Сенсоры PE
- time:2025-07-23 13:40:37
- Нажмите:0
The PE Sensor: Phase Enhancement for Uncompromising Detection Reliability
Imagine a high-speed automotive assembly line suddenly halted. Thousands of dollars per minute evaporate. The culprit? A standard photoelectric sensor failed again, blinded by a stray reflection or tricked by a glossy surface. This scenario underscores the critical need for unwavering detection accuracy in demanding industrial environments. Enter the PE sensor (Phase Evaluation Sensor), a sophisticated evolution in photoelectric sensing leveraging phase-shift analysis to cut through interference and deliver unprecedented reliability where standard sensors falter.
At its core, a Фотоэлектрический датчик functions by emitting a light beam (typically infrared, visible red, or laser) towards a target. A receiver then detects either the reflected beam (diffuse mode), the beam broken by an object (through-beam), or the beam reflected off a specific reflector (retro-reflective). Traditional sensors primarily measure the amplitude (intensity) of the returning light signal. If the amplitude exceeds a set threshold, an object is ‘seen’. However, amplitude-based detection is inherently vulnerable. Ambient light interference, dirt accumulation on lenses or reflectors, color variations, and surface reflectivity changes (like glossy vs. matte finishes) can all dramatically alter the received light intensity, leading to false triggers or missed detections.
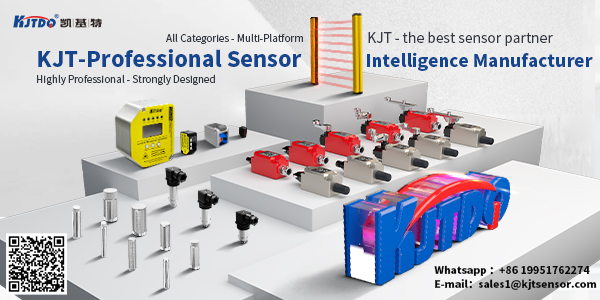
This is where Phase Evaluation technology, the defining characteristic of a high-performance PE sensor, becomes revolutionary. Instead of solely relying on the strength of the returned light, the PE sensor meticulously analyzes the phase shift – the subtle time difference – between the emitted light pulse and the reflected pulse returning to the receiver.
Here’s the breakthrough:
- Modulated Light Emission: The PE sensor emits its light beam as a rapidly modulated signal, essentially pulsing the light at a very high, specific frequency.
- Precise Echo Analysis: The sensor’s sophisticated receiver circuit is finely tuned to detect only the light signal oscillating at exactly that same modulation frequency. It effectively ignores light signals at other frequencies, such as steady-state ambient light (from overhead lamps, sunlight) or erratic interference.
- Phase-Shift Measurement: Crucially, it measures the minuscule delay (phase shift) between the outgoing modulated pulse and the returning echo. This phase shift is directly proportional to the distance the light has traveled to the target and back.
- Intelligent Object Discrimination: The sensor evaluates this phase-shift data. If the light takes longer to return (indicating it traveled further, likely bouncing off a distant background or a reflector), the sensor knows it’s not seeing the intended close-range target. Conversely, a specific, expected phase shift confirms the presence of the target object at the desired sensing distance.
The profound implications of Phase Evaluation PE sensors are felt across industries facing tough sensing challenges:
- Overcoming Challenging Surfaces: They excel where standard diffuse sensors fail: detecting transparent objects (bottles, blisters, glass sheets), ultra-dark or ultra-black materials, or targets with widely varying reflectivity (shiny metal vs. dull plastic). The phase-shift information is largely independent of reflectivity amplitude.
- Immune to Ambient Light: Operating reliably in bright sunlight or under intense workshop lighting is a hallmark of PE sensors. Their modulated signal and tuned receiver filter out DC and low-frequency ambient light noise.
- Extended Sensing Ranges & Precision: Laser-based PE sensors offer greater detection ranges and significantly finer resolution than standard diffuse types, enabling precise positioning or small object detection even at distance.
- Stable Performance Amidst Contamination: Gradual lens fogging or dust accumulation tends to attenuate the light signal amplitude relatively equally across the modulation frequency. While it might reduce overall range, the phase information remains a robust indicator for detecting the presence of an object, preventing complete failure due to light loss. Critical process reliability is maintained.
- Background Suppression Mastery: This is arguably their strongest suit. By precisely measuring the distance via phase shift, PE background suppression (BGS) sensors can be configured to detect objects only within a very specific, narrow ‘detection window’ in front of the sensor, rejecting objects or surfaces beyond that window (the background). This is invaluable for:
- Detecting components on a conveyor belt while ignoring the belt structure beneath.
- Ensuring packaging flaps are folded correctly within the machine, ignoring the surrounding machinery.
- Counting items on a pallet, ignoring the pallet itself or warehouse walls.
Selecting and implementing a PE sensor requires consideration:
- Diffuse vs. Background Suppression (BGS): Understand if you need simple diffuse presence detection or the powerful background rejection capability. BGS variants are far more common for PE sensors due to their unique advantage.
- Sensing Range & Spot Size: Match the sensor’s specified range and the size of its light spot to your target size and required detection distance.
- Output Configuration: Ensure the electrical output signal (PNP/NPN, NO/NC) and connection type (cable, connector) are compatible with your control system.
- Environmental Rating: Choose a housing (typically cylindrical or block style) and IP rating suitable for dust, moisture, vibration, and temperature in your application. Robustness ensures longevity.
- Teach-in/Mode Selection: Most modern intelligent PE sensors feature simple push-button teaching or mode selection via teach wire to set the detection threshold or window quickly.
For engineers battling unreliable detection caused by ambient light, challenging surfaces, varying colors, or background interference, the PE sensor is not merely an alternative – it’s often the definitive solution. By harnessing the power of phase-shift analysis, it delivers the robustness, precision, and unwavering reliability needed to optimize processes, minimize costly downtime, and ensure quality in the most demanding sensing applications. This is detection engineered to overcome.