высокоскоростной индукционный датчик приближения
- time:2025-07-12 00:28:16
- Нажмите:0
High-Speed Inductive Proximity Sensors: The Unseen Engines of Rapid Automation
Imagine a production line where components whizz by faster than the eye can track, robotic arms dance with millisecond precision, and every pause or misalignment spells costly downtime. Capturing the position or presence of objects reliably at these blistering speeds demands sensing technology that’s equally swift and robust. Enter the high-speed inductive proximity sensor – the silent, indispensable guardian of efficiency in high-velocity automation.
Beyond the capabilities of standard inductive sensors, these specialized variants are engineered for one paramount goal: ultra-fast detection and switching. While their fundamental operating principle remains based on electromagnetic induction – generating an oscillating field disrupted by the approach of a conductive target – their internal circuitry and design are optimized to minimize response time and maximize switching frequency. Understanding this distinction is crucial for applications demanding peak performance.
The Heart of the Speed: How They Achieve Velocity
The core advantage lies in the sensor’s ability to react immediately to the presence or absence of a target. Key factors enabling high speed include:
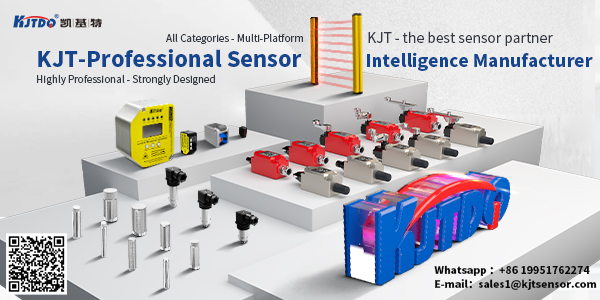
- Advanced Oscillator Circuitry: High-frequency oscillators react quicker to changes in the electromagnetic field caused by the target. This translates directly to faster detection.
- Optimized Signal Processing: Sophisticated electronics process the signal change caused by the target intrusion with minimal delay, filtering out noise efficiently to prevent false triggers while maintaining speed.
- Reduced Hysteresis: Hysteresis is the difference in distance between the point where the sensor detects the target approaching and where it detects it leaving. High-speed sensors minimize this difference, allowing for more precise and faster switching cycles, especially critical for small targets or tight positioning tolerances.
- Specialized Coil Design: The geometry and winding of the internal coil contribute significantly to the field shape and reaction speed.
Where Milliseconds Matter: Critical Applications
The non-contact nature of inductive sensors inherently avoids wear and tear. When combined with high speed, they become the preferred solution in numerous demanding scenarios:
- High-Speed Counting & Sorting: Reliably tracking items on conveyor belts moving several meters per second or sorting small parts based on presence/absence requires sensors capable of kHz switching frequencies (thousands of operations per second). High-speed inductive sensors excel here.
- Precision Assembly & Robotics: In automated assembly lines or robotic work cells, verifying component presence, checking robotic arm end-position, or detecting minute part movements happens in fractions of a second. Fast response times (often measured in microseconds) are non-negotiable for smooth, precise operation.
- Packaging Machinery: Bottle cap detection, label presence verification, film registration marks detection – these tasks occur at incredibly high packaging rates. Only sensors with minimal delay ensure flawless synchronization and zero jams.
- Printing & Converting: Register mark detection for aligning printing or cutting processes on fast-moving webs (paper, film, foil) demands sensors that can instantly recognize the mark and trigger downstream actions without lag.
- Machine Tool Monitoring: Monitoring tool position, detecting broken tools, or verifying workpiece clamping on CNC machines or presses requires rapid feedback for safety and process control.
Key Performance Metrics: Beyond “Just” Speed
When selecting a high-speed inductive proximity sensor, several critical specs interplay:
- Response Time: Defined as the time between the target entering the sensing range and the output signal switching. Typically measured in microseconds (µs) or milliseconds (ms) for high-speed variants. Lower values indicate faster response. (Example: 100 µs vs. 2 ms for a standard sensor).
- Switching Frequency (f_max): The maximum number of on/off switching cycles the sensor can reliably perform per second, measured in Hertz (Hz) or kiloHertz (kHz). (Example: 5 kHz equals 5,000 detections per second). This is vital for applications involving rapidly moving or closely spaced targets.
- Repeat Accuracy: The consistency of the switching point over repeated target approaches. High-speed sensors maintain tight tolerances even at speed.
- Sensing Range: While crucial, achieving maximum range can sometimes come at the cost of speed. Finding the optimal balance is key. High-speed sensors often have shorter nominal ranges than slower counterparts optimized purely for distance.
- Target Material: Primarily designed for ferrous metals (iron, steel) offering the strongest signal and longest range. However, many high-speed models also detect non-ferrous metals (aluminum, brass, copper) and even stainless steel, albeit often with a reduced sensing range.
- Robustness & Environmental Resistance: Immunity to electrical noise (EMC), resistance to vibration, shock, liquids (IP ratings), and temperature extremes remains essential, especially in harsh industrial environments.
Why Choose High-Speed Over Standard? The Performance Edge
The benefits of investing in high-speed inductive proximity sensors are clear for demanding applications:
- Unmatched Responsiveness: Enables reliable detection and control in ultra-fast processes impossible with slower sensors.
- Повышение точности: Minimal response delay and hysteresis allow for more accurate positioning and timing.
- Increased Throughput: Facilitates higher production speeds and machine cycle rates by eliminating sensor lag as a bottleneck.
- Improved Reliability: Consistent, fast switching reduces missed detections and false triggers, minimizing costly errors and downtime.
- Non-Contact Operation: Inherently wear-free, ensuring long service life and reduced maintenance.
Selecting the Right High-Speed Sensor: Considerations
Choosing the optimal sensor involves carefully evaluating your specific needs:
- Required Speed: What is the minimum acceptable response time or switching frequency? Test under actual or simulated conditions.
- Target: What material (steel, aluminum, SS)? What size and shape? Ensure the sensor can reliably detect it at the required speed and distance.
- Environmental Factors: Temperature range, presence of cutting fluids, coolants, dust, vibration? Choose the appropriate IP rating and robust housing.
- Mounting Constraints: Available space? Flush or non-flush mounting capability required?
- Output Type & Wiring: NPN/PNP? NO/NC? Voltage? Cable or connector type? Ensure compatibility with your control system.
When the relentless pace of modern automation demands sensing that keeps up without compromise, high-speed inductive proximity sensors are the proven solution. Their ability to deliver millisecond or even microsecond-level response, combined with inherent ruggedness and reliability, makes them the indispensable foundation for optimizing efficiency, maximizing throughput, and ensuring precision in the fastest production environments. Specifying the right high-speed sensor isn’t just about technology; it’s about empowering your machines to perform at their absolute peak.