through beam type sensor
- time:2025-07-25 01:57:21
- Нажмите:0
Through Beam Sensors: Precision Detection Over Extended Distances Demystified
Ever struggled to detect objects reliably over long distances, through challenging environments, or with transparent or highly reflective targets? In the demanding world of industrial automation and safety, achieving consistent, fail-safe detection is paramount. This is where the robust and fundamentally simple Фотоэлектрический датчик с проникающим лучом shines. Offering unparalleled range and reliability in specific applications, understanding its workings and ideal use cases is crucial for optimizing sensing solutions. This article delves into the core principles, advantages, limitations, and strategic applications of the indispensable through beam sensor.
Understanding the Fundamental Principle
At its heart, a through beam sensor operates on a straightforward but powerful concept: separation. Unlike other photoelectric sensor types (diffuse or retro-reflective) that combine emitter and receiver in a single housing, the through beam configuration consists of two distinct, separate units:
- The Transmitter (Emitter): This unit houses a focused light source, typically an infrared LED or laser diode, which emits a constant beam of light directed precisely towards the receiver.
- The Receiver: Positioned directly opposite the transmitter, this unit houses a photosensitive element designed to detect the specific light beam emitted by its paired transmitter.
The core operating principle hinges on this uninterrupted light path. The receiver’s output signal state (typically switching between ON and OFF) depends entirely on whether the light beam reaches it:
- Beam Unbroken: When the path is clear, the receiver detects the light beam and outputs a specific signal (e.g., HIGH or ON).
- Beam Broken: The instant an object interrupts the beam’s path, the receiver stops detecting the light and immediately changes its output signal state (e.g., LOW or OFF).
This direct “beam present/beam absent” detection logic makes through beam sensors incredibly reliable and immune to most variations in the target object’s color, surface finish, or material – as long as the object is sufficiently opaque to block the light beam.
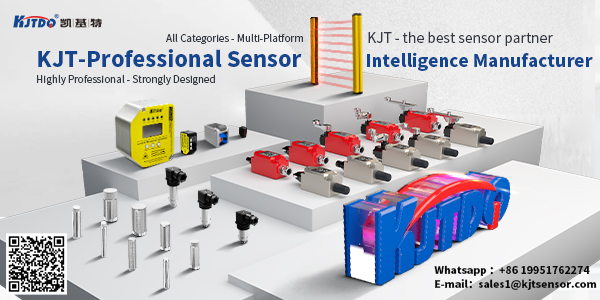
Unlocking the Key Advantages
The distinct physical separation of emitter and receiver unlocks several significant advantages, making through beam sensors the gold standard for specific demanding scenarios:
- Longest Sensing Ranges: Among all photoelectric sensor types, through beam sensors consistently achieve the greatest possible detection distances. Ranges can easily extend from several meters up to 30 meters (100 feet) or even more in specialized models. This makes them ideal for monitoring large machines, conveyor spans, warehouse bays, or vehicle entry/exit points.
- Highest Detection Reliability & Immunity: Because detection relies solely on beam interruption, these sensors are largely unaffected by:
- Target Characteristics: Surface color, reflectivity, texture, or material (wood, metal, plastic, glass) have minimal impact, provided the target is opaque enough to block the beam. This makes them excellent for detecting transparent objects like glass bottles or clear films, which often confound other sensor types.
- Environmental Factors: They generally offer better resistance to ambient light interference, dust (unless coating the lenses heavily), and minor misalignment issues compared to diffuse sensors, although alignment is still critical.
- False Triggering: The distinct beam interruption signal is clear-cut, minimizing the risk of false triggers caused by stray reflections or background objects – a common challenge with diffuse sensors.
- Fast Response Times: The on/off nature of the beam break detection allows for extremely fast switching speeds. This capability is essential for high-speed counting applications, precise position verification on rapidly moving production lines, or triggering safety light curtains.
- Consistent Operation: Performance remains stable regardless of the object’s distance from the sensor pair, as long as the beam is broken. There’s no “minimum sensing distance” limitation inherent to diffuse sensors.
Acknowledging the Limitations: Alignment is Paramount
Despite their impressive strengths, through beam sensors have specific considerations:
- Critical Alignment: The most significant challenge is ensuring precise alignment between the transmitter and receiver. Any misalignment, vibration causing drift, or movement of the mounting structure can disrupt the beam path, leading to false beam-break signals (nuisance trips) or failure to detect. Careful installation and robust mounting are essential. Laser alignment tools built into some models significantly aid setup.
- Cabling Complexity: Requiring two separate housings means needing two cables and power supplies (though often the receiver can be powered via the connection to the control system). This increases installation time, cost, and potential points of failure compared to single-housing sensors.
- Physical Obstruction Potential: The physical space between the emitter and receiver must be kept clear. Unauthorized access, accumulated debris, or inadvertently placed objects can block the beam and cause false triggers.
- Higher Initial Cost: While highly cost-effective for their intended applications, the need for two units typically makes the initial hardware cost higher than a single diffuse or retro-reflective sensor.
Where Through Beam Sensors Truly Excel
Understanding their strengths and weaknesses dictates their ideal deployment:
- Long-Range Object Detection: Detecting objects, vehicles, or personnel over expansive distances (e.g., conveyor systems spanning large facilities, parking garage entrances, warehouse doorways).
- Detection of Transparent/Shiny Objects: Consistently sensing clear bottles, glass panels, plastic films, or highly reflective metals that defy reliable detection by diffuse sensors.
- High-Speed Counting & Verification: Accurately counting small, fast-moving items on conveyor belts (pills, caps, small components) or verifying the presence/absence of objects at high line speeds.
- Position & Registration Control: Verifying the precise arrival position of objects at a work station or ensuring correct registration on web processes (paper, film, textiles).
- Safety Applications: Forming the basis of safety light curtains (where multiple beams create a detection zone) and perimeter guarding systems where any beam break signals an intrusion.
- Harsh Environments: Selected models with rugged housings (IP67/IP69K) and/or modulated light can operate reliably in dusty, steamy, or outdoor conditions where other sensors might falter.
Selecting and Implementing Effectively
When considering a through beam type sensor, deliberate on these factors:
- Required Sensing Range: Match the sensor’s specification to your maximum distance requirement with a safety margin.
- Target Characteristics: Confirm opacity. If detecting liquids or very thin films, verify the beam wavelength’s absorption characteristics.
- Environmental Conditions: Assess dust, moisture, temperature extremes, and vibration levels. Choose appropriate IP ratings and mechanical resilience.
- Beam Type: Standard (visible or invisible IR) vs. Laser (tighter beam, longer range, easier alignment).
- Mounting Stability: Ensure the mounting locations for both units are rigid and protected from vibration or accidental impact.
- Alignment Aids: Prioritize models with visual indicators (LEDs showing alignment status) or built-in laser pointers for vastly simplified setup.
- Output Type: Ensure compatibility (PNP/NPN, Analog, IO-Link) with your control system.
The Фотоэлектрический датчик с проникающим лучом remains an indispensable tool in the automation engineer’s arsenal. Its unparalleled combination of extended range, immunity to challenging target surfaces, and inherent reliability for detecting opaque objects makes it the optimal choice for countless applications where other sensor types fall short. While demanding careful alignment and involving more components, its performance benefits often far outweigh these considerations, delivering consistent, long-term detection precision essential for modern manufacturing, logistics, and safety systems.