Диапазон измерения фотоэлектрического датчика
- time:2025-07-25 04:20:23
- Нажмите:0
Demystifying Photoelectric Sensor Range: Factors and Selection Guide
Ever installed a photoelectric sensor only to find it doesn’t quite “see” the object where you need it to? Or wondered why one sensor claims a 10-meter range while another similar-looking one manages only 2? The operating range is arguably one of the most critical specifications for photoelectric sensors, directly impacting application success. Understanding what influences it and how to choose wisely is essential.
What Exactly is “Range”?
In the realm of photoelectric sensors, “range” refers to the maximum reliable operating distance or sensing distance at which the sensor can consistently detect a specified target under defined conditions. It’s not simply a theoretical maximum; it’s a practical specification tied to performance guarantees. Crucially, range specifications are always defined for a standard target – typically a matte white surface (like Kodak 90% white card) of a specific size. Actual range in your application will vary based on the target’s properties and environmental factors.
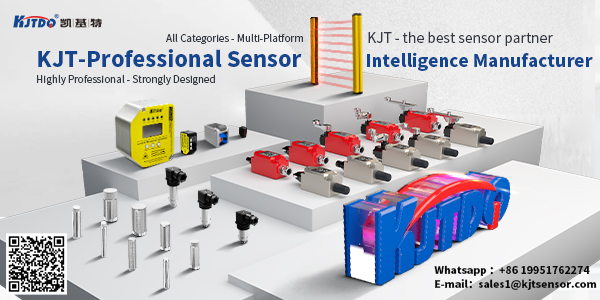
The Four Pillars Influencing Photoelectric Sensor Range
A sensor’s achievable range isn’t magic; it’s governed by physics and design. Four key factors interplay:
- Sensor Type & Operating Principle: This is fundamental.
- Through-Beam Sensors: Offering the longest possible ranges (easily 10m, 20m, 50m+), these separate emitter and receiver units create an uninterrupted beam. Detection occurs when an object blocks this beam. The range is primarily limited by the emitter’s output power and the receiver’s sensitivity.
- Retroreflective Sensors: Combining emitter and receiver in one housing, these detect objects that interrupt the beam reflected back from a specialized reflector. Range is significant but generally less than through-beam (commonly 0.1m up to 10m or even 15m for high-end models), limited by the round-trip light path and reflector efficiency.
- Diffuse (Proximity) Sensors: The most common, self-contained type. They detect light reflected directly off the target object itself. Range is the shortest among the primary types, typically ranging from a few millimeters up to around 2 meters, with most common models under 300mm. Range is heavily dependent on target size, color, and surface finish, and also affected by the background.
- Background Suppression (BGS) & Fixed Field (Fixed Focus): Advanced diffuse types use triangulation or focused optics to detect objects only within a defined, narrow distance band. While their absolute maximum range might be similar to standard diffuse (e.g., 50-300mm), their effective sensing range is precisely controlled within that span, ignoring objects outside this “window”. This enhances accuracy for specific tasks.
- Light Source: The wavelength and intensity of the emitted light dictate performance.
- Infrared (IR): The most common light source. IR is invisible to humans, resistant to ambient visible light interference, and generally provides the best range and energy efficiency, especially for through-beam and retroreflective sensors.
- Red LED: Visible light source offering easier beam alignment and confirmation. Generally provides shorter range than IR but sufficient for many diffuse applications. Ideal where visual beam location is helpful.
- Laser: Generates a highly focused, intense beam. Provides the longest ranges, smallest spot size, and highest precision, especially crucial for detecting tiny objects (minimum detectable object) or applications needing long-range precision (e.g., laser through-beam for 50m+). More susceptible to dust/dirt contamination on the lens than LEDs.
- Target Characteristics: Remember the “standard target” caveat? Real-world targets differ:
- Size: Larger targets reflect more light, increasing the effective sensing distance. A sensor calibrated for a 100mm white card might struggle to detect a 5mm black screw at the same distance. The minimum detectable object specification is vital for small targets.
- Color & Reflectivity: Matte white (high reflectivity) provides the best range. Dark colors (low reflectivity), black especially, absorb light, drastically reducing range. Shiny or mirror-like surfaces can unpredictably reflect light away from the sensor’s receiver. Transparent targets (glass, clear plastic) are notoriously challenging unless using specialized sensors.
- Surface Finish: Smooth, glossy surfaces reflect light directionally (like a mirror), while matte, rough surfaces scatter light diffusely. Diffuse sensors work best with matte finishes. Glossy targets can reflect light unpredictably, potentially causing missed detections or false triggers.
- Environmental Conditions: The real world is messy:
- Ambient Light: Strong sunlight or bright artificial light can swamp the sensor’s receiver, especially with visible red LEDs. IR sensors offer better resistance. Sunlight immunity is a key specification for outdoor or bright indoor applications. Optical filters in the receiver help reject unwanted wavelengths.
- Contaminants: Dust, fog, smoke, and dirt particles scatter and attenuate the light beam, reducing effective range. Regular cleaning may be necessary. Some sensors offer air purge fittings or special coatings. Condensation on lenses can also block light.
- Temperature: Extreme cold or heat can affect the light source output (LED efficiency drops as temperature rises) and electronic components. Ensure the sensor’s operating temperature range suits the environment.
- Electrical Noise: While not directly reducing optical range, strong electromagnetic interference near high-power motors or VFDs can cause erratic sensor behavior or reduced effective range consistency.
Choosing the Right Range for Your Application: Key Considerations
Selecting a sensor isn’t just about picking the longest range spec you see. Focus on practical application needs:
- Define the Required Sensing Distance: Measure accurately. How far must the sensor reliably detect the object? Add a reasonable safety margin (e.g., 20-50%). Don’t overspecify unnecessarily, as other factors (like target properties) might force a different choice anyway.
- Analyze the Target: Be specific. What is its size, color, material, and surface finish? Is it consistent? For challenging targets (dark, small, shiny, transparent), sensor selection becomes even more critical. Consult sensor datasheets for performance curves relative to target size/reflectivity.
- Assess the Environment: Honestly evaluate ambient light levels, potential contaminants (dust, mist, oil), temperature extremes, and sources of electrical noise. Match sensor IP ratings (ingress protection) and specifications (like sunlight immunity) to these conditions.
- Prioritize Practicality & Cost: While a laser through-beam might offer the ultimate range and precision, it requires careful alignment and is more expensive than a simple diffuse sensor. Can a retroreflective sensor provide sufficient range and accuracy more simply? Could a longer-range diffuse sensor eliminate the need for a separate reflector? Evaluate installation complexity and maintenance needs.
- Consult Datasheets Critically: Look beyond the headline range figure. What was the standard target size and reflectivity? Are there graphs showing range vs. target size/reflectivity? What are the Рабочая температура limits? Is sunlight immunity specified? Understanding the test conditions behind the range spec is vital for predicting real-world performance.
Beyond Maximum Range: Consistency and Stability
While knowing the maximum range is important, equally crucial is the sensor’s ability to detect consistently within its operating range despite variations in target properties, temperature, and supply voltage. High-quality sensors incorporate features like constant current regulation for the LED and sophisticated receiver circuits with automatic gain control (AGC) to maintain stable sensing characteristics across their specified operating envelope. This stability ensures reliable detection over time and varying conditions, preventing costly false triggers or missed detections. Consistent performance is often more valuable than sheer maximum distance.
Selecting the optimal photoelectric sensor hinges on a clear understanding of the critical factors impacting its operating range. By carefully considering the application’s sensing distance needs, target properties,