:0
Keyence LR-X50: The Next Frontier in High-Speed Precision Measurement
In an era where manufacturing efficiency and accuracy are non-negotiable, the Keyence LR-X50 emerges as a game-changer. Imagine a device capable of detecting microscopic defects on a production line in real time or measuring ultra-fine components with zero margin for error—this is where the LR-X50 shines. Combining cutting-edge laser technology with unmatched versatility, this sensor is redefining quality control across industries. But what makes it stand out in a crowded market of measurement tools? Let’s dive deeper.
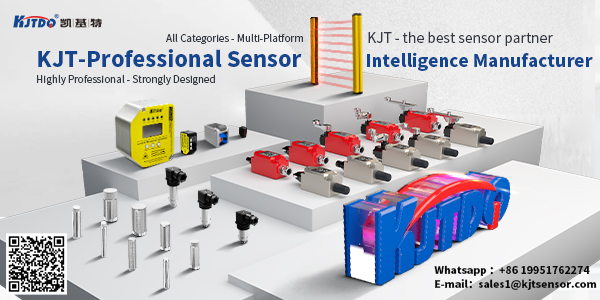
The Science Behind the Keyence LR-X50
At its core, the LR-X50 is a high-speed laser displacement sensor designed for precision measurement tasks. Unlike traditional contact-based sensors, it employs a non-contact method using laser triangulation. This means it can measure objects without physical interaction, eliminating risks of damage to delicate surfaces—a critical advantage in industries like semiconductor manufacturing or medical device production.
The sensor boasts a 50 kHz high-speed sampling rate, enabling it to capture data points at lightning speed. For context, this allows it to detect variations as small as 0.1 µm (micrometers) on objects moving at high velocities. Whether it’s inspecting automotive parts for micro-cracks or ensuring the thickness uniformity of battery electrodes, the LR-X50 delivers results with submicron-level accuracy.
Why Industries Are Switching to the LR-X50
- Adaptability in Harsh Environments
Industrial settings often involve dust, vibrations, or temperature fluctuations. The LR-X50 is built with IP67-rated durability, ensuring reliable performance even in challenging conditions. Its robust housing and advanced noise-reduction algorithms make it ideal for automotive assembly lines or metalworking facilities.
- User-Friendly Integration
One standout feature is its plug-and-play compatibility with existing systems. The sensor’s intuitive software allows engineers to configure measurement parameters in minutes. With real-time waveform monitoring and automatic calibration, downtime is minimized—a key factor for high-volume production environments.
- Cost-Efficiency Through Precision
Defects in manufacturing can lead to massive financial losses. By catching errors early, the LR-X50 reduces waste and rework. For example, in electronics manufacturing, it ensures components like circuit boards meet exact specifications, preventing costly recalls.
Real-World Applications of the LR-X50
- Автомобильная промышленность: Ensuring piston ring thickness uniformity or detecting warping in brake discs.
- Pharmaceuticals: Verifying tablet coating consistency to comply with strict regulatory standards.
- Renewable Energy: Measuring solar cell layers for optimal energy efficiency.
A case study from a leading EV battery producer highlights the sensor’s impact: After integrating the LR-X50, defect rates dropped by 34% within three months, thanks to its ability to detect anode coating irregularities invisible to the human eye.
Keyence LR-X50 vs. Compes: What Sets It Apart?
While brands like Omron or Panasonic offer similar sensors, the LR-X50 excels in three areas:
- Speed: Compes average 10–20 kHz sampling rates; the LR-X50 operates at 50 kHz.
- Многогранный.: Its adjustable focus and 12-mm measurement range accommodate diverse object sizes.
- Software Intelligence: Built-in algorithms automatically filter environmental noise, a feature rarely matched by rivals.
The Future of Precision Measurement
As industries push toward miniaturization and smarter automation, tools like the Keyence LR-X50 are becoming indispensable. Its ability to combine speed, accuracy, and resilience positions it as a cornerstone of Industry 4.0. For engineers and quality assurance teams, adopting this technology isn’t just an upgrade—it’s a strategic move to stay ahead in a competitive global market.
Whether you’re optimizing a production line or pioneering next-gen products, the LR-X50 offers a measurable edge. After all, in the quest for perfection, every micron counts.