Фотоэлектрический датчик цвета
- time:2025-07-25 02:43:22
- Нажмите:0
Photoelectric Color Sensors: The Eyes of Modern Industry
Imagine a world where machines flawlessly distinguish a ripe tomato from an unripe one, spot microscopic defects on a circuit board moving at blinding speed, or ensure every component in your car is perfectly painted. This isn’t science fiction; it’s the daily reality powered by photoelectric color sensors. These sophisticated devices act as the critical vision system within countless automated processes, translating the complexities of color into precise, actionable data.
Beyond Simple Detection: The Color Perception Challenge
While traditional photoelectric sensors excel at detecting presence or absence, or differentiating brightness levels, they fall short when the task demands recognizing specific hues. That’s where photoelectric color sensors shine. They don’t just see light intensity; they analyze its spectral composition, enabling machines to make decisions based on color – a capability fundamental to quality, efficiency, and brand consistency across numerous sectors.
How They See Color: Under the Hood
The core principle revolves around light analysis. A typical Фотоэлектрический датчик цвета features:
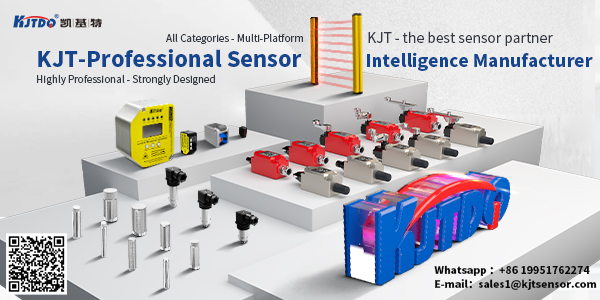
- Integrated Light Source: Most incorporate LEDs, often emitting red, green, and blue (RGB) light sequentially or sometimes broad-spectrum white light. Some advanced models offer specific spectral outputs.
- Light Interaction: The emitted light strikes the target object. Different pigments and surface properties cause specific wavelengths to be absorbed and others reflected.
- Specialized Receiver: Instead of a simple photodetector measuring total reflected intensity, a color sensor uses either:
- Multiple Photodiodes with Color Filters: Individual photodiodes are precisely covered with red, green, and blue filters, allowing them to measure the intensity of light in each specific color band independently.
- A True Spectral Sensor (Less Common): More sophisticated sensors might use a spectrometer element to analyze the full spectrum of reflected light.
- Processing Unit: The sensor’s internal logic analyzes the ratio of the intensities received from the red ®, green (G), and blue (B) channels. This RGB data is then transformed into a standardized color space like HSV (Hue, Saturation, Value) or *L*ab. The crucial parameter for color recognition is usually the Hue component.
The Language of Color: Setting Standards
The true power lies in how the sensor uses this color information. During setup, an operator teaches the sensor by presenting it with a sample of the desired “good” color. The sensor captures the reflected light ratios or the calculated hue value. Sophisticated algorithms allow setting tolerance ranges around this target value. The sensor’s output (e.g., discrete On/Off signal, analog value, digital data via IO-Link) then signals whether the detected color falls within this acceptable tolerance band or deviates, triggering downstream actions.
Where Color Vision is Mission-Critical: Key Applications
The ability to reliably detect and sort based on color makes these sensors indispensable across industries:
- Manufacturing & Assembly: Verifying correct parts placement by color-coded components, detecting color-coded labels or markings, ensuring painted parts meet exact color specifications (critical for automotive, aerospace), sorting colored caps onto bottles, identifying wires by insulation color.
- Packaging & Printing: Inspecting print quality and color registration on labels, cartons, and flexible packaging to prevent costly misprints. Verifying correct label application on specific product variants distinguished by color.
- Food & Beverage Processing: Sorting produce by ripeness (tomatoes, apples, potatoes), detecting foreign material based on color difference (e.g., green plastic in peas), confirming correct cap or closure color on beverages.
- Pharmaceuticals: Ensuring correct pill color for identification and quality control, verifying tamper-evident seals and colored packaging elements.
- Recycling: Automated sorting of plastics or glass based on color streams to improve purity and efficiency in recycling facilities.
- Textiles & Apparel: Sorting fabrics or garments by color, verifying thread or dye consistency.
Why Choose a Photoelectric Color Sensor? Key Advantages
Compared to manual inspection or less capable sensors, photoelectric color sensors offer significant benefits:
- Unmatched Speed and Consistency: They operate at machine speeds, performing thousands of reliable color checks per minute without fatigue, crucial for high-volume production lines.
- Objective Quality Control: Removes human subjectivity from color judgments, ensuring consistent adherence to brand and quality standards.
- Enhanced Efficiency: Automates sorting and inspection tasks, reducing labor costs, minimizing waste from errors, and increasing overall production throughput.
- Robust Performance: Modern sensors are designed for harsh industrial environments, resistant to dust, vibration, and varying ambient light conditions, though careful setup is still required.
- Flexibility: Capable of being rapidly reprogrammed (often via simple teach-in buttons or software) for different products or color targets.
Choosing the Right Vision Partner: Critical Selection Factors
Selecting the optimal Фотоэлектрический датчик цвета requires careful consideration:
- Required Color Discrimination: How subtle are the color differences you need to detect? Higher precision demands more sophisticated sensors.
- Target Surface Properties: Matte, glossy, textured, transparent, or metallic surfaces reflect light very differently. Test the sensor on actual samples.
- Operating Distance & Spot Size: The sensor must physically reach the target area with an appropriate beam spot size.
- Speed & Response Time: Must match the line speed for reliable detection.
- Environmental Conditions: Temperature, dust, humidity, potential contaminants, and ambient light interference.
- Output Requirements: Simple discrete output, analog signal proportional to color deviation, or digital communication (like IO-Link) for richer data and remote configuration?
- Mounting Constraints: Physical size and mounting options must fit the application space.
The Future is Colorful
As automation continues its relentless advance, the demand for precise, robust, and intelligent sensing grows. Photoelectric color sensors have evolved from niche devices to fundamental components driving quality and efficiency in modern manufacturing and processing. By giving machines the critical sense of sight to interpret color, these sensors perform vital roles, ensuring the products we rely on meet the highest standards of consistency and performance every single time.