photo electric control panel
- time:2025-07-24 01:06:29
- Нажмите:0
The Silent Sentinel: How Photoelectric Control Panels Power Modern Automation
Imagine walking into a warehouse after dusk. Instead of fumbling for a switch, the place smoothly illuminates. Conveyors start, safety gates lift, and an intricate dance of machinery begins – all triggered seemingly by your presence. This isn’t magic; it’s the intelligent orchestration of a Photoelectric Control Panel, the unsung brain behind countless automated systems. These panels, integrating sophisticated light-based sensing technology with precise logic control, are fundamental to efficient, safe, and responsive operations across diverse industries. Understanding their function reveals why they are indispensable in our increasingly automated world.
At its core, a photoelectric control panel manages systems that rely on the detection of light to make decisions. It’s the central hub for Фотоэлектрический датчик (often called photoeyes, photo sensors, or light curtains). These sensors work on a simple but powerful principle: they emit a beam of light (visible, infrared, or laser) and detect changes in the received light signal. This change could be an interruption (an object blocking the beam), reflection (detecting the presence of an object), or attenuation (reduced light intensity signaling proximity or contrast changes).
But the sensor is only the input device. The true intelligence lies within the control panel. This panel serves several critical functions:
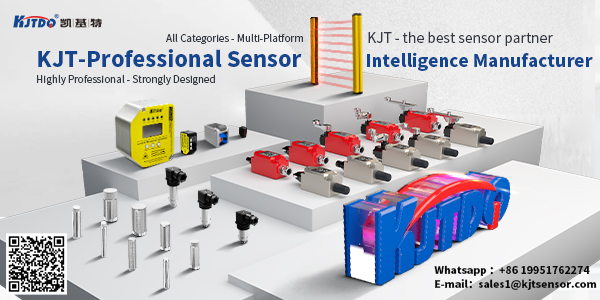
- Power Supply Management: It provides stable, regulated power (often 12-24V DC or 120-240V AC) to the connected photoelectric sensors and associated output devices.
- Signal Processing: It interprets the often delicate analog or digital signals coming from the sensors. This involves filtering noise, compensating for ambient light variations, and determining the exact state (beam present/broken, object detected/absent).
- Logic Execution: This is where the “control” happens. Based on the processed sensor signals and predefined programming or configuration (e.g., using relays, timers, counters, or a Programmable Logic Controller - PLC within the panel), the panel makes decisions. If Sensor A’s beam is broken and Sensor B detects an object, then activate Output Relay C to start the conveyor. This logic can be remarkably complex.
- Output Control: The panel directly controls output devices like relays, motor starters, solenoid valves, indicator lights, or communication signals (e.g., to a SCADA system) based on its logic decisions. Relays within the panel are often the workhorses, physically switching higher power loads.
- Diagnostics and Monitoring: Modern panels feature status LEDs, display screens, or communication ports (like Ethernet/IP, Modbus) providing vital feedback on sensor health, operational status, faults, and system performance, enabling rapid troubleshooting. Remote diagnostics capability is increasingly a standard feature.
Why Light? The Advantage of Photoelectric Sensing
Photoelectric sensors offer distinct advantages that make them ideal partners for control panels:
- Non-Contact Detection: They sense objects without physical touch, eliminating wear and tear and allowing detection of fragile items.
- Long Range: Compared to proximity sensors, photoelectric sensors can detect objects over much greater distances (inches to tens of meters).
- Многогранность: They detect a vast array of objects regardless of material (metal, plastic, wood, glass, liquid) – provided there’s sufficient contrast or opacity to affect the light beam. Various types (through-beam, retroreflective, diffuse reflective) offer solutions for different applications.
- High Speed and Precision: Capable of detecting extremely fast-moving objects or minute positional changes with high accuracy, often measured in microseconds.
Where Photoelectric Control Panels Shine: Real-World Applications
The synergy of photoelectric sensing and centralized control creates solutions across numerous sectors:
- Industrial Automation & Manufacturing: Photoelectric control panels manage conveyor sorting (detecting package size/material for diverting), automated assembly (part presence/position verification), robotic cell guarding (safety light curtains integrated with machine control via the panel), filling level detection, and packaging line control. Precision timing and reliable object detection are crucial here.
- Material Handling & Logistics: Controlling pallet elevators, regulating automated storage and retrieval systems (AS/RS), managing baggage handling systems, and ensuring safe operation of automated guided vehicles (AGVs) all rely heavily on photoelectric sensors managed by dedicated panels. Safety system integration (e.g., E-Stop circuits tied to light curtains) is paramount.
- Building Automation: While often integrated into broader systems, specialized panels manage automatic door operation (detecting approaching pedestrians), parking garage lighting control (presence detection), and access control systems. Energy efficiency through intelligent lighting control is a major driver.
- Security & Access Control: Perimeter security (invisible barrier breach detection), gate automation, and restricted access points frequently utilize photoelectric beams or light curtains connected to central alarm and control panels.
- Food & Beverage, Pharmaceutical: Ensuring hygiene, photoelectric sensors detect product presence on high-speed bottling lines, verify cap placement, count items, and control labeling – all orchestrated by robust control panels designed for harsh washdown environments.
The Tangible Benefits: Beyond Just Sensing
Implementing a photoelectric control panel system delivers significant advantages:
- Enhanced Efficiency: Automated processes driven by reliable sensing minimize downtime and boost throughput. Machines only run when needed (e.g., lighting, conveyors), saving energy.
- Повышение безопасности: Integration with safety-rated light curtains and perimeter guards provides non-contact safeguarding for personnel around hazardous machinery. The panel ensures safe shutdown sequences.
- Reduced Costs: Minimized physical wear (non-contact), lower energy consumption, fewer manual interventions, and rapid fault diagnosis via advanced diagnostics translate to lower operational expenses.
- Increased Flexibility: Modern panels are configurable and programmable. Logic can be easily adapted as production needs change, supporting different sensor types and output requirements.
- Superior Reliability: Centralized monitoring via the panel allows predictive maintenance and quicker response to sensor or circuit issues, maximizing system uptime. Robust protection against electrical noise and surges is standard.
- Data Connectivity: Integration with factory networks (IoT/Industry 4.0) through the panel enables real-time process monitoring, data logging, and production optimization analytics.
The Future: Smarter Integration and Intelligence
The evolution of photoelectric control panels is tightly linked to broader automation trends. We see a move towards:
- Integrated Smart Sensors: Sensors with more onboard intelligence (IO-Link technology) communicating detailed diagnostic data and configuration parameters directly to the panel/controller.
- Smaller, More Powerful PLCs: Control panels increasingly leverage compact, high-performance PLCs capable of complex logic, networking, and even edge computing tasks.
- Simplified Configuration: Graphical user interfaces (GUIs) and web-based configuration tools are making setup and programming more accessible.
- Seamless IIoT Connectivity: Panels becoming primary nodes on the Industrial Internet of Things (IIoT), enabling cloud analytics, remote supervision, and integration with enterprise systems for unprecedented operational insight. The focus is shifting towards predictive maintenance and optimized performance.
Far more than just a junction box for wires, the photoelectric control panel represents the critical convergence point of sensing intelligence and automated action. By translating