Тип индукционного датчика
- time:2025-07-12 00:42:20
- Нажмите:0
Inductive Sensor Types: Understanding Varieties and Applications
In the intricate dance of modern automation, where machines perform tasks with astonishing precision, a silent orchestra of sensors provides the essential feedback. Among these crucial components, inductive sensors stand out as robust, reliable, and incredibly versatile workhorses. But what exactly are the different types of inductive sensors, and how do they shape the capabilities of countless systems? This article unravels the key varieties of inductive sensors, demystifying their principles and showcasing their diverse industrial roles.
The Core Principle: Electromagnetic Induction in Action
Before diving into specific types, it’s vital to grasp the common thread binding all inductive sensors. They operate based on Faraday’s Law of Electromagnetic Induction. Simply put, they generate an oscillating electromagnetic field from a coil. When an electrically conductive target (typically metal) enters this field, it induces small electrical currents – called eddy currents – within the target itself. These eddy currents generate their own opposing electromagnetic field, which interacts with the sensor’s original field. This interaction alters the sensor’s coil properties (like its inductance or oscillation amplitude). The sensor’s built-in electronics detect this change and convert it into a clean electrical output signal, typically indicating the presence or absence of the target, or measuring its distance. Crucially, this detection occurs without physical contact, making these sensors highly durable and wear-resistant.
Key Inductive Sensor Types and Their Distinctions
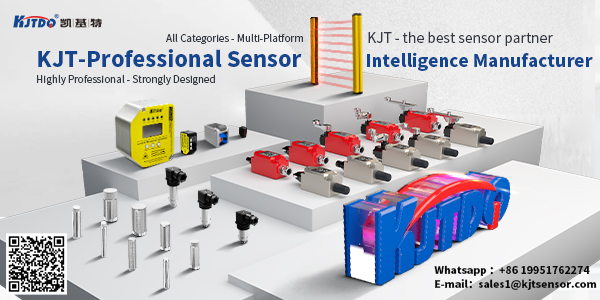
While sharing the foundational principle, inductive sensors are categorized based on their specific design focus and output characteristics. The primary types are:
- Inductive Proximity Sensors (IP Sensors):
- Core Function: Detection of metallic object presence (or absence) within a defined range.
- Output Type: Primarily digital output (ON/OFF, PNP, NPN configurations). They act as proximity switches.
- Operation: The sensor continuously generates an electromagnetic field. When a metallic target enters its sensing range (switching distance), the resultant change in the oscillator’s amplitude is detected. The sensor’s internal circuit triggers its output state to switch (e.g., from OFF to ON).
- Key Characteristics:
- Target Material Sensitivity: Typically categorized based on the standard target material – usually mild steel. Factors like target size, shape, and specific material type (ferrous vs. non-ferrous metals like aluminum, brass, copper) significantly affect the sensing distance. Shielded sensors have a reduced range but can be mounted flush with metal surfaces; Unshielded sensors offer longer ranges but require more mounting clearance.
- Robustness: Highly resistant to dirt, dust, moisture, vibration, and harsh environments.
- Многогранность: Widely used for position detection (e.g., cylinder end-position), object counting, and end-stop verification in machinery.
- Inductive Displacement Sensors / Linear Position Sensors:
- Core Function: Precise, continuous measurement of the distance (displacement) between the sensor face and a conductive target.
- Output Type: Analog output (e.g., 4-20 mA, 0-10 VDC) proportional to the measured distance. Digital outputs like IO-Link are also common for data-rich applications.
- Operation: Similar to proximity sensors in generating an electromagnetic field, but displacement sensors are designed and calibrated specifically to provide a linear relationship between the target distance and the output signal. High resolution and accuracy are paramount. They continuously measure the effect on the electromagnetic field (often using a differential coil design) as the target moves within their defined measuring range.
- Key Characteristics:
- Precision: Engineered for high linearity and repeatability, often down to micrometer resolution.
- Measuring Range: Varies significantly, from fractions of a millimeter to several tens of millimeters.
- Target Sensitivity: Performance depends heavily on the target material and size. Calibration is often needed for specific applications.
- Применение: Precise position feedback in hydraulic/pneumatic cylinders, vibration monitoring, bearing clearance measurement, thickness gauging of non-conductive materials over a conductive base, and runout detection.
- Eddy Current Sensors:
- Core Function: A specialized subset of inductive displacement sensors, often optimized for very high resolution, high-frequency response, and non-ferromagnetic target materials.
- Output Type: Analog output (typically 0-10 VDC or ±10 VDC).
- Operation: They rely heavily on the generation and detection of eddy currents in the target material. The sensor probe contains a coil driven at high frequency. The strength of the eddy currents induced in the target is inversely proportional to the distance. Changes in distance cause measurable changes in the coil’s impedance (resistance and inductance), which the sensor electronics convert into a proportional voltage output.
- Key Characteristics:
- High Resolution/Frequency: Capable of sub-micrometer resolution and bandwidths reaching tens or hundreds of kilohertz.
- Material Independence (Relative): Generally less sensitive to the electrical properties of the target material than standard inductive displacement sensors, though calibration for the specific material is still crucial for accuracy. Often perform exceptionally well on non-ferrous metals like aluminum and copper.
- Small Spot Size: Allows for measurement on small targets or specific features.
- Применение: Vibration analysis in turbines, motors, and gearboxes; precise gap measurement; runout and eccentricity monitoring; surface profiling; conductivity and coating thickness measurements.
Choosing the Right Sensor: Application Dictates Type
The selection of the appropriate inductive sensor type hinges entirely on the specific application requirement:
- Do you simply need to know “Is the metal part there or not?” An индукционный датчик приближения is the most cost-effective and straightforward solution. Its robust digital output is ideal for counting, position verification, and limit switching.
- Do you need exact distance or position information? An Inductive Displacement Sensor (or Linear Position Sensor), providing a continuous analog or digital position reading, is essential. This is crucial for closed-loop control systems demanding precision.
- Is very high resolution, high-frequency measurement required, especially on non-ferrous targets? An Eddy Current Sensor is likely the optimal choice, excelling in demanding vibration and precision measurement tasks.
Material Matters Across All Types
Regardless of type, the inherent material sensitivity of inductive sensors is a critical design consideration. The sensing performance (switching distance for proximity, linearity, and range for displacement) is profoundly influenced by the electrical conductivity and magnetic permeability of the target material. Ferrous materials (like iron, steel) generally yield the longest ranges/proximity and strongest signals due to their magnetic properties. Non-ferrous metals (aluminum, copper) induce weaker signals/shorter ranges. Sensor specifications always refer to a standardized target material (usually mild steel), and actual performance with a different material must be carefully evaluated or compensated for via calibration or sensor settings.
Conclusion: The Pillars of Non-Contact Sensing
From the simple presence detection of an inductive proximity switch on a conveyor line, to the micrometer-level precision of an eddy current sensor monitoring the vibrations of a high-speed spindle, the different Тип индукционного датчика form the bedrock of reliable, non-contact sensing in industrial automation. Understanding the distinctions between proximity, displacement, and eddy current sensors empowers engineers and technicians to select the perfect tool for the job, ensuring optimal performance, longevity, and efficiency across countless applications. Their inherent robustness, immunity to environmental factors, and contactless operation solidify their indispensable role in shaping the automated world.