Датчики приближения и фотоэлектрические датчики
- time:2025-07-24 04:05:03
- Нажмите:0
Proximity Sensor vs. Photoelectric Sensor: Choosing the Right Detection Solution
In the intricate dance of modern automation, manufacturing, and countless smart applications, object detection is the fundamental step. Two ubiquitous technologies enabling this are the датчик приближения and the Фотоэлектрический датчик. While both serve the critical purpose of detecting the presence or absence of an object without physical contact, their underlying principles, strengths, and ideal applications differ significantly. Selecting the right one isn’t just a technicality; it’s about optimizing reliability, efficiency, and cost-effectiveness in your specific environment. This guide cuts through the confusion, helping you navigate the proximity sensor vs photoelectric sensor decision.
Understanding the Core Technologies
- Proximity Sensors: Sensing the Invisible Field
Primarily inductive or capacitive, proximity sensors detect objects by generating an electromagnetic field. Inductive proximity sensors are the workhorses for detecting metallic objects. A coil inside generates a high-frequency oscillating field. When a metal object enters this field, it induces eddy currents within the metal, causing a change in the oscillation amplitude. The sensor’s circuit detects this change and triggers a signal. Their key strengths lie in robustness, resistance to environmental contaminants like dust, oil, or water (due to the sealed sensing face), and insensitivity to target color or surface finish. They excel in short-range applications (typically millimeters to a few centimeters) common on machinery, conveyor systems, and cylinder positioning.
Capacitive proximity sensors, on the other hand, detect both metallic and non-metallic objects (like plastics, wood, liquids, powders). They work on the principle of capacitance change. The sensor forms one plate of a capacitor, the detected object (or background) forms the other, and the air gap is the dielectric. When an object enters the sensing zone, it alters the capacitance, which the sensor detects. This makes them ideal for level detection in tanks (liquids, grains) or detecting materials through containers.
- Photoelectric Sensors: Harnessing Light
Photoelectric sensors utilize a beam of light (visible red, infrared, or laser) to detect objects. They consist of an emitter (light source) and a receiver. Detection occurs when the target object interrupts or reflects this light beam. There are three main operating modes:
- Through-Beam (Opposed Mode): The emitter and receiver face each other. Detection occurs when the object breaks the light beam. This offers the longest sensing range and highest reliability, but requires mounting on both sides of the target path.
- Retro-Reflective: The emitter and receiver are housed together. A reflector is mounted opposite. The emitter sends light to the reflector, which bounces it back to the receiver. Detection occurs when the object interrupts the reflected beam. Easier mounting than through-beam, but reflective targets can sometimes cause issues.
- Diffuse (Proximity Mode): Both emitter and receiver are in the same unit. The emitter sends light, and the receiver detects the light reflected directly off the target object itself. Simplest mounting, but sensing range is shorter and performance is affected by the target’s color, reflectivity, and surface texture.
Photoelectric sensors excel at longer-range detection (centimeters to tens of meters) and detecting objects regardless of material (metal, plastic, wood, glass etc.), though transparent objects can be challenging. They are highly versatile but can be susceptible to interference from ambient light, dust, fog, or steam obscuring the beam.
Key Differences: A Head-to-Head Comparison
Understanding the distinct characteristics is crucial for making an informed choice:
- Operating Principle:
- Proximity Sensor: Relies on changes in an electromagnetic field (inductive for metals, capacitive for most materials).
- Photoelectric Sensor: Relies on the presence, absence, or reflection of a light beam.
- Target Material:
- Proximity Sensor (Inductive): Only detects metals. Material composition and type (ferrous/non-ferrous) affect sensing distance.
- Proximity Sensor (Capacitive): Detects metals and non-metals (solids, liquids, powders).
- Photoelectric Sensor: Detects virtually any material, though transparent or highly reflective targets require specific sensor selection and setup.
- Sensing Range:
- Proximity Sensor: Generally short-range (mm to cm). Capacitive sensors often have shorter ranges than inductive.
- Photoelectric Sensor: Offers much longer ranges (cm up to 100m+ for specialized laser sensors). Through-beam provides the longest range.
- Environmental Suitability:
- Proximity Sensor (Especially Inductive): Highly resistant to dust, dirt, oil, water splashes, and vibrations. Ideal for harsh industrial environments. Generally unaffected by ambient light.
- Photoelectric Sensor: Susceptible to performance degradation from dust, fog, steam, or heavy contamination that obscures the light beam. Can be affected by strong ambient light sources. Requires careful selection and sometimes protective housings for dirty environments. Laser sensors offer better performance in challenging conditions.
- Target Characteristics Sensitivity:
- Proximity Sensor (Inductive): Sensitive to the Тип of metal (ferrous best, non-ferrous shorter range). Size and shape also matter. Less sensitive to surface color/reflectivity.
- Capacitive Sensor: Sensitive to the dielectric constant of the material and material density.
- Photoelectric Sensor (Diffuse): Highly sensitive to the target color (dark colors absorb light, reducing range) and surface texture/reflectivity (shiny surfaces reflect more light, increasing range). Through-beam and retro-reflective are less affected by target surface properties.
Choosing the Right Sensor: Application is Key
The ‘proximity sensor vs photoelectric sensor’ debate is resolved by understanding your specific needs:
Choose a Proximity Sensor (Inductive) When:
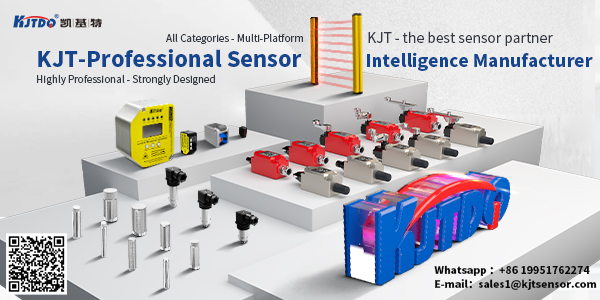
You need to detect metal objects only.
The environment is harsh (dusty, oily, wet).
The sensing range is short (mm/cm).
Target color or reflectivity varies.
Robustness and reliability are paramount.
Example Applications: Machine tool part presence, end-of-stroke detection on pneumatic cylinders, metal object counting on conveyors, gear tooth sensing.
Choose a Proximity Sensor (Capacitive) When:
You need to detect non-metallic objects, liquids, or granular materials.
Sensing range can be short.
You might need to detect materials through thin non-metallic barriers.
Example Applications: Liquid level control in plastic tanks, detecting full/empty in bins with plastic liners, paper/cardboard stack height detection.
Choose a Photoelectric Sensor When:
You need longer detection ranges.
You need to detect non-metallic objects (especially where capacitive range is insufficient).
The target material varies significantly (as long as not transparent).
The environment is relatively clean (or appropriate sensor type/housing is chosen for minor contamination).
Precise positioning or small object detection is required (especially with laser types).
Example Applications: Object detection on fast-moving conveyors (long