Фотоэлектрический лазерный датчик
- time:2025-07-23 11:53:35
- Нажмите:0
Photoelectric Laser Sensors: The Invisible Guardians of Automation Precision
How often do you consider the unseen technologies ensuring the smooth operation of the factories producing your daily goods? Chances are, photoelectric laser sensors play a crucial, albeit hidden, role. These sophisticated devices form the bedrock of modern industrial automation, providing unparalleled non-contact detection capabilities essential for efficiency, safety, and quality control. Understanding their function and advantages reveals why they are indispensable in countless applications.
At its core, a photoelectric laser sensor operates on a brilliantly simple principle: emitting light and detecting changes in its reception. Unlike their incandescent or LED-based counterparts, these sensors utilize a highly focused, coherent laser beam as the light source. This laser emitter sends out a concentrated stream of photons towards a target. A receiver component, positioned according to the sensor type, then analyzes the light signal. Detection occurs based on the presence or absence of the light beam at the receiver, or significant modulations in its intensity caused by the target interrupting or reflecting the beam.
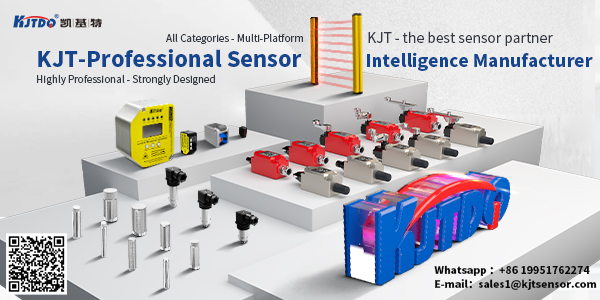
The exceptional nature of photoelectric laser sensors stems directly from the unique properties of laser light: coherence, collimation, and monochromaticity. Coherence means the light waves are perfectly in phase, collimation ensures the beam remains tightly focused over remarkable distances with minimal divergence, and monochromaticity guarantees a single, specific wavelength. This combination delivers decisive advantages:
- Exceptional Detection Range & Precision: The concentrated laser beam can travel significantly farther than standard light sources while maintaining accuracy. It enables the detection of minute objects or very small positional changes, often achieving sub-millimeter precision. This is vital for high-precision manufacturing and assembly.
- Pinpoint Accuracy & Small Spot Size: The laser generates an extremely small, well-defined light spot. This allows for precise object detection, even in confined spaces, or discerning between closely spaced components where a larger light spot would cause ambiguity. Targeting specific features on tiny parts becomes feasible.
- Enhanced Reliability in Challenging Environments: The high intensity and focused nature of the laser beam offer superior resistance to interference from ambient light compared to standard light sources. This results in consistent and reliable operation in various factory lighting conditions. The focused beam is also less susceptible to contamination on the sensor lens compared to diffused light, enhancing durability.
Photoelectric laser sensors primarily function in three distinct detection modes, each suited to specific application challenges:
- Through-Beam Sensing (Opposed Mode): The gold standard for long-range and highly reliable detection. The laser emitter and receiver are mounted opposite each other. Detection occurs when the target object interrupts the beam traveling directly from the emitter to the receiver. This method offers the longest sensing ranges and highest immunity to target surface characteristics (color, reflectivity) or environmental factors like dust or steam.
- Retroreflective Sensing: Here, the emitter and receiver are housed in the same unit. The emitted laser beam is directed towards a special reflector (corner-cube or tape type) which efficiently bounces the beam directly back to the receiver. Detection happens when the target object breaks this reflected beam path. This mode simplifies installation (only one device to mount and wire, plus the reflector) and provides good range and reliability, though less than through-beam.
- Diffuse Reflective Sensing (Proximity Mode): The emitter and receiver are again co-located within the same sensor head. The sensor works by detecting the laser light scattered (diffusely reflected) back from the surface of the target object itself – no separate reflector is needed. While offering the simplest installation (only one device), this mode is most sensitive to target surface color, reflectivity, texture, and angle. Sensing range is typically shorter than the other methods, and detection reliability can vary significantly based on target properties. However, advanced background suppression (BGS) and foreground suppression (FGS) technologies have dramatically improved the performance of diffuse laser sensors, allowing them to reliably ignore distant or close backgrounds.
The capabilities of photoelectric laser sensors make them ubiquitous across industries:
- Precision Positioning & Gauging: Verifying minute component positions in electronics assembly, measuring tiny gaps or steps, controlling web tension in printing or converting.
- Object Detection & Counting: High-speed counting of small products (pills, fasteners), detecting presence/absence of labels, caps, or components on high-speed lines with laser precision.
- Web & Edge Guidance: Tracking edges of materials (film, paper, metal) for guiding systems in continuous processing lines.
- Level Detection: Monitoring fill levels in transparent or opaque containers without contact.
- Robotics & Automated Guided Vehicles (AGVs): Providing precise object detection and localization for robotic arms (pick-and-place) and navigation/safety for AGVs.
- Packaging & Bottling: Ensuring proper container filling, cap presence, label application, and case packing verification.
- Security & Access Control: Used in safety light curtains, intrusion detection systems in sensitive areas, and high-security perimeter monitoring.
Selecting the optimal photoelectric laser sensor involves evaluating several critical factors:
- Detection Mode: Based on required range, target characteristics, and installation constraints (through-beam for max range/reliability, diffuse for simplicity on opaque targets, retroreflective as a balance).
- Required Sensing Range: Laser sensors excel here, but specific needs dictate choice.
- Target Characteristics: Size, color, surface finish (shiny, matte), material (transparent/opaque). Diffuse sensors are highly sensitive to these; through-beam largely is not.
- Environmental Conditions: Dust, steam, temperature extremes, vibration, electrical noise, and ambient light levels. Look for appropriate Ingress Protection (IP) ratings.
- Required Resolution & Spot Size: For detecting tiny objects or precise positioning, a small laser spot is crucial.
- Output Requirements: Discrete on/off (PNP/NPN) or analog (e.g., 4-20mA, 0-10V) for distance measurement? Some lasers offer switching and analog outputs.
- Response Time: How quickly must the sensor react? Laser sensors typically offer very fast response times, essential for high-speed lines.
In the relentless pursuit of industrial efficiency, quality, and safety, the photoelectric laser sensor stands as a testament to the power of focused light. From enabling the microscopic precision needed in semiconductor manufacturing to ensuring bottles are filled correctly on high-speed lines, these devices operate silently and reliably. Their ability to provide non-contact, high-precision detection over long distances, coupled with the inherent advantages of laser technology, ensures they will remain fundamental components powering the automated world. Choosing the right sensor type and configuration unlocks their full potential as indispensable tools for modern manufacturing and beyond.