диффузионный тип фотоэлектрического датчика
- time:2025-07-24 02:53:30
- Нажмите:0
Diffuse Photoelectric Sensors: Your Go-To Solution for Simplified Object Detection
In the intricate world of industrial automation, reliably detecting the presence or absence of objects is a fundamental requirement. Among the array of sensing technologies available, Фотоэлектрический датчик consistently prove invaluable. And within this category, the diffuse reflective type stands out as one of the most popular and versatile choices, prized for its simplicity and effectiveness in countless applications. If you’ve ever needed a sensor that’s easy to install, cost-effective, and dependable for detecting objects at close range, understanding the diffuse photoelectric sensor is essential.
What Exactly is a Diffuse Photoelectric Sensor?
At its core, a диффузионный фотодатчик operates on a surprisingly straightforward principle. Unlike its through-beam counterparts requiring a separate transmitter and receiver unit, or retro-reflective types needing a reflector, the diffuse sensor houses both the light emitter (typically an LED) and the receiver within a single housing. The sensor works by emitting a beam of light (usually visible red, infrared, or laser) towards the target. When this beam strikes the target object, some of the light is diffusely reflected – meaning it scatters in many directions – and a portion of this scattered light bounces back towards the sensor’s receiver.
The sensor’s internal electronics are finely tuned to detect this returning light intensity. When the received light exceeds a predefined threshold (indicating an object is present within the sensing range), the sensor triggers its output signal (e.g., switches from OFF to ON, or vice-versa). The detection occurs solely through light bouncing back from the target itself, eliminating the need for any external components placed opposite the sensor.
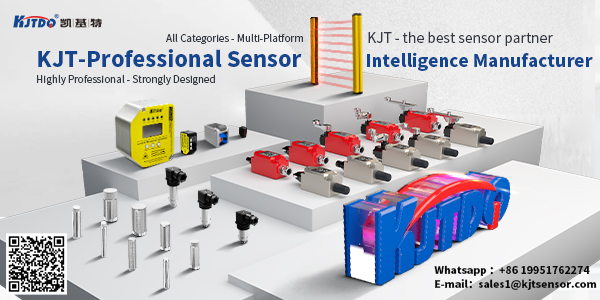
The Compelling Advantages of Diffuse Sensors
The popularity of diffuse photoelectric sensors stems from several key benefits:
- Simplified Installation: This is arguably their biggest advantage. Only one device needs to be mounted, powered, and wired on the machine side. There’s no complex alignment with a separate receiver or reflector across the detection path, drastically reducing installation time and complexity.
- Cost-Effectiveness: By combining emitter and receiver in one unit and eliminating the need for reflectors or separate receiver housings, diffuse sensors are generally more economical than through-beam or retro-reflective sensors for many common tasks.
- Flexibility in Object Detection: Diffuse sensors can detect a wide variety of objects – boxes, bottles, cartons, parts on a conveyor, irregularly shaped items, and even liquids in clear containers – provided the object reflects enough light back.
- Compact Design: Their single-housing nature often results in a smaller, more compact sensor profile, making them easier to fit into tight spaces on machinery.
- Sensing Range: While not typically as long as through-beam sensors, modern diffuse sensors offer respectable sensing ranges suitable for a vast array of proximity detection tasks, typically from a few millimeters up to several hundred millimeters or more, depending on the specific model and technology (e.g., standard diffuse vs. background suppression).
Understanding the Limitations and Challenges
While powerful, diffuse sensors aren’t a universal panacea. Being aware of their limitations ensures successful application:
- Dependence on Target Reflectivity: Performance is inherently linked to how well the target reflects light. Highly reflective targets (like mirrors or glossy white plastic) are easy to detect at longer ranges. Low-reflective or dark/matte targets (black rubber, dark textiles, unvarnished wood) absorb more light, reflecting less back to the sensor, significantly reducing the effective sensing distance and potentially causing detection failures. Target color and surface finish directly impact reliability.
- Background Interference: Objects or surfaces behind the target can also reflect light back to the sensor. If the background is highly reflective or close enough, the sensor might falsely detect it instead of the actual target, or fail to detect the target reliably.
- Contrast Sensitivity: Detecting targets with reflectivity very similar to the background can be challenging for standard diffuse sensors.
- Sensing Range Limit: Maximum range is generally shorter than other photoelectric types and varies considerably with target reflectivity.
Overcoming Challenges: Background Suppression (BGS)
To combat the critical issue of background interference, a significant advancement was made: Diffuse Sensors with Background Suppression (BGS), also sometimes called “fixed field” or “convergent beam” sensors. These are sophisticated diffuse sensors incorporating triangulation principles.
- How BGS Works: The emitted light beam is focused at a precise, predetermined distance in front of the sensor. The receiver optics are designed so that only light reflected from objects at this exact focal point distance is focused sharply onto the receiver element. Light reflected from objects closer than the focal point hits the receiver above the optimal point. Light from objects farther away than the focal point (i.e., the background) hits the receiver below this point.
- The Advantage: By electronically analyzing where the light falls on the receiver element, the BGS sensor ignores anything beyond its preset focal point distance. This allows it to reliably detect a low-reflective target very close to the sensor, even if there’s a highly reflective surface right behind it. BGS fundamentally solves the background interference problem and allows detection based on the position of the reflection, not just its intensity.
Where Diffuse Sensors Shine: Key Applications
The combination of simplicity, reliability, and cost makes diffuse sensors ubiquitous:
- Object Presence/Absence on Conveyors: Detecting products, packages, or totes moving along conveyor lines for counting, sorting, or triggering downstream processes.
- Part Detection in Machinery: Verifying parts are in place for robotic assembly, machining operations, or packaging.
- Level Detection: Monitoring fill levels in bins, hoppers, or tanks (works well for powders, pellets, and opaque liquids). Can detect products stacked on pallets.
- Bottle/Cap Detection: Ensuring bottles are present before filling or capping. Verifying caps are correctly applied.
- End-of-Travel Detection: Confirming the presence of components like cylinders, slides, or doors in their end positions.
- Web Break/Slack Detection: Monitoring the presence or tension of materials like film, foil, or textiles.
- Carton Erecting/Packing: Detecting flaps, case forming, and product insertion points.
Selecting the Right Diffuse Sensor: Key Considerations
Choosing the best diffuse sensor for your application involves evaluating several factors:
- Required Sensing Range: How far away is the target? Remember this is highly dependent on target reflectivity. Consult sensor datasheets, which typically list max ranges for standard targets (e.g., white matte card).
- Target Characteristics: What is the target material, color, and surface finish? Low-reflective targets demand sensors either specifically designed for them or BGS types. Know your target’s reflectivity.
- Background Environment: Is there potential for highly reflective surfaces behind the target area? If yes, background suppression (BGS) is strongly recommended over standard diffuse to avoid false triggers.
- Operating Environment: Consider temperature, humidity, dust, dirt, splashing water, or washdown requirements. Choose sensors with appropriate Ingress Protection (IP) ratings (e.g., IP67, IP69K for harsh environments).
- Required Output Type: Does your controller need a simple switch (PNP/NPN), or a