Датчик рассеянного света
- time:2025-07-25 00:45:54
- Нажмите:0
Diffuse Photoelectric Sensors: The Unseen Eyes of Industrial Automation
Ever wondered how an automated assembly line knows a box is present, a vending machine detects a can, or packaging equipment senses a missing label? Often, the answer lies in a remarkably versatile and reliable workhorse: the диффузионный фотодатчик. These unobtrusive devices are fundamental pillars in countless automated systems, providing non-contact object detection through a simple yet ingenious principle.
Unlike their retroreflective cousins that require a separate reflector or thru-beam counterparts needing both a transmitter and a separate receiver, a диффузионный фотодатчик houses both the light emitter (usually an LED - infrared, red, or laser) and the receiver in a single unit. Its brilliance lies in detecting the diffuse reflection bouncing off the target object itself.
Here’s the core working principle:
- Emission: The sensor’s integrated emitter projects a focused beam of light towards the detection zone.
- Diffuse Reflection: When an object enters this zone, the light beam hits its surface. Unlike a mirror, most industrial targets (cardboard, plastic, metal cans, etc.) scatter the light rays in many directions – this phenomenon is called diffuse reflection.
- Reception: A portion of this scattered light travels back towards the sensor. The integrated receiver detects the presence and intensity of this returning light.
- Processing and Output: The sensor’s internal circuitry processes the received light signal. If the intensity exceeds a predetermined threshold (indicating an object is present within the detection range), the sensor triggers its output signal (e.g., switches an NPN or PNP transistor, or sends a digital signal). No object means insufficient light returns, resulting in no output trigger.
The Versatility Driving Ubiquity: Key Applications
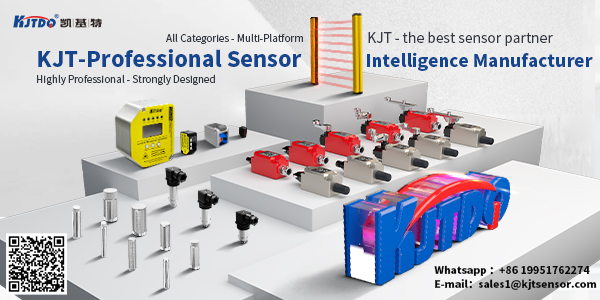
The simplicity, robustness, and cost-effectiveness of diffuse mode sensors make them incredibly popular across diverse sectors:
- Object Presence/Absence Detection: Confirming a part is on a conveyor belt, a bottle has entered a filling station, or a package is ready for sealing.
- Counting: Tallying products moving past a point on a line.
- Height/Distance Verification: Detecting variations in object height or stack levels (though less precise than specialized distance sensors).
- Web Break Detection: Sensing if a continuous material (like fabric, film, or paper) snaps or tears.
- Label Detection: Verifying labels are present on containers or packages.
- End-of-Travel Detection: Confirming hatches, doors, or guards are closed.
- Vending Machines & Consumer Electronics: Detecting coins, products, or tray positions reliably.
Why Choose a Diffuse Photoelectric Sensor? The Advantages
- Simplicity in Installation: Only one single device needs mounting, wiring, and alignment. There’s no reflector or separate receiver unit to position opposite it. This drastically simplifies setup and reduces installation time and cost.
- Cost-Effectiveness: Often the most economical photoelectric sensing solution due to the single-unit design and simpler installation requirements.
- Suitability for Various Targets: Can detect a wide range of non-shiny surfaces effectively. Modern sensors often feature background suppression technology to focus detection within a specific range, ignoring reflections from surfaces beyond the target.
- Compact Size: The integrated design typically results in a compact sensor housing, useful in space-constrained applications.
- Non-Contact Operation: Provides wear-free detection without physical interaction with the target object.
Navigating Limitations: Considerations for Optimal Use
While incredibly versatile, diffuse sensors have inherent limitations designers and engineers must consider:
- Detection Range Limitations: Diffuse sensors generally offer shorter maximum detection ranges compared to thru-beam or retroreflective models. Ranges typically vary from a few centimeters up to a meter or two, highly dependent on the model, light type (IR, Red, Laser), and target properties.
- Target Dependency: Performance is significantly influenced by the target’s:
- Color: Dark, matte surfaces absorb more light, reflecting less back to the sensor, which reduces effective range. Light, reflective surfaces reflect more light, increasing range.
- Surface Finish: Matte finishes work better than highly polished, mirror-like surfaces, which can specularly reflect light away from the receiver.
- Size: Very small objects may not reflect sufficient light to be reliably detected.
- Material: Transparent objects (like glass or clear plastic) can be extremely challenging or impossible to detect with standard diffuse sensors, as they allow most light to pass through.
- Background Interference: Objects behind the intended target can potentially reflect light back to the sensor, causing false triggers. Background suppression (BGS) technology is a critical feature in modern diffuse sensors to mitigate this by focusing detection sensitivity within a predefined zone.
- Environmental Factors: Dust, fog, steam, or heavy ambient light variations can scatter or wash out the sensor’s emitted light beam, potentially affecting reliability. Choosing sensors with robust housings (IP ratings) and environmental resistance is crucial in harsh conditions. Laser diffuse sensors often perform better in challenging environments and offer longer ranges and smaller spot sizes.
Choosing the Right Diffuse Sensor: Key Selection Criteria
To maximize performance, consider these factors:
- Required Sensing Range: Match the sensor’s specified range to your application’s needs, always considering the influence of target color/material.
- Target Characteristics: What color, material, surface finish, and size must it detect? Are there transparent objects?
- Background Suppression Needs: Is the detection zone likely to have objects beyond the intended target? Select sensors with BGS technology if required.
- Environmental Conditions: Exposure to dust, moisture, chemicals, or extreme temperatures? Require specific IP67/IP69K ratings for washdown areas?
- Light Source: Infrared is common and resistant to ambient light; bright red is easier for alignment; laser offers precision and longer range in specific models.
- Output Type: NPN, PNP, analog, or IO-Link? Match it to your controller’s input requirements.
- Housing Material & Size: Plastic for cost, metal for ruggedness? What physical space constraints exist?
- Special Features: Need teach-in functionality, adjustable sensitivity, synchronization options to prevent crosstalk, or high-speed response?
From managing simple presence checks on conveyor belts to enabling complex robotic guidance, the диффузионный фотодатчик remains an indispensable component in the automation landscape. Its elegant reliance on diffuse reflection delivers a powerful blend of simplicity, reliability, and affordability. Understanding their operating principle, inherent advantages, and key limitations allows engineers and technicians to leverage these “unseen eyes” effectively, ensuring smooth, efficient, and reliable operation in countless automated processes across the globe.