Промышленный лазерный датчик расстояния
- time:2025-03-04 10:05:14
- Нажмите:0
Industrial Laser Distance Sensors: The Precision Powerhouse Transforming Modern Manufacturing
Imagine a world where machines operate with micron-level accuracy, robotic arms weld car frames without human intervention, and quality control happens in real-time at blinding speeds. This isn’t science fiction—it’s the reality enabled by industrial laser distance sensors, the unsung heroes of modern automation. From automotive assembly lines to aerospace manufacturing, these cutting-edge devices are redefining efficiency, safety, and precision in industrial settings.
What Are Industrial Laser Distance Sensors?
At their core, industrial laser distance sensors are non-contact measurement devices that use laser technology to determine the distance between the sensor and a target object. By emitting a laser beam and analyzing the reflected light—whether through time-of-flight (ToF), triangulation, or phase-shift methods—these sensors deliver real-time data with exceptional accuracy. Unlike traditional mechanical measuring tools, they eliminate physical wear, reduce human error, and thrive in harsh environments where dust, vibrations, or extreme temperatures would cripple conventional systems.
Why Laser Distance Sensors Are Dominating Industry 4.0
The rise of smart factories and Industry 4.0 has created an insatiable demand for precision and automation. Here’s why laser sensors are leading the charge:
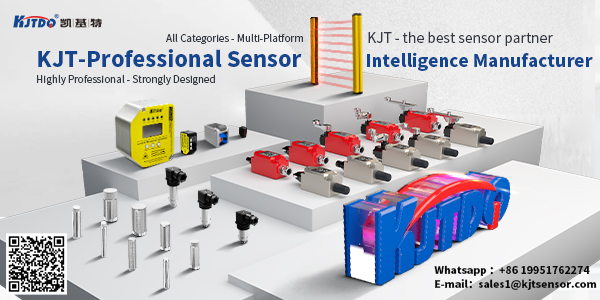
- Unmatched Precision: Capable of measuring distances down to micrometers (µm), these sensors ensure components fit perfectly in assemblies, reducing waste and rework. For example, in semiconductor manufacturing, even a 1µm deviation can render a microchip useless.
- Speed and Real-Time Feedback: Laser sensors operate at kHz frequencies, enabling high-speed inspections on conveyor belts or robotic arms. In automotive welding, they adjust robot trajectories milliseconds before contact, preventing costly collisions.
- Многогранный.: Whether measuring transparent glass, reflective metals, or uneven surfaces, advanced models adapt using multi-echo technology or wavelength adjustments.
- Долговечность: Encased in ruggedized housings, they withstand IP67-rated conditions—think foundries with 1,000°C ambient temperatures or offshore oil rigs battered by saltwater.
A 2023 report by Fortune Business Insights predicts the laser sensor market will grow at a CAGR of 8.2% through 2030, driven largely by automotive and electronics sectors.
Key Applications Redefining Industries
Industrial laser distance sensors aren’t just niche tools—they’re transformative across sectors:
- Производство автомобилей: From aligning robotic paint sprayers to ensuring brake discs meet thickness tolerances, lasers ensure every Audi or Tesla rolls off the line flawlessly. BMW recently credited laser-guided systems for cutting assembly errors by 37%.
- Аэрокосмическая промышленность: Airbus uses laser sensors to inspect turbine blade coatings, where a 10µm variation can impact fuel efficiency by 2%.
- Pharmaceuticals: In vial filling lines, sensors verify liquid levels at 200 bottles/minute, complying with FDA mandates for dosage accuracy.
- Логистика: Amazon’s warehouses deploy laser-aided LiDAR systems to map pallet dimensions instantly, optimizing storage space.
Overcoming Challenges: Noise, Surface Variability, and Cost
While revolutionary, laser sensors aren’t without hurdles. Engineers often grapple with:
- Optical Interference: Ambient light or stray reflections can distort readings. Solutions like polarized filters or narrow-band lasers mitigate this.
- Complex Surfaces: Measuring translucent materials (e.g., plastic films) requires sensors with adjustable sensitivity or dual-wavelength beams.
- Initial Costs: High-end models can exceed $5,000, but ROI is swift. A case study by Sick AG showed a sensor paying for itself in 6 months by reducing scrap rates in steel coil production.
The Future: AI Integration and Miniaturization
The next frontier for laser sensors lies in edge computing and AI. Sensors equipped with onboard processors now analyze data locally, slashing latency. For instance, Keyence’s LK-G5000 series uses machine learning to ignore irrelevant background noise, boosting reliability in cluttered environments.
Meanwhile, miniaturization is opening new applications. Researchers at MIT recently unveiled a chip-sized laser sensor for micro-robot navigation, hinting at future uses in medical devices or nanoscale manufacturing.
Choosing the Right Sensor: A Quick Guide
Selecting a laser distance sensor hinges on three factors:
- Range and Resolution: Short-range (0.1–10m) sensors suit precision tasks, while long-range models (up to 300m) monitor large-scale infrastructure.
- Environmental Factors: Opt for IP67/IP69K ratings for wet/dusty settings or explosion-proof certifications for hazardous areas.
- Output Options: Analog (4–20mA) outputs integrate with PLCs, while Ethernet/IP or IO-Link enable Industry 4.0 connectivity.
Brands like Leuze, Banner Engineering, and Omron offer configurable solutions, but always validate specs with real-world testing.
From boosting production yields to enabling fully autonomous factories, industrial laser distance sensors are more than tools—they’re the bedrock of tomorrow’s manufacturing landscape. As industries push for finer tolerances and faster cycles, these sensors will remain indispensable, proving that sometimes, the smallest beam of light can cast the longest shadow.