Датчик рассеянного луча
- time:2025-07-23 15:07:10
- Нажмите:0
Unlocking Efficiency: The Essential Guide to Diffuse Beam Sensors in Modern Automation
Imagine the high-speed ballet of a packaging line: bottles zipping by, labels flying on, caps twisting tight. Now imagine a single misaligned bottle causing chaos – jams, spills, costly downtime. Preventing this hinges on reliable, instant detection. Enter the Датчик рассеянного луча, a frequently unsung hero in industrial automation, offering a remarkably simple yet powerful solution for countless object detection challenges. Its core principle? Harnessing light itself bounced back from a target to trigger an action.
But how does this ubiquitous Фотоэлектрический датчик actually work? Unlike its cousins – the retro-reflective sensor needing a reflector or the through-beam sensor requiring separate emitter and receiver units – the diffuse sensor integrates everything into one compact housing. It contains both the infrared or visible light emitter and the photoelectric receiver. The emitter constantly projects a light beam. When an object enters its detection zone, light strikes the object’s surface and scatters (diffuses) in various directions. If enough of this scattered light reflects back towards the sensor’s receiver, exceeding a pre-set threshold, the sensor switches its output state, signaling “object detected!”
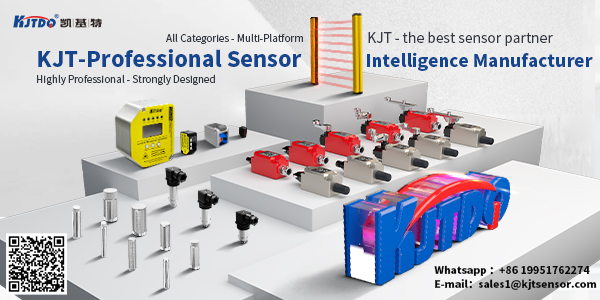
This self-contained nature bestows several critical advantages making diffuse sensors exceptionally popular:
- Simplified Installation: Forget complex alignment! The absence of a separate reflector or receiver unit drastically cuts installation time and complexity. Mount the single sensor unit, point it towards the detection area, power it up, and you’re often ready. This plug-and-play simplicity is a major time and cost saver during setup and maintenance.
- Cost Efficiency: Requiring only one physical unit instead of two (emitter + receiver) or one unit plus a dedicated reflector translates directly into lower hardware costs. This cost-effectiveness scales significantly across large production lines deploying dozens or hundreds of sensors.
- Space Optimization: Tight spaces are no longer a barrier. Only needing mounting space on one side of the detection path is a huge advantage where machine real estate is scarce. This compact nature allows integration into intricate machinery designs.
- Target Flexibility: Diffuse sensors are generally less sensitive to the target material’s optical properties compared to some proximity sensors. While color, texture, and reflectivity do influence detection range (see limitations below), they can reliably detect a wide variety of objects – from matte black plastics to shiny metal cans.
These strengths make diffuse beam sensors indispensable across diverse sectors:
- Packaging & Filling: Detecting presence/absence of bottles, cans, boxes, caps, labels on conveyors or within filling stations. Monitoring stack heights or product counts.
- Перевозка материалов: Verifying part presence in fixtures, detecting pallets on rollers, checking for material jams, ensuring part orientation.
- Automotive Assembly: Confirming component seating (like door panels, dashboards), verifying robot tool pickup/dropoff, detecting vehicle bodies on lines.
- Printing & Paper: Monitoring paper roll diameters, detecting sheet presence or misfeeds, verifying label application.
- Food & Beverage: Detecting filled containers, checking for lids, ensuring proper stacking on pallets.
However, understanding their limitations is key to successful application:
- Detection Range Uncertainty: This is the primary trade-off for simplicity. The effective sensing range relies heavily on the target’s size, color, surface texture, and reflectivity. A large, white, matte object will be detected at maximum range. A small, black, shiny object will significantly reduce the usable range. Always consult the sensor’s datasheet for specific figures and consider worst-case scenarios.
- Background Interference: Objects behind the intended target might also reflect light back, potentially causing false triggers. Careful positioning and potentially using models with background suppression technology are crucial. Background suppression (BGS) sensors use triangulation principles to focus detection on a specific, defined distance, ignoring reflections beyond it.
- Environmental Factors: Dust, fog, steam, or intense ambient light can scatter the emitted beam before it reaches the target or swamp the receiver with stray light, reducing reliability. Choosing sensors with higher IP ratings (for dust/water resistance) and robust housing materials becomes essential in harsh conditions. Some offer teach functions to adapt to changing environments.
Selecting the right diffuse sensor demands careful consideration:
- Required Sensing Range: Determine the maximum working distance needed for your specific target and add a safety margin. Don’t rely solely on the sensor’s nominal “max range.”
- Target Characteristics: Evaluate size, color, reflectivity, and material. Use the manufacturer’s correction factors if provided. Test if possible.
- Operating Environment: Assess dust, moisture, temperature extremes, vibration, and ambient light levels. Choose appropriate IP rating and housing material (metal often offers better EMI resistance).
- Output Type: Decide between PNP / NPN, relay, or analog outputs based on your control system requirements. Light-on/Dark-on operation selection is also vital.
- Характеристики: Consider needs for adjustable sensitivity, teach-in capability, IO-Link connectivity for smart diagnostics and configuration, or specialized optics/housings.
Why does the Датчик рассеянного луча remain a cornerstone of industrial detection? It strikes an unparalleled balance between simplicity, cost-effectiveness, and performance for a vast array of proximity sensing tasks. Its one-unit design slashes installation complexity and cost. While understanding its dependence on target properties is crucial, modern variants with features like background suppression and enhanced environmental resistance continue to expand its reliable application envelope. From ensuring the smooth flow of packages to verifying critical assembly steps, the диффузионный фотодатчик is a fundamental building block enabling efficiency and reliability in the automated world.