digital photo electric control panel
- time:2025-07-25 01:01:10
- Нажмите:0
Unlock Precision & Efficiency: The Power of the Digital Photoelectric Control Panel in Modern Automation
Imagine production lines grinding to a halt because a sensor missed detecting a crucial component. Or envision safety systems failing to activate because a mechanical switch jammed. These scenarios highlight the critical need for reliable, precise, and adaptable sensing and control in today’s industrial and commercial environments. Enter the Digital Photoelectric Control Panel, a sophisticated convergence of light-based sensing and intelligent electronic control, designed to overcome these very challenges and drive operational excellence. This powerful technology represents a significant leap beyond basic sensing, offering unparalleled accuracy, flexibility, and robust performance for demanding automation tasks.
Demystifying the Core Technology: Light Meets Logic
At its heart, a Digital Photoelectric Control Panel integrates two fundamental components:
- Photoelectric Sensors: These are the “eyes” of the system. They utilize a light source (typically LED-based infrared, red, or laser light) and a receiver. They detect the presence, absence, distance, or position of an object based on the interruption or reflection of this emitted light beam. Common types include:
- Through-beam: Separate emitter and receiver; highest accuracy and long range.
- Retro-reflective: Emitter and receiver in one unit, beam reflected off a reflector; reliable for medium distances.
- Diffuse reflective: Emitter and receiver in one unit; detects objects by the light reflected directly off them; most common, versatile for short ranges.
- Digital Control Panel: This is the “brain.” It’s not just a simple switch. A digital control panel features a microprocessor or programmable logic controller (PLC) integrated within the housing or interface. This intelligence allows for:
- Advanced Configuration: Setting detection thresholds, sensitivity, time delays (on/off delay), operating modes, and output logic (e.g., light/dark operate) via intuitive digital interfaces (buttons, displays, software).
- Precise Signal Processing: Digitally filtering out ambient light interference, electrical noise, and other environmental factors that plague analog systems, ensuring consistent and reliable object detection.
- Flexible Output Control: Providing configurable digital outputs (transistor PNP/NPN, relay) to interface seamlessly with PLCs, motor controllers, alarms, or other machinery based on sensor status.
- Diagnostics & Communication: Offering status indicators, error reporting, and often communication capabilities (like IO-Link) for monitoring, remote configuration, and integration into Industrial IoT (IIoT) networks.
Why Choose a Digital Photoelectric Control Panel? Compelling Advantages Revealed
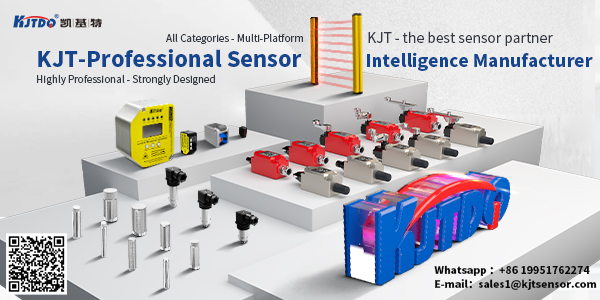
Moving beyond simple mechanical switches or basic analog sensors, digital photoelectric control panels offer transformative benefits:
- Unmatched Precision & Reliability: Digital signal processing eliminates the guesswork and inconsistency associated with analog thresholds. Detection is consistently accurate, minimizing false positives (nuisance trips) and false negatives (missed detections), critical for quality control and safety applications.
- Non-Contact Sensing: Objects are detected without physical contact. This eliminates wear and tear on both the sensor and the target object, significantly improving longevity and reducing maintenance costs, especially in high-speed or abrasive environments.
- Long Sensing Ranges & Versatility: Capable of detecting objects from millimeters up to several meters away, adapting to diverse applications – counting small parts on a conveyor or detecting large pallets in logistics. Their versatility shines across object sizes, materials (including glass, plastic, metal), and colors.
- Robust Performance in Challenging Environments: Engineered to withstand dust, moisture (often IP67/IP69K rated), vibration, and varying temperatures, making them suitable for demanding factory floors, food processing plants, and outdoor installations.
- Simplified Operation & Diagnostics: Digital interfaces provide clear set-up guidance, real-time status feedback, and diagnostic information. Troubleshooting becomes faster, minimizing costly downtime. Features like teach-in functionality allow for quick calibration simply by presenting the target object.
- Enhanced Flexibility & Integration: Configurable timers, counters, and logic functions directly within the panel reduce the need for external relays or PLC programming for simpler tasks. Compatibility with industrial networks facilitates seamless integration into larger automation systems.
Where This Technology Shines: Diverse Industrial Applications
The unique capabilities of digital photoelectric control panels make them indispensable across numerous sectors:
- Manufacturing & Assembly: Precise part counting, verifying component presence/absence before critical operations, detecting jams on conveyors, positioning robots for pick-and-place, ensuring proper fill levels.
- Packaging & Material Handling: Detecting labels, controlling case erectors/carton sealers, tracking products on high-speed lines, managing palletizing/depalletizing sequences, triggering sortation gates in warehouses.
- Food & Beverage: Monitoring bottle/can fill levels, detecting caps or lids, verifying label application, controlling packaging flow (even on transparent materials), ensuring safety guarding on machinery.
- Logistics & Warehousing: Detecting vehicles at loading docks, verifying pallet presence on Automated Guided Vehicles (AGVs), triggering barcode readers, managing inventory flow on sorters.
- Automotive: Ensuring component sequencing on assembly lines, detecting vehicle bodies in paint shops, monitoring part placement in robotic welding cells, controlling door and safety systems.
- Pharmaceutical & Medical: Verifying vial presence before filling or capping, ensuring precise component assembly in devices, guarding sensitive equipment.
Selecting the Right Digital Photoelectric Control Panel: Key Considerations
To maximize the benefits, consider these factors for optimal selection:
- Detection Mode & Range: Choose through-beam for longest range/highest reliability, retro-reflective for mid-range with simpler mounting, or diffuse reflective for close range and direct object detection. Measure the required sensing distance.
- Target Object Characteristics: Size, material (opaque, transparent, reflective? Shiny or matte?), color. Transparent object detection often requires specialized polarized or background suppression sensors.
- Environmental Conditions: Assess ambient light levels, temperature extremes, presence of dust, moisture, oil, or chemicals. Ensure the IP rating (Ingress Protection) is suitable (e.g., IP67 for washdown areas). Consider the panel’s material (stainless steel for harsh environments).
- Output Type & Configuration: Match the output (NPN sinking, PNP sourcing, relay contact, IO-Link) to the input requirements of your PLC, controller, or actuator. Determine if configurable logic functions or timers within the panel are needed.
- Power Supply: Ensure compatibility with your available voltage (e.g., 12-24V DC, 100-240V AC).
- Mounting & Connectivity: Consider space constraints and ease of wiring. Quick-connect options or M12 connectors can significantly speed up installation.
Embracing the Future of Intelligent Sensing & Control
The Digital Photoelectric Control Panel is far more than just a sensor; it represents a vital node of intelligence within modern automation ecosystems. By seamlessly blending the precision of photoelectric detection with the power of digital control and communication, it delivers unprecedented levels of reliability, adaptability, and diagnostic capability. In an era demanding higher efficiency, reduced downtime, and improved product quality, investing in this sophisticated technology isn’t just an upgrade – it’s a strategic imperative for businesses seeking to thrive in competitive markets. From safeguarding intricate assembly processes to optimizing logistics flows, its impact resonates throughout the entire value chain, solidifying its role as a cornerstone of industrial innovation.