датчик индуктивного кольца
- time:2025-07-23 12:08:54
- Нажмите:0
Inductive Ring Sensors: Unseen Guardians of Industrial Precision
Imagine an industrial robot arm seamlessly placing components on a circuit board, a high-speed conveyor flawlessly sorting metal parts, or a CNC machine repeating cuts with micron-level accuracy. Behind these feats of automation, often unseen but critically important, lies a dependable workhorse: the датчик индуктивного кольца. Far from simple proximity switches, these sensors are sophisticated devices enabling precise, reliable, and non-contact detection of metallic objects, forming an invisible backbone of modern manufacturing and control systems.
Understanding the Core Principle: It’s All About Electromagnetism
An датчик индуктивного кольца operates on the fundamental principles of electromagnetic induction. It typically consists of three core elements housed within a robust, ring-shaped enclosure:
- An Oscillator Circuit: This generates a high-frequency alternating current.
- A Coil: This coil, wound concentrically and forming the “ring” structure, transforms the oscillator’s current into a stable, oscillating electromagnetic field that radiates from the sensor’s face.
- A Signal Evaluation Circuit: This intelligent component continuously monitors the state of the electromagnetic field generated by the coil.
Here’s the crucial interaction: When a metallic object (typically ferromagnetic materials like iron or steel, or also non-ferrous metals like aluminum, copper, or brass, though detection distance varies) enters the active zone of this electromagnetic field, something fascinating happens.
Eddy currents are induced on the surface of the target metal. These circulating currents create their own opposing electromagnetic field. This interaction detunes the original field generated by the sensor’s coil. The result? A measurable change occurs within the sensor’s oscillator circuit – often a reduction in amplitude or a shift in frequency.
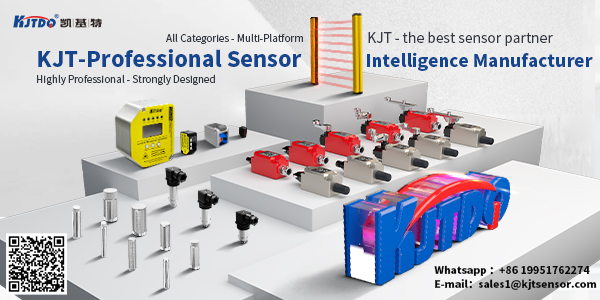
The evaluation circuit is constantly on guard. It detects this specific change induced by the eddy currents and triggers a switching output – typically changing from “OFF” to “ON” (or vice-versa, depending on sensor type and configuration). This output signal is then used by the control system (PLC, robot controller, etc.) to know that an object is present. Crucially, this detection happens without any physical contact between the sensor and the target object.
Why Choose an Inductive Ring Sensor? The Compelling Advantages
The non-contact nature of inductive ring sensors unlocks a suite of significant advantages over mechanical switches or other sensing technologies in demanding industrial environments:
- Exceptional Durability & Long Service Life: With no moving parts to wear out or physical impact during detection, these sensors boast remarkable longevity. They are inherently immune to mechanical wear and tear, translating to lower maintenance costs and reduced downtime. This makes them incredibly robust and reliable.
- High Resistance to Environmental Contaminants: Unlike optical sensors that can be blinded by dust, dirt, oil, or coolant mist, or capacitive sensors affected by moisture, inductive sensors are largely immune to such common environmental factors. Their sealed construction allows them to perform flawlessly in dirty, wet, greasy, or dusty conditions where other sensors would falter. This resilience is vital for harsh manufacturing floors.
- High Switching Frequencies and Speed: Capable of detecting objects at remarkable speeds – often thousands of times per second – inductive sensors are perfect for high-speed automation lines, packaging machinery, and sorting systems where rapid object detection is critical for throughput and efficiency.
- Position Sensing Accuracy: Modern sensors offer impressive repeatability (often within microns). Combined with their ability to detect minute position changes, they provide highly precise feedback for control loops in applications like robotic guidance, valve positioning, or verifying part placement.
- Target Material Versatility: While optimized for metals, their ability to detect a wide range of metallic objects (ferrous and often non-ferrous) adds significant flexibility. Specific sensor variants can be tuned for optimal performance with different metal types.
- Simplified Installation: Their ring shape allows for bracket-free mounting in many scenarios. Objects simply need to pass through the ring aperture, enabling straightforward integration around shafts, rods, pipes, or fast-moving parts for tasks like counting, speed monitoring, or end-position detection. Mounting brackets are only required for structural support, not necessarily for positioning relative to the target path.
Where Do They Shine? Key Applications
The unique blend of reliability, durability, non-contact operation, and position sensing capability makes inductive ring sensors indispensable across numerous sectors:
- Промышленная автоматизация: The primary battlefield. Used extensively for object detection on conveyors (verifying presence, counting), robotic tooling guidance and position feedback, verifying part clamping or fixturing, end-of-stroke detection in cylinders, spindle orientation in machine tools, and detecting tool breakage or presence in CNC machining centers. Their robustness shines in assembly lines.
- Material Handling & Packaging: Counting cans, bottles, or metal parts on high-speed lines; detecting metallic components in packaging; verifying the position of grippers or arms.
- Automotive Manufacturing: From engine assembly (detecting pistons, crankshafts, valves) to final assembly line positioning, these sensors ensure precision and process reliability in one of the most demanding environments.
- Machine Tooling: Monitoring spindle position, detecting tool holders in magazines, verifying chuck closure, and safeguarding against collisions. Their resistance to coolant and metal chips is paramount here.
- Rolling Mills & Metal Processing: Detecting the leading edge of metal sheets, monitoring roll position, and verifying the presence of billets in high-temperature and physically demanding settings.
- Safety Systems: Used as part of safety interlocks to verify guard closures are secured with a metal fastener in place, or to detect the position of safety doors on machinery.
- Food & Beverage (Limited Scope): Primarily for detecting metal contaminants (tramp metal) within products or packaging using specialized versions, though direct food contact is rare due to materials regulations.
Selecting the Right Ring Sensor: Key Considerations
Choosing the optimal inductive ring sensor requires careful consideration:
- Target Material: Ferrous metals offer the longest detection ranges. Detection of non-ferrous metals like aluminum, copper, or brass is possible but requires specific sensor designs (often with reduced range) – check manufacturer specifications carefully.
- Housing & Size: The ring’s inner diameter must be larger than the item passing through it. Consider available space and potential mounting constraints. Housing material (e.g., stainless steel, nickel-plated brass, PBT plastic) should suit the environmental conditions (chemical exposure, temperature).
- Switching Distance: The rated operating distance for the specific target material. Ensure it meets the application’s positional requirements.
- Electrical Output: NPN or PNP? Normally Open (NO) or Normally Closed (NC)? Voltage rating? Must match the input requirements of the control system (PLC/counter).
- Environmental Factors: Temperature range, pressure, IP rating (for dust/water ingress protection), resistance to chemicals or coolants.
- Response Frequency: How quickly can the sensor detect objects passing by? Critical for high-speed applications.
The Unmatched Value of Non-Contact Detection
Inductive ring sensors are far more than mere switches; they are sophisticated, electromagnetic guardians of precision and reliability. By harnessing the power of eddy currents and offering rugged, contactless operation, they solve critical object detection and position sensing challenges in environments where traditional methods fail. Their ability to deliver high accuracy, withstand harsh industrial conditions, and operate at high speeds makes them an essential, often invisible, component driving efficiency and automation on factory floors worldwide. From verifying the simplest presence to enabling complex robotic movements, the inductive ring sensor remains a cornerstone of modern industrial sensing technology.