autonics inductive proximity sensor
- time:2025-07-12 01:38:37
- Нажмите:0
Autonics Inductive Proximity Sensors: The Unsung Heroes of Robust Industrial Sensing
Imagine a high-speed production line bottling beverages. Thousands of containers whiz by every hour. How does the system know when a bottle is perfectly positioned for filling, without ever touching it? How does it count precisely, detect jams instantly, or confirm a metal component is present? More often than not, the silent workhorse enabling this flawless, non-contact detection is the индукционный датчик приближения, and Autonics has built a formidable reputation for delivering exceptionally reliable ones.
In the demanding world of industrial automation, where milliseconds matter, environments are harsh, and reliability is non-negotiable, non-contact sensing is paramount. This is the core domain of inductive proximity sensors. They detect the presence or absence of metallic objects – ferrous metals like iron and steel, and often non-ferrous metals like aluminum, brass, and copper – without any physical contact. This eliminates wear-and-tear, provides incredibly fast response times, and ensures long operational life, making them indispensable across countless applications in manufacturing, packaging, material handling, and beyond.
Autonics: Precision Engineered Sensing Solutions
As a global leader in industrial automation components, Autonics has cultivated deep expertise in sensor technology. Their range of inductive proximity sensors is engineered to meet the rigorous demands of modern industry. Built with high-quality materials and subjected to stringent quality control, Autonics sensors are synonymous with durability, accuracy, and consistent performance, even in challenging conditions characterized by dust, moisture, vibration, and extreme temperatures.
Decoding the Core Technology: How Autonics Inductive Sensors Work
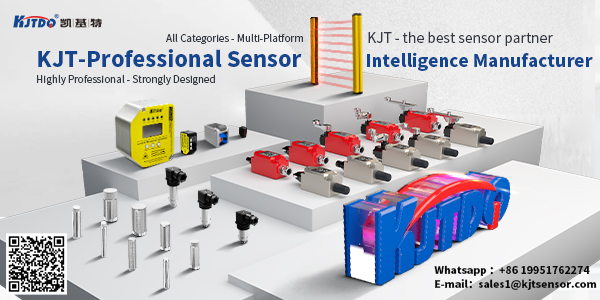
The fundamental principle is elegantly simple yet incredibly effective. Inside every inductive proximity sensor lies a coil energized by a high-frequency oscillating current. This generates a dynamic electromagnetic field emanating from the sensor’s active face. When a metallic target enters this field, eddy currents are induced on the surface of the metal. These eddy currents draw energy from the sensor’s oscillating circuit, causing a detectable change – a reduction in the oscillation’s amplitude.
The sensor’s sophisticated internal electronics continuously monitor this oscillation. When the change exceeds a predefined threshold, signifying that a metal object is within the designated sensing distance, the sensor electronically switches its output state. This instantaneous signal change (e.g., from OFF to ON, or vice-versa, depending on configuration) is then communicated to the control system (like a PLC), triggering actions such as starting a conveyor, actuating a cylinder, initiating a count, or stopping a process due to a missing part. The key advantages? Zero physical contact, high-speed response (often in microseconds), immunity to surface conditions (oil, dust), and exceptional reliability.
Key Features Defining Autonics Inductive Proximity Sensors
Autonics designs its sensors with a focus on versatility and ruggedness, incorporating features that directly address real-world industrial needs:
- Прочная структура: Housed in rugged materials like nickel-plated brass or stainless steel, many models boast impressive IP67, IP68, IP69K, or even IP69K ratings. This translates to excellent resistance against water jets, high-pressure washdowns, dust ingress, oils, and coolants, making them ideal for food processing, automotive, and outdoor applications.
- Shielding Matters: Autonics offers both shielded (flush-mountable) and unshielded (non-flush) types. Shielded sensors can be mounted flush with surrounding metal surfaces without affecting their sensing field, offering neat installation and protection against physical damage. Unshielded types provide a longer nominal sensing range but require a specific clearance area around them.
- Varied Sensing Distances: Catering to diverse application requirements, Autonics provides sensors with a wide range of nominal sensing distances (Sn), from just 1mm or 2mm for ultra-precise positioning up to 40mm or more for detecting larger objects or providing greater installation flexibility. Selection based on the specific target size and required margin is crucial.
- Output Configuration Flexibility: Available as НС (sourcing) or ПНП (sinking) outputs, with both Normally Open (NO) and Normally Closed (NC) logic options. This ensures compatibility with virtually any PLC or control system input card.
- LED Status Indication: A built-in LED provides visual confirmation of the sensor’s operating state (power-on and switching status), significantly simplifying installation, commissioning, and troubleshooting on the factory floor.
- Temperature Resilience: Engineered to perform reliably across a broad operating temperature range (typically -25°C to +70°C, with specialized models going beyond), ensuring stability in foundries, cold storage, and other thermally demanding environments.
- Short-Circuit & Overload Protection: Integrated protection circuits safeguard the sensor against accidental wiring errors (like short circuits) and electrical surges, enhancing overall system uptime and reducing the risk of sensor failure.
Diverse Applications: Where Autonics Inductive Sensors Excel
The reliability and non-contact nature of Autonics inductive proximity sensors make them ubiquitous in automation:
- Position Verification: Confirming the presence or correct positioning of metal parts on assembly lines, machining centers (“part in place”), robotic arms, and automated guided vehicles (AGVs).
- End-of-Stroke Detection: Accurately sensing the extended or retracted position of pneumatic and hydraulic cylinders.
- High-Speed Counting: Reliably counting metal objects like cans, bottles (via cap detection), or machined components moving rapidly on conveyors. Their speed is unmatched for such tasks.
- Liquid Level Control: Detecting metal floats inside tanks or vessels to monitor fluid levels.
- Machine Safety: Used in simple interlock circuits to confirm machine guards are closed before operation begins.
- Speed Monitoring: Detecting teeth on rotating gears or sprockets to measure rotational speed.
- Перевозка материалов: Monitoring the position of metal carriers, lifts, and cranes.
- Packaging Machinery: Controlling sequences involving metallic machine elements, detecting foil lids, or verifying metal components in packaging.
Why Choose Autonics? The Distinct Advantages
Beyond the fundamental technology, opting for Autonics inductive proximity sensors brings specific benefits:
- Proven Reliability & Longevity: Rigorous manufacturing and testing result in sensors that operate dependably for millions of cycles, minimizing unplanned downtime – a critical factor in continuous production environments. Their robustness directly impacts the bottom line.
- Consistent Performance: Tight tolerances ensure uniform sensing characteristics across batches, guaranteeing predictable results in automated processes.
- Global Support & Availability: A well-established global distribution network ensures accessibility and technical support when needed.
- Wide Product Range: Whether you need a tiny M5 sensor for confined spaces, a high-temperature variant, a long-range detector, or a sensor with extra EMI resistance, Autonics likely has a model specifically designed for the challenge. Exploring the AI series or E2E series highlights this breadth.
- Excellent Price-to-Performance Ratio: Autonics delivers high-quality industrial-grade sensing performance at highly competitive price points, offering significant value.
Implementing Autonics Sensors: Key Considerations
To maximize performance and reliability:
- Select the Correct Sensing Distance (Sn): Always choose a sensor where the nominal sensing distance (Sn) exceeds the maximum operating gap you require. Account for temperature fluctuations and target material variations (e.g., aluminum typically reduces Sn compared to steel).
- Mind the Target Size: Ensure the target is large enough relative to the sensor’s face to trigger it reliably. Most sensors specify a minimum target size for the rated sensing distance