индукционный датчик
- time:2025-07-12 01:03:25
- Нажмите:0
Inductive Type Sensors: Precisely Sensing the Movement of Metal Objects
Look around. From the smartphone assembly line to the robotic arm welding a car frame, countless machines operate with seamless motion. This intricate dance relies heavily on sensors acting as the “eyes” of automation, constantly feeding data about position, proximity, and crucially, movement. Among these essential components, inductive proximity sensors stand out for their remarkable ability to reliably detect the movement of metal objects without physical contact, operating silently yet effectively in demanding industrial environments. But how exactly do these robust devices translate the passage of metal into actionable signals? Let’s delve into the electromagnetic principles that make it possible.
Understanding the Inductive Sensor Core: Electromagnetic Fields at Work
At its heart, an inductive sensor is a purely electronic device designed for non-contact sensing. Its primary function is to detect the presence or absence of metallic objects (typically ferrous metals like iron and steel, but also non-ferrous metals like aluminum or copper, depending on the sensor type) within its detection range. Unlike optical or capacitive sensors, inductive sensors rely entirely on magnetic fields generated by an internal coil.
The core components of a typical inductive proximity sensor are:
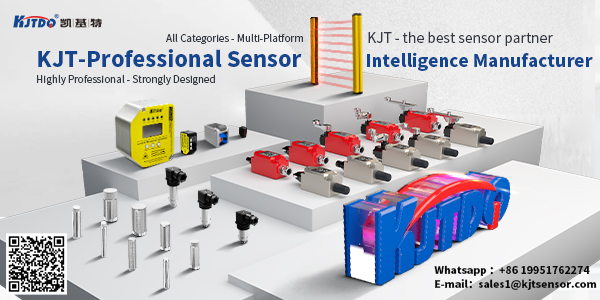
- An Oscillator: Generates a high-frequency alternating current (AC).
- A Coil (Windings): Conducts the oscillator’s current, producing a rapidly oscillating electromagnetic field that radiates outwards from the sensor’s active face.
- A Signal Evaluation Circuit: Monitors the state of the oscillator circuit.
- An Output Stage: Switches (Solid State Relay or Transistor) when a target is detected, providing a binary (ON/OFF) signal.
The Fundamental Principle: Presence Detection
The magic happens when a conductive metal target enters this electromagnetic field. As the metal object approaches the sensor face, the oscillating magnetic field induces small circulating electrical currents, known as eddy currents, within the body of the metal target itself. These eddy currents are not random; they generate their own opposing magnetic field, effectively interacting with the original field generated by the sensor’s coil.
This interaction causes a measurable change in the characteristics of the sensor’s internal oscillator circuit – specifically, a reduction in oscillation amplitude (or sometimes a frequency shift, depending on the sensor design). The sensor’s built-in evaluation circuit is meticulously tuned to detect this precise change. Once the amplitude drops below a predetermined threshold (indicating the target is sufficiently close), the circuit triggers the output stage to change state. For example, it might switch from “OFF” (no target present) to “ON” (target detected). This is the fundamental mechanism of presence detection.
From Presence to Movement: The Critical Output Signal
While the fundamental physics detect presence at a specific location, it’s the real-time changes in the sensor’s output signal that enable us to sense movement. Here’s how it translates:
- Threshold Crossing: Movement implies that the target is changing its position relative to the sensor. As the target moves into the sensor’s detection range, it crosses the activation threshold, causing the output to switch ON. Conversely, as the target moves out of the detection range, it crosses the deactivation threshold, causing the output to switch OFF.
- Signal Changes Indicate Transition: Each change in the sensor’s output state (OFF to ON or ON to OFF) represents a specific positional transition point of the target relative to the sensor. A single change indicates the target arrived or departed. Repeated ON-OFF cycling of the output signal is the primary indicator of movement passing by the sensor.
- Speed and Frequency: The rate at which these output changes occur provides information about the speed of the moving target. A faster object will trigger state changes more frequently as it crosses the sensor’s detection zone. Counting these transitions over time allows calculation of speed or distance traveled (if the sensor detects individual objects, like parts on a conveyor).
- Direction Inference (With Multiple Sensors): While a single inductive sensor primarily detects movement across its sensing field, strategically placing multiple sensors in sequence allows systems to infer the direction of movement. The sequence in which sensors are triggered (Sensor A then Sensor B, or vice versa) clearly indicates the path of travel.
Key Strengths for Movement Sensing Applications
Inductive sensors shine in applications demanding robust, reliable movement detection of metal objects:
- Robustness & Reliability: With no moving parts and sealed housings (often IP67/IP68 rated), they withstand harsh industrial environments – dirt, dust, oil, vibration, even washdowns – where mechanical switches or optical sensors might fail. Their immunity to non-metallic contaminants is crucial.
- Non-Contact Operation: The absence of physical contact significantly reduces wear and tear on both the sensor and the target, leading to virtually unlimited operational life and eliminating friction-related failures.
- High Switching Frequencies: Modern inductive sensors boast very high response speeds (switching frequencies in the hundreds of Hz or even kHz). This allows them to accurately track very rapid movement, such as counting fast-moving components on high-speed production lines or monitoring the rotation of machinery shafts.
- Cost-Effectiveness: They offer excellent performance and durability at a relatively low cost compared to many other sensing technologies suitable for industrial environments.
- Simplicity: Providing a simple, clean digital (ON/OFF) output makes them easy to integrate into control systems like PLCs (Programmable Logic Controllers).
Diverse Applications: Where Sensing Metal Movement Matters
The ability to reliably detect the movement of metal objects makes inductive sensors indispensable across numerous sectors:
- Manufacturing Automation: Counting parts on conveyor belts, detecting position of machine slides/arms, verifying gripper closure (has the part been picked up?), monitoring the passage of metal components through assembly stages.
- Packaging Machinery: Detecting the presence or absence of metal lids/caps on containers moving down the line.
- Перевозка материалов: Sensing the position of metal racks, pallets, or lifts; confirming tray or drawer closure; detecting end-of-stroke on cylinders.
- Automotive: Monitoring the rotation speed of engine components (e.g., camshafts, transmission gears - often using specialized inductive “gear tooth” sensors), detecting pedal position, verifying door/hatch closure status.
- Metalworking (CNC Machining): Tool breakage detection (sudden absence where presence is expected), verifying workpiece clamping, detecting the position of turrets or tool changers.
- Conveyor Systems: Object detection for sorting, speed control