Промышленный фотодатчик
- time:2025-07-25 00:35:42
- Нажмите:0
Industrial Photo Eye Sensors: The Unseen Guardians of Automation Efficiency
In the relentless hum of modern manufacturing, efficiency is paramount. Unplanned downtime is the enemy, safety is non-negotiable, and precision is demanded every second. Amidst the whirring robots, clanging conveyors, and intricate assembly lines, a humble yet indispensable technology works tirelessly, often unnoticed: the industrial photo eye sensor. These compact optoelectronic sentinels are fundamental to automation, providing the critical “eyes” that machines lack, enabling detection, positioning, counting, and safeguarding that keep operations running smoothly and safely.
Understanding the “Photo Eye”: Core Functionality
At its heart, an industrial photo eye sensor (more formally known as a photoelectric sensor) is a device that uses light to detect the presence, absence, or distance of an object without physical contact. It consists of two essential parts:
- Emitter (Light Source): Typically an infrared LED, though visible red or laser light sources are also common depending on the application. This generates the light beam.
- Receiver: A photodiode or phototransistor that detects incoming light and converts it into an electrical signal.
The fundamental principle revolves around the interaction between the emitted light beam and the target object. Depending on the sensor type (discussed next), detection occurs when the beam is either interrupted by an object or reflected back to the receiver. This change in light intensity triggers the sensor’s output to switch states (ON/OFF), providing a vital signal to the control system – effectively telling the machine, “Something is here,” or “The path is clear.”
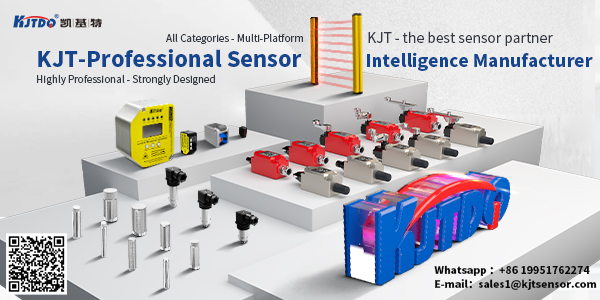
Navigating the Sensor Spectrum: Key Types Explained
Choosing the right Фотоэлектрический датчик is crucial for optimal performance. The primary types differ based on how the emitter and receiver are configured and how they interact with the target:
- Through-Beam Sensors (Opposed Mode):
- How it Works: Emitter and receiver are housed in separate units, facing each other directly. The receiver constantly “sees” the emitter’s beam.
- Detection Trigger: Detection occurs when an object interrupts the beam between the two units.
- Преимущества: Longest sensing ranges (often meters), high immunity to ambient light, and excellent reliability for clear/opaque objects. Ideal for: Detecting objects on high-speed conveyors, large object counting, safety light curtains.
- Limitation: Requires wiring and mounting two separate components, which can be less convenient.
- Retroreflective Sensors:
- How it Works: Emitter and receiver are housed in the same unit. A special reflector (corner-cube or tape) is placed opposite the sensor. The emitted beam travels to the reflector and bounces directly back to the receiver within the same housing.
- Detection Trigger: Detection occurs when an object interrupts the beam path to the reflector.
- Преимущества: Simpler installation than through-beam (only one sensor unit to mount/wire, reflector on opposite side), good sensing range (less than through-beam but still substantial). Ideal for: Packaging line presence detection, pallet positioning, door monitoring.
- Limitation: Performance depends on a clean reflector; highly reflective or shiny objects can sometimes confuse the sensor.
- Diffuse Reflection Sensors (Proximity Mode):
- How it Works: Emitter and receiver are housed in the same unit. The sensor emits light, and the receiver detects light diffusely reflected off the target object itself.
- Detection Trigger: Detection occurs when enough reflected light from the target reaches the receiver.
- Преимущества: Simplest installation – only Один. unit needed, no separate reflector required. Well-suited for detecting objects close to the sensor. Ideal for: Short-range object detection, bottle/can counting, label presence, level detection in bins/vessels.
- Limitations: Sensing range is shortest among the types. Performance highly dependent on target color, surface finish (rough/dark absorbs more light, smooth/light reflects better), and background conditions. More susceptible to ambient light interference.
Beyond Basic Detection: Versatility Across Industries
The applications for Промышленный фотодатчик are incredibly diverse, touching virtually every automated sector:
- Manufacturing & Assembly: Precise positioning of parts on conveyors, robotic arm guidance, verifying component assembly (“presence detection”), detecting missing labels or caps (“quality control”), counting products entering/leaving stations.
- Packaging: Verifying filled bottle/can heights (“level detection”), detecting labels, controlling case/tray erectors and sealers, counting products into cartons.
- Перевозка материалов: Monitoring conveyor belt jams (“object detection”), detecting pallets at loading docks, triggering sortation gates, controlling stack height in warehouses. Through-beam sensors excel here for long-range detection.
- Printing & Paper: Monitoring paper web breaks, detecting sheet presence in printers or copiers, controlling roll diameters.
- Automotive: Verifying door, hood, or trunk closure on assembly lines, robot safety zones for collaborative cells, part presence verification during sub-assembly.
- Food & Beverage: Ensuring proper bottle/can fill levels, detecting foreign objects (within application limits), verifying cap/can seal placement, counting packaged items. Sanitary washdown-rated sensors are critical here.
Selecting the Right “Eye” for the Job: Critical Factors
Implementing Фотоэлектрический датчик effectively requires careful consideration:
- Sensing Range: How far away must the sensor detect the object? Through-beam offers the longest range.
- Target Characteristics: What is the object’s size, color, material, and surface finish? Shiny, dark, or non-reflective targets challenge diffuse sensors.
- Operating Environment: Consider dust, dirt, fog, temperature extremes, washdown requirements (IP ratings), vibrations, and ambient light levels. Sensors with background suppression are vital for rejecting irrelevant reflections.
- Response Time & Speed: How fast is the object moving? Choose a sensor with a fast enough response time to reliably detect objects at line speed.
- Output Type: Does the control system require a standard PNP/NPN discrete signal, analog distance output, or IO-Link communication for advanced diagnostics and configuration?
- Mounting & Physical Constraints: Space limitations dictate sensor size and form factor (cylindrical, rectangular, miniature). Diffuse sensors offer single-unit simplicity.
Optimizing Performance & Longevity: Key Practices
Even the most robust industrial photo eye sensor requires attention:
- Proper Alignment: Especially critical for through-beam and retroreflective sensors. Misalignment leads to unreliable detection.
- Lens Maintenance: Keep the emitter and receiver lenses clean. Dust, grime, or condensation significantly degrade performance. Regular inspection and cleaning are simple but crucial preventative steps.
- Avoid Shiny/Oblique Backgrounds: For diffuse sensors, ensure the background behind the target isn’t highly reflective or angled in a way that could cause false reflections. Background suppression sensors help mitigate this.
- Electrical Protection: Ensure stable power supply and protect wiring from EMI and physical damage. Surge protection can be vital in harsh electrical environments.
- Leverage Diagnostics: Modern sensors, especially those with IO-Link, provide valuable data like operating hours, light intensity levels, and temperature, enabling predictive maintenance before failures occur.
From ensuring a bottle is filled and capped correctly to preventing a robotic arm from colliding with an operator, Промышленный фотодатчик are the silent workhorses of automation. They provide the essential feedback loop