laser gauge measurement
- time:2025-03-04 12:12:00
- Нажмите:0
Laser Gauge Measurement: The Future of Precision in Industrial Applications
Imagine a manufacturing floor where components are measured with accuracy down to a micrometer—without physical contact, without human error, and in real time. This isn’t science fiction; it’s the reality enabled by laser gauge measurement. As industries push for tighter tolerances and higher efficiency, this technology has emerged as a cornerstone of modern precision engineering. But what makes laser gauging so revolutionary, and how is it transforming sectors from aerospace to consumer electronics? Let’s dive in.
The Science Behind Laser Gauge Measurement
At its core, laser gauge measurement relies on the principles of light interference and reflection. A laser beam is directed toward a target surface, and sensors detect changes in the beam’s properties—such as wavelength, phase, or intensity—caused by the surface’s position, texture, or movement. Unlike traditional mechanical gauges, which require physical contact, laser systems operate non-invasively, eliminating wear and tear while capturing data at lightning speeds.
One standout feature is its ability to measure sub-micron displacements. For instance, in semiconductor manufacturing, even a nanometer-level deviation can render a microchip useless. Laser gauges provide the precision needed to detect such minute variations, ensuring quality control at unprecedented levels.
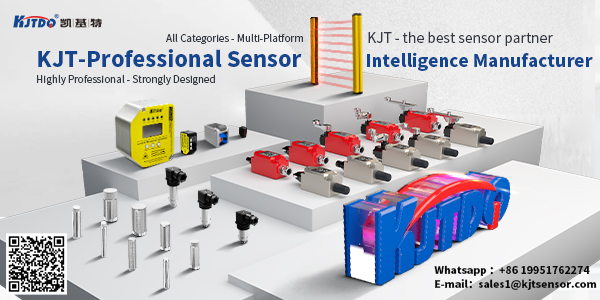
Key Applications Across Industries
Laser gauge measurement isn’t limited to niche applications—it’s a versatile tool driving innovation globally. Below are sectors where its impact is most pronounced:
- Производство автомобилей
From engine components to body panels, automotive parts demand exact specifications. Laser gauges monitor thickness, alignment, and surface defects during production. For example, Tesla’s Gigafactories use laser systems to inspect battery cell dimensions, ensuring consistency across millions of units.
- Aerospace and Defense
Aircraft turbines and satellite components operate under extreme conditions. Here, laser measurement validates part geometries and detects micro-cracks invisible to the human eye. Boeing and Airbus have integrated these systems to reduce assembly errors by over 30%.
- Потребительская электроника
Smartphone screens, circuit boards, and camera modules require flawless surfaces. Apple’s suppliers employ laser gauges to verify screen flatness within 0.1 microns—critical for touch sensitivity and display clarity.
- Medical Device Production
Surgical instruments and implants rely on biocompatible materials with precise dimensions. Laser systems ensure compliance with stringent regulatory standards, minimizing risks in life-critical applications.
Advantages Over Traditional Measurement Methods
Why are industries rapidly adopting laser gauging? Let’s compare it to conventional tools like calipers or coordinate measuring machines (CMMs):
- Non-Contact Operation: Physical probes can scratch delicate surfaces or deform flexible materials. Lasers eliminate this risk, making them ideal for measuring soft polymers or high-temperature components.
- Speed and Efficiency: A single laser scan can capture thousands of data points in seconds, whereas manual measurements take hours. This accelerates production cycles and reduces downtime.
- Adaptability: Laser systems can be integrated into robotic arms or conveyor belts for real-time monitoring. For example, in food packaging, they verify seal integrity on moving production lines.
- Data Accuracy: Human error and instrument calibration drift are minimized. Advanced algorithms process raw data into actionable insights, enabling predictive maintenance and process optimization.
Overcoming Challenges in Laser Gauging
While laser measurement offers unparalleled benefits, it isn’t without limitations. Environmental factors like ambient light, vibrations, or dust can interfere with readings. However, innovators are addressing these issues:
- Shielding Technologies: Enclosures and filters block external light sources, ensuring signal clarity.
- AI-Powered Calibration: Machine learning models compensate for environmental noise, enhancing reliability in harsh conditions.
- Multi-Sensor Fusion: Combining laser data with thermal or ultrasonic measurements provides a holistic view of complex assemblies.
The Future of Laser Gauge Measurement
As Industry 4.0 gains momentum, laser gauging is evolving beyond standalone tools. Here’s what’s on the horizon:
- Smart Factories: Integrated with IoT platforms, laser systems will feed data directly to cloud-based analytics engines, enabling autonomous quality control.
- Miniaturization: Portable laser gauges are shrinking in size while expanding in capability. Field technicians can now perform lab-grade measurements on-site.
- Sustainability: By reducing material waste and energy consumption, laser-driven precision aligns with global ESG goals. For instance, optimizing metal cutting processes saves tons of raw material annually.
From microfabrication to mega-infrastructure projects, laser gauge measurement is redefining what’s possible in precision engineering. Its blend of speed, accuracy, and versatility makes it indispensable for industries striving to stay competitive in an era of escalating quality demands. As technology advances, one thing is clear: the laser’s role in measurement isn’t just a trend—it’s the new standard.